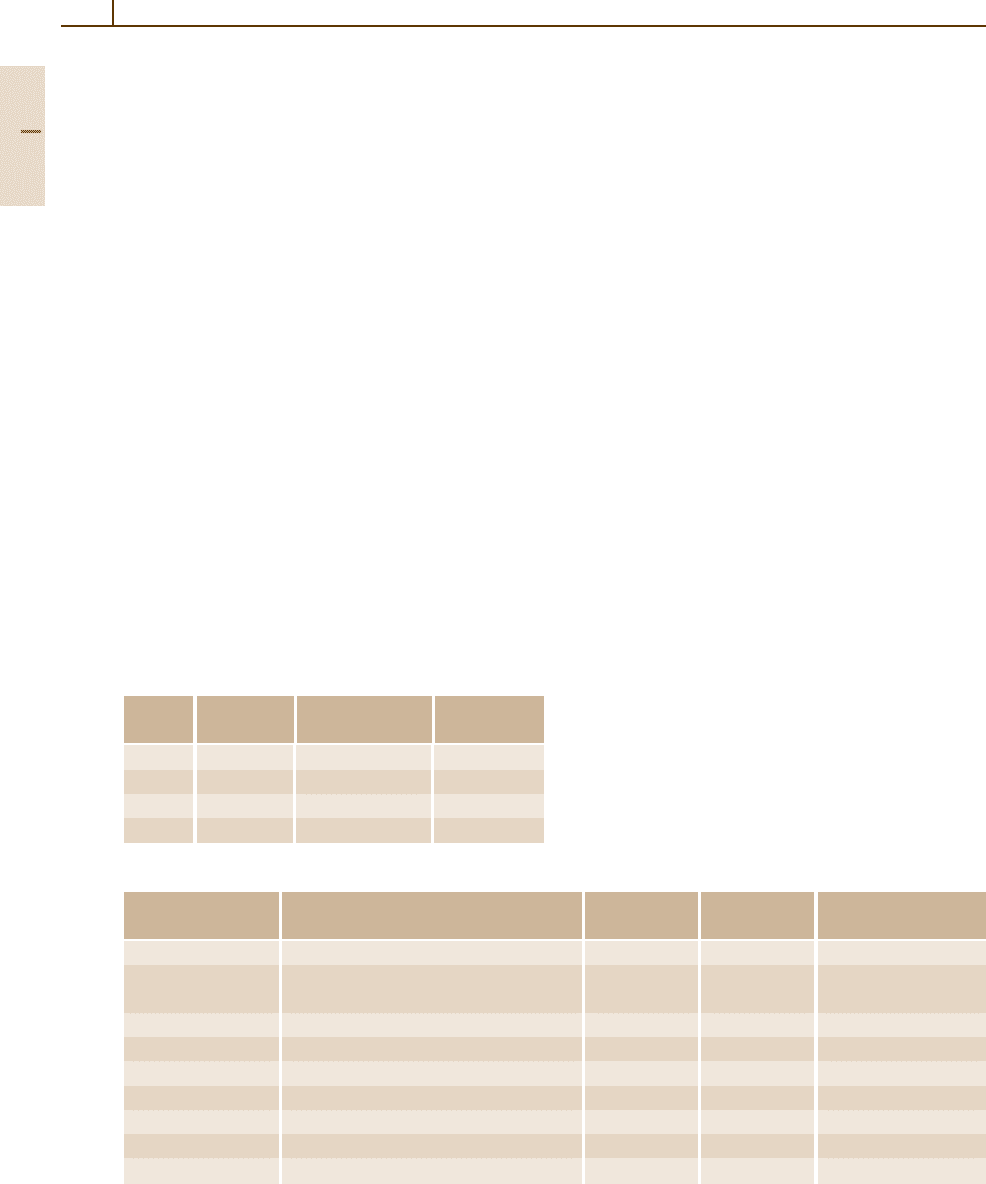
296 Part 3 Classes of Materials
3.1.8 Copper and Copper Alloys
Copper and copper alloys are used as materials mainly
because of the high electrical and thermal conductiv-
ity of Cu and because of the variability and favorable
combination of electrical, mechanical, and corrosion
properties and of color (from copper red to silver white)
by alloying and heat treatment. The basic properties of
Cu are covered in Sect. 2.2.3. The electrical resistivity of
Cu, σ = 16.78 nΩ m (293 K), is the highest among the
metals of moderate cost. The corresponding high ther-
mal conductivity λ =397 W m
−1
K
−1
of Cu gives rise
to numerous applications in heat exchangers. Its high
corrosion resistance and good formability are the ba-
sis of its use as gas and water pipes, in the chemical
and food industries, and – combined with its color – in
architecture.
The alloying of Cu with group IIB to IVB metals
results in a series of alloy systems with a characteristic
sequence of intermetallic phases characterised by their
outer electron to atom ratio (e/a), as first recognised
by and named after Hume-Rothery. This behavior is at-
tributed to the fact that the electronic structure rather
than ionic radius, directed bonds, or other factors of in-
fluence for alloy formation is dominating the and crystal
Table 3.1-100 Characteristics of Hume-Rothery phases in
Cu-, Ag- and Au-based alloy systems
e/a Phase Crystal Example
designation structure
3/2 β bcc CuZn
3/2 ζ hcp CuGa, CuGe
21/13 γ γ brass structure Cu
5
Zn
8
7/4 ε hcp CuZn
3
Table 3.1-101 Groups of copper materials according to ASTM
Designation Maximum alloying range, wt%, Wrought Cast alloys Particular alloying
further alloying elements alloys alloys range for castings
Coppers − + + −
High copper alloys 1.2Cd, 2Be, 3Fe, 2.7Co, 3Ni, 2.5Sn, 1.5Cr, + +
0.7Zn, 0.25Si, 3.4Ti, 1Zr, 3.5Pb
Brasses 43Zn, 3Pb, 2Al, Co, Si, Mn, Fe + +
Bronzes 8Sn, Zn + + 12Sn, 2Pb, 2Ni
Cu
−
Pb
−
Sn − − + 10Sn, 20Pb
Copper–Nickels 30Ni, 1Fe, 1Mn, 2Sn + +
Nickel–Silvers 18Ni, 39Zn, 3Pb, 2Mn + − −
Cu
−
Sn
−
Zn − − + 7Sn, 8Zn, 7Pb
Cu
−
Al 8Al + +
structure formation of theintermetallic phases. The same
is true for Ag- and Au-based alloy systems. A survey is
given in Table 3.1-100.
The solid solution phase α of Cu, dominat-
ing in most Cu materials, is hardened by the
solute elements s through solid solution hardening
which is proportional to the misfit parameter η
s
,
given by the relative difference in atomic radius r
s
to r
Cu
: η
s
= 2
r
s
−r
Cu
/
r
s
+r
Cu
.Sincer
Cu
= 1.28,
r
Ni
= 1.25, r
Zn
= 1.33, and r
Sn
= 1.51, it follows that
the increase in yield stress per at.% of solute increases
in the order Ni < Zn < Sn.
The materials on copper basis may be subdivided
into the groups shown in Table 3.1-101. Standards
for copper and copper materials have been issued by
ASTM, DIN, DKE, CEN, CENELEC, ISO, and IEC.
In the USA, the Unified Numbering System for Met-
als and Alloys (UNS) applied to Cu materials consists
of the letter C and a 5 digit number. More extensive
accounts of Cu and Cu alloys as materials are given
in [1.102–104].
3.1.8.1 Unalloyed Coppers
Cu is used as the technical standard for the conduc-
tivity of metals and alloys. The International Annealed
Copper Standard (IACS) is defined by a Cu wire, 1 m
long and weighing 0.1 kg, the resistance of which is
0.15327 Ω at 20
◦
C. Accordingly, a conductivity of
100% IACS =58.00 MS m
−1
(or m Ω
−1
mm
−2
), which
corresponds to a resistivity of 1.7243793 (µΩ cm). The
electrical conductivity is specifically and strongly de-
pendent on the kind and concentration of impurities
(Fig. 3.1-130).
Part 3 1.8