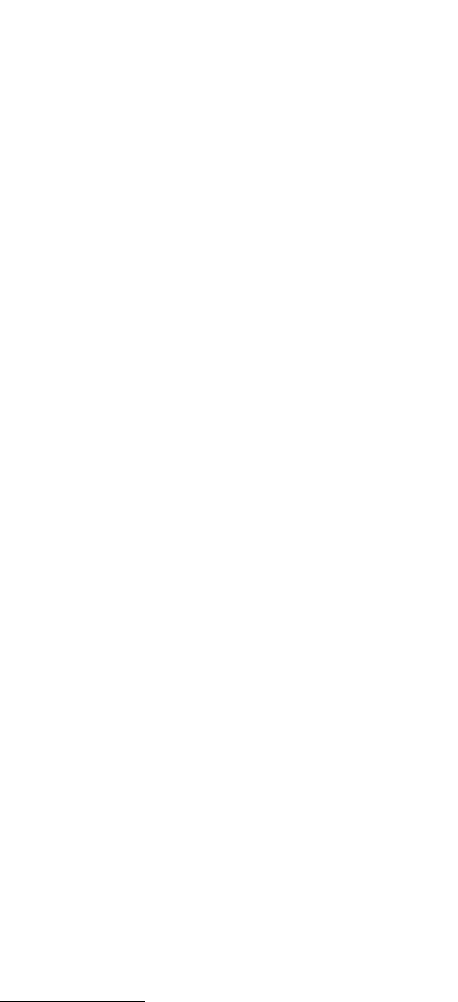
© 1999 by CRC Press LLC
where A is the Hamaker constant, R is the tip radius, D is the separation distance by the surface roughness
of the means of the tip and the sample surfaces, γ
t
and γ
d
are the surface energies of the tip and sample
surfaces, and D
0
~ 0.2 nm (Israelachvili, 1992). As a consequence of the strong 1/D
2
dependence, the tip
should experience a much weaker van der Waals force on the top of a summit as compared with that of
a valley. Mate (1993a) reported that a separation change ∆D of 5 nm would give a variation in the van
der Waals force by a factor of 5 if the distance of closest approach, approximately the amount of roughness
separation between the two surfaces, is 4 nm. Another component of the attractive adhesive force in the
presence of liquid film is the meniscus force. The meniscus force for a sphere on a flat in the presence
of liquid is
(14.9)
where γ
l
is the surface tension of the liquid. Meniscus force is generally much stronger than the van der
Waals force. Thus, the contribution of adhesion mechanism to the friction force variation is relatively
small for samples used in this study. Furthermore, the correlation between the surface and friction force
profiles is poor; therefore, an adhesion mechanism cannot explain the topography effects. The ratchet
mechanism already quantitatively explains the variation of friction.
Since the local friction force is a function of the local slope of sample surface, the local friction force
should be different as the scanning direction of the sample is reversed. Figures 14.13 and 14.15 show the
gray-scale plots of slope of roughness profiles and friction force profiles for a lubricated textured disk
and an MP tape, respectively. The left side of the figures corresponds to the tip sliding from the left
toward the right (or the sample sliding from the right to the left). We again note a general correspondence
between the surface roughness slope and the friction profiles. The middle figures in Figures 14.13 and
14.15 correspond to the tip sliding from the right toward left. We note that generally the points that have
high friction force and high slope in the left-to-right scan have low friction and low slope as the sliding
direction is reversed (Meyer and Amer, 1990; Grafstrom et al., 1993; Overney and Meyer, 1993; Bhushan
and Ruan, 1994e; Ruan and Bhushan, 1994b). This results from the slope being of opposite sign as the
direction is reversed, which reverses the sign of friction force contribution by the ratchet mechanism.
This relationship is not true at all locations. The right-side figures in Figures 14.13 and 14.15 correspond
to the left-hand set with sign reversed. On the right, although the sign of friction force profile is the
reverse of the left-hand profile, some differences in the right two friction force profiles are observed
which may result from the asymmetrical asperities and/or asymmetrical transfer of wipe material during
manufacturing of the disk. This directionality in microscale friction force was first reported by Bhushan
et al. (1994a,c,e, 1995a–d, 1997a, 1998).
If asperities in a sample surface have a preferential orientation, this directionality effect will be man-
ifested in macroscopic friction data; that is, the coefficient of friction may be different in one sliding
direction from that in the other direction. Such a phenomenon has been observed in rubbing wool fiber
against horn. It was found that the coefficient of friction is greatest when the wool fiber is rubbed toward
its tip (Mercer, 1945; Lipson and Mercer, 1946; Thomson and Speakman, 1946). Makinson (1948)
explained the directionality in the friction by the “ratchet” effect. Here, the ratchet effect is the result of
large angle θ, where instead of true sliding, rupture or deformation of the fine scales of wool fibers occurs
in one sliding direction. We note that the frictional directionality can also exist in materials with particles
having a preferred orientation.
The directionality effect in friction on a macroscale is also observed in some magnetic tapes. In a
macroscale test, a 12.7-mm-wide MP tape was wrapped over an aluminum drum and slid in a recipro-
cating motion with a normal load of 0.5 N and a sliding speed of about 60 mm/s. The coefficient of
friction as a function of sliding distance in either direction is shown in Figure 14.18. We note that the
coefficient of friction on a macroscale for this tape is different in different directions.
WR
M
=π4 γ
l
,