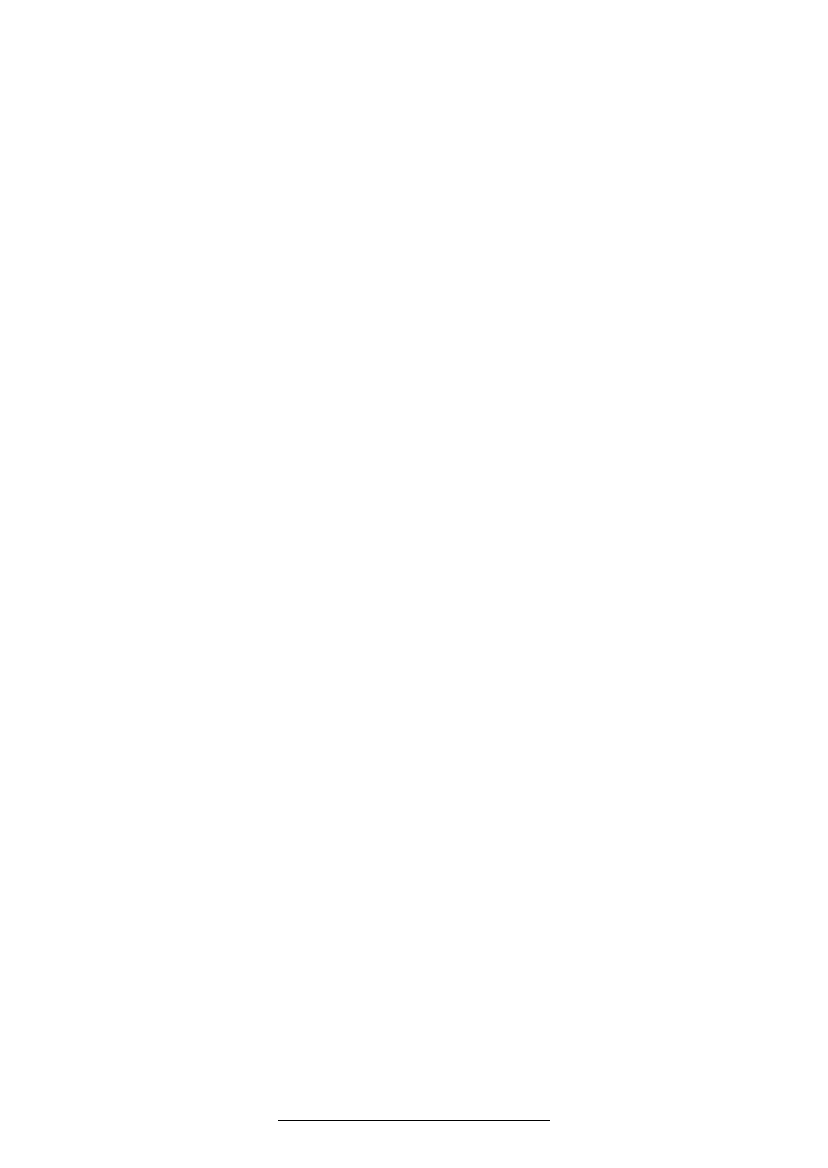
that aimed to replicate Kamakura-era techniques
that had been lost. Nearly all swords made in the
shinto period were intended for hand-to-hand com-
bat, and thus did not reproduce the wide variety of
blades made in past eras. Characterized by brilliant
surface patterns atop a well-tempered steel structure,
these swords were technically refined, yet nearly all
of those produced after the beginning of the Toku-
gawa shogunate were used solely for martial arts
practice or for ornamental purposes. At the same
time, sword fittings, such as sword guards, scabbards,
and other equipment, became more elaborate and
reflected the new role of samurai swords as a status
symbol linked to social rank. Swords also came to be
regarded as status symbols which identified those
who belonged to the warrior classes and upheld the
warrior code, and were prized as part of family her-
itage. After about 1800, swords are identified as shin-
shinto (literally, “new-new swords”) or as fukkoto
(meaning “of the renewal”) depending upon type.
The term fukkoto is reserved for katana-type blades.
Sword Production Japanese-style swords are dif-
ferentiated from other types in their consistent use
of steel in different gradations of hardness attuned
to the requirements of different parts of the blade.
As early as the eighth century, during the Nara
period, these technologically advanced blades were
made of densely forged steel laboriously hammered,
folded, and welded multiple times in order to create
a steel fabric of superior flexibility and integrity. Due
to this process, Japanese-style blades have a com-
plex, multilayered structure similar to the grain of
wood, with a more flexible, lower carbon-content
steel encased in (or layered with) a harder, more
brittle outer surface that is exceptionally durable.
The difference in the carbon content of the steel and
the positioning of the contrasting metals also results
in the characteristic curve of Japanese swords.
The traits detailed above comprise the distin-
guishing characteristics associated with all swords
produced in the traditional Japanese style. In later
times, Japanese swords were forged from precisely
combined blocks of steel that were prefabricated to
facilitate production and then hammered into a final
form that was unsurpassed by blades produced in
other parts of the world in structural integrity,
toughness, and sharpness.
As noted above, even in the formative years of
sword production, Japanese smiths mastered steel
technology. Japanese swords are noted for their con-
trolled carbon content, which produces refined steel
of superior hardness and regularity of structure. In
addition, Japanese sword smiths were also skilled in
shaping blades of superior strength and durability.
Thus, swords made in Japan quickly gained a repu-
tation for precision and technological refinement,
and those involved in sword production attained
social prominence. Beyond the respect accorded to
their profession, smiths also had religious affiliations
that enhanced their high social position. Some early
sword smiths were members of the Shugendo sect, a
religion practiced by mountain-dwelling adherents
who lived in austerity and seclusion. Other sword
manufacturers who worked prior to the Kamakura
era were affiliated with the Tendai school of Bud-
dhism, an eclectic religious tradition originating in
China that was headquartered in Japan on Mt. Hiei,
just above the aristocratic capital, Kyoto. For more
information on Shugendo and Tendai Buddhism, see
chapter 6: Religion.
About 200 schools of sword craft techniques
existed in Japan during approximately 1,200 years of
sword production, and each had particular tradi-
tions, blade marks, and other identifying character-
istics that can be traced with great accuracy today.
From the 10th century, smiths began to chisel signa-
tures on the tang of the blade, thus forging an
enduring bond between the reputation of a skilled
artisan and the sword throughout its functional life.
Inscriptions could also include the province and
town where the blade was produced and even the
date the sword was tempered.
Another form of signature is used by all Japanese
sword smiths. A distinctive temper pattern called
hamon on the cutting edge of the sword can indicate
the specific era and place, as well as the individual
smith or workshop, where the sword was produced.
The hamon is a synergistic result of three events that
contribute to the final hardening of the sword’s cut-
ting surface. First, clay is applied to the blade and
allowed to dry. Then, the sword is repeatedly passed
through a high-temperature charcoal fire for a spec-
ified amount of time, until it reaches the tempera-
ture desired by the smith. Finally, the blade is
plunged into a tank of water, calibrated precisely to
W ARRIORS AND W ARFARE
159