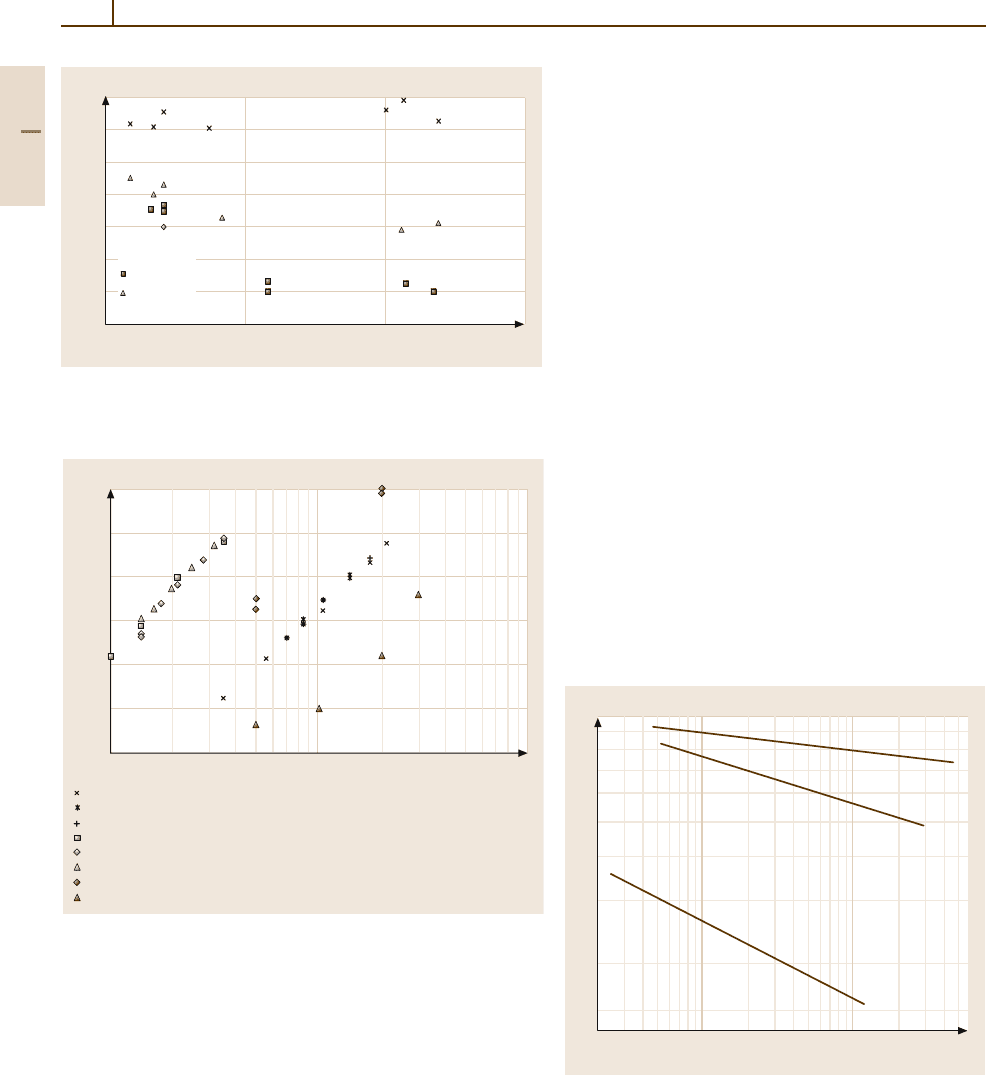
328 Part 3 Classes of Materials
1
10
–1
10
–2
10
–3
10
–4
10
–5
10
–6
10
–7
Grain size (mm)
Steady state creep rate (1/h)
0.01 0.1 1 10
3.5 MPa
7 MPa
14 MPa
35 MPa
Fig. 3.1-185 Steady state creep rate of molybdenum sheets ver-
sus grain size. Sheet thickness = 2mm/6 mm; test temperature =
1450
◦
C; test atmosphere = hydrogen [1.208]
1
10
–1
10
–2
10
–3
10
–4
10
–5
10
–6
Steady-state creep rate of (1/h)
110
100
Test stress (MPa)
T=1600°C; arc-cast Mo sheet, th.=0,5mm
T=1600°C; arc-cast Mo (M9) sheet, th.=0,5mm
T=1600°C; arc-cast Mo rod, dia.=4,1mm
T=2200°C; arc-cast Mo sheet, th.=0,5mm
T=2200°C; arc-cast Mo (M9) sheet, th.=0,5mm
T=2200°C; arc-cast Mo rod, dia.= 4,1mm
T=1800°C; PM-Mo sheet, th.=6mm, grain size=0,1 mm
T=1800°C, MLR sheet,th.=1mm
Fig. 3.1-186 Steady state creep rate at various test temperatures
of vacuum-arc-cast (VAC) Mo sheet (thickness = 0.5mm), VAC
Mo rod (diameter = 4.1 mm), P/M Mo sheet (thickness = 6mm),
and Mo–0.7 wt% La
2
O
3
sheet (thickness = 1mm) versus test
stress [1.107,208]
law creep regime. Nabarro–Herring and/or Coble creep
is suppressed because of the large diffusion dis-
tances in a structure with large, highly elongated
grains. Grain boundaries resist sliding because of the
interlocking structure. A comparison of creep rup-
ture data of pure tungsten and two AKS–W grades
with different grain aspect ratios (GAR) is given in
Fig. 3.1-187.
In the high stress regime (> 60 MPa) and at tempera-
tures between 2500
◦
C and 3000
◦
C, stress exponents
between 8 and 25 were found [1.162,209,210]. This high
stress dependence led to the introduction of a threshold
stress (σ
th
) below which a component does not revealany
measurable creep deformation under usual service con-
ditions. For this threshold stress, which is lower than the
Orowan stress, the detachment of the dislocations from
the second phase particles or bubbles is the controlling
factor [1.211,212].
In the second phase particle/metal matrix interface,
the dislocation line energy is lower compared to the
dislocation line energy in the metal matrix. Of all dis-
persion strengthened materials investigated, potassium
bubbles in AKS–W exert the most attractive interaction
on dislocations [1.213].
For material produced in the 1970s with a mean,
but strongly scattered, grain aspect ratio of around
35, dislocation creep dominated at stresses > 60 MPa
(stress exponent = 25), as can be seen in Fig. 3.1-188.
For material produced 20 years later with a similar grain
aspect ratio of 31, a stress exponent of 1.2 was found
in the stress regime from 30 to 80 MPa, indicating
a diffusion-controlled creep process [1.214]. The eval-
uation of the strain rate/stress dependence of the values
10 100
15
20
30
40
50
60
70
80
90
Stress (MPa)
Time to rupture (min)
AKS-W (GAR = 4)
pure W
AKS-W (GAR > 12)
Fig. 3.1-187 Creep rupture data for AKS–W wires in com-
parison with pure tungsten. Wire diameter = 0.183 mm;
4 < GAR < 12; test temperature = 2527
◦
C; atmosphere
= vacuum better than 7 ×10
−5
Pa; heating rate = approxi-
mately 2000
◦
C/s [1.162]
Part 3 1.9