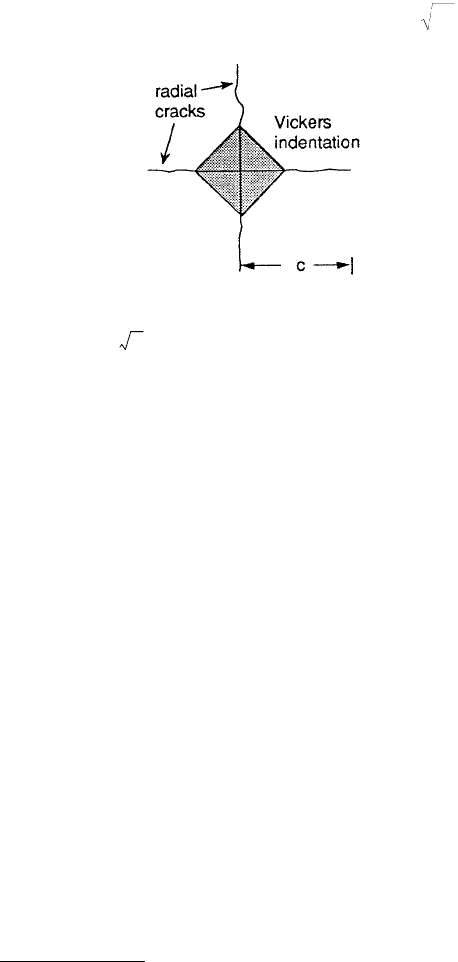
© 1999 by CRC Press LLC
of a material. The variations in stress exponent reflect the changes that may take place when the sub-
structure generated at high strain rate approaches equilibrium condition (Mayo and Nix, 1988a).
10.7.2 Nanofracture Toughness
Fracture toughness, K
Ic
of a material is a measure of its resistance to the propagation of cracks and the
ratio H/K
Ic
is an index of brittleness, where H is the hardness. Resistance to fracture is a strong function
of crack pattern. It is typically measured in a test in which a specimen containing a sharp crack of known
length, c, is subjected to an applied stress s, which is increased during test until the sample fractures
(Lawn, 1993), Figure 10.61. The magnitude of the stresses near the crack tip are determined by the stress
intensity factor K
I
which, in turn, depends on s, c, and the specimen geometry (A)
(10.30)
The term A provides correction for the thickness-to-width ratio of the material. Units of stress-intensity
factor are MPa . With more intense stress or with deeper cracks, the stress intensity becomes sufficient
for the fracture to progress spontaneously. This threshold stress intensity is a property of the material
and is called the critical stress intensity factor, K
Ic
, or the fracture toughness of the material. Ceramics
generally have relatively low fracture toughness, consequently, it is an important property to be considered
for the selection of ceramics for industrial applications.
Indentation fracture toughness is a simple technique for determination of fracture toughness (Palm-
quist, 1957; Lawn and Wilshaw, 1975; Evans and Charles, 1976; Lawn and Evans, 1977; Lawn and Marshall,
1979; Lawn et al., 1980; Antis et al., 1981; Chantikul et al., 1981; Chiang et al., 1981, 1982; Henshall and
Brookes, 1985; Cheng et al., 1990; Cook and Pharr, 1990; Choi and Salem, 1993; de Boer et al., 1993;
Lawn, 1993; Pharr et al., 1993; Bhushan et al., 1996). The indentation cracking method is especially useful
for measurement of fracture toughness of thin films or small volumes. This method is quite different
from conventional methods in that no special specimen geometry is required. Rather, the method relies
on the fact that when indented with a sharp indenter, most brittle materials form radial cracks and the
lengths of the surface traces of the radial cracks (for definition of crack length, see Figure 10.62) have
been found to correlate reasonably well with fracture toughness. By using simple empirical equations,
fracture toughness can then be determined from simple measurement of crack length.
In microindentation, cracks at relatively high indentation loads of several hundred grams are on the
order of 100 µm in length and can be measured optically. However, to measure toughness of very thin
films or small volumes, much smaller indentations are required. However, a problem exists in extending
the method to nanoindentation regime in that there are well-defined loads, called cracking thresholds,
below which indentation cracking does not occur in most brittle materials (Lankford, 1981). For a Vickers
indenter, cracking thresholds in most ceramics are about 25 g. Pharr et al. (1993), Li et al. (1997), and
Li and Bhushan (1998a) have found that the Berkovich indenter (a three-sided pyramid) with the same
depth-to-area ratio as a Vickers indenter (a four-sided pyramid) has a cracking of the thresholds very
similar to that of the Vickers indenter. They showed that cracking thresholds can be substantially reduced
FIGURE 10.62 Schematic of Vickers
indentation with radial cracks.
KA c
I
=πσ
m