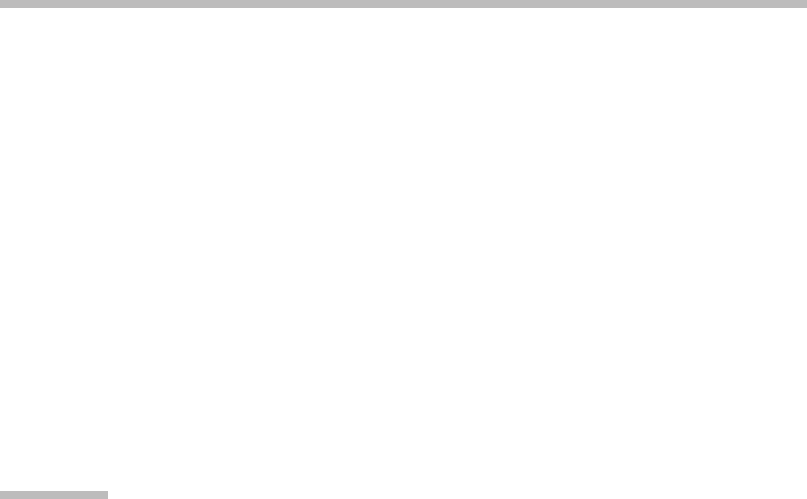
display is a haptics issue. The first goal of the project was developing a haptic
interface for biting. The device should be suitably shaped for placing in the
mouth, and be effectively controlled to simulate food texture. The second goal
was to present a multimodal sensation to the user. To this end, biting sounds
and chemical tastes should be integrated with the haptic interface.
To achieve these goals, we developed a haptic interface to present the biting
force. The Food Simulator generates a force simulating the previously captured
force profiles of an individual biting real food. A film-like force sensor is used to
measure biting force associated with real food. A force sensor is installed in the
Food Simulator and the device is actuated using force control methods.
The Food Simulator is integrated with auditory and chemical sensations asso-
ciated with taste. The sound of biting is captured by a bone vibration microphone.
The sound is then replayed using a bone vibration speaker synchronized with the
biting action. The chemical sensation of taste is produced using an injection
pump, with a tube installed at the end effecter.
9.3
CURRENT IMPLEMENTATIONS
OF THE INTERFACE
The Food Simulator employs mechanical linkages to apply biting force to the
teeth. It is integrated with sound, vibration, and chemical taste.
9.3.1 Haptic Device in a Food Simulator
The haptic device is composed of a one degree-of-freedom (DOF) mechanism
that is designed to fit in the user’s mouth. The device is aimed at applying a force
representing the first bite. Chewing is not addressed in this prototype. Thus, the
device is designed to apply force in a direction normal to the teeth. The configu-
ration of the mechanical linkage takes into consideration the jaw structure. The
shape of the linkage enables the application of force to the back teeth. The width
of the end effecter is 12 mm, and the device applies force to two or three teeth.
Regarding hygiene, the end effecter includes a disposable cover of cloth and
rubber. Figure 9.1 shows the overall view of the apparatus.
The haptic device is composed of a ones DOF mechanism that employs four
linkages. Figure 9.2 illustrates its mechanical configuration. The linkages are
driven by a DC servo motor (MAXON Motor, RE25). The user bites the end effec-
ter of the device. The working angle of the end effecter is 35 degrees, and the max-
imum force applied to the teeth is 135 N. A force sensor that detects force applied
by the user’s teeth is attached to the end effecter. The device is controlled by a PC
(Pentium 4, 2 GHz). The update rate of force control is 1,700 Hz, which is suffi-
cient for controlling a haptic interface.
9.3 Current Implementations of the Interface
293