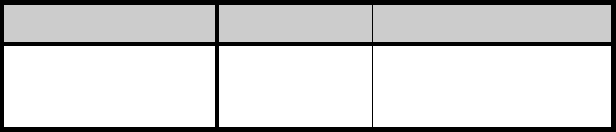
240 Practical Variable Speed Drives and Power Electronics
A.5 Resistance temperature detector (RTD)
Name of Sensor Metal Resistance at 0ºC
Cu-10
Pt-100
Ni-120
Copper
Platinum
Nickel
10 Ω
100 Ω
120 Ω
Figure A.7:
The most common types of RTD sensors
Resistance temperature detectors (RTDs) monitor temperature by measuring the change
of resistance of an accurately calibrated resistive sensor, usually made of copper,
platinum or nickel. Tungsten is sometimes used for high temperature applications. RTD
sensors can be of the wire wound type, which have a high stability over a period of time,
or can be of the metal film types, which are lower cost with faster response but their
characteristics can deteriorate over a period of time.
The type of RTD sensor most commonly used in electrical machines comprises a
Pt-100 sensor
element made of platinum, whose resistance is accurately calibrated to
100 Ω at 0
o
C. The sensor is usually insulated and mounted inside a cylindrical metal tube
of dimensions typically 10 mm diameter and 200 mm length.
Since the RTD sensor is physically larger than other types of measuring sensors, it
cannot easily be mounted in the windings or bearings of small electric motors.
Consequently, RTDs are only used on large machines, where they are installed within the
stator slots during manufacture. A slightly different mechanical form is used for mounting
in bearing housings. Thermistors or thermocouples are still the most commonly used
temperature sensors for electric motors.
An RTD has a linear relationship between resistance and temperature, typically
0.4 Ω/
o
C for a Pt-100 sensor. A very sensitive measuring instrument, usually based on the
Wheatstone bridge, is required to continuously measure the small changes in the
resistance of the RTD. These instruments pass a small excitation current through the
resistive sensor.
Although the excitation current can cause some problems with self-heating, this is
seldom a problem because the currents are small, typically less than 1 mA, and RTDs
have a high rate of heat dissipation along the connecting wires and to the measured
medium.
Considering the small changes of resistance with temperature, the overall accuracy of
the RTD resistance measurement is affected by the series loop resistance of the extension
wire between the measuring instrument and the Pt-100 sensor. This is dependent on the
cross-sectional area of the wires and the distance between the RTD sensor and the
measuring instrument. This has led to the development of 3-wire RTDs, where a third
identical extension wire is connected between the instrument and the sensor. The purpose
of the third wire is to provide the measuring instrument with a means of measuring the
wire loop resistance to the RTD sensor. To improve accuracy, this is subtracted from the
total measured resistance. At the RTD sensor, the third wire is simply connected to one of
the legs of the sensor as shown in Figure A.8.