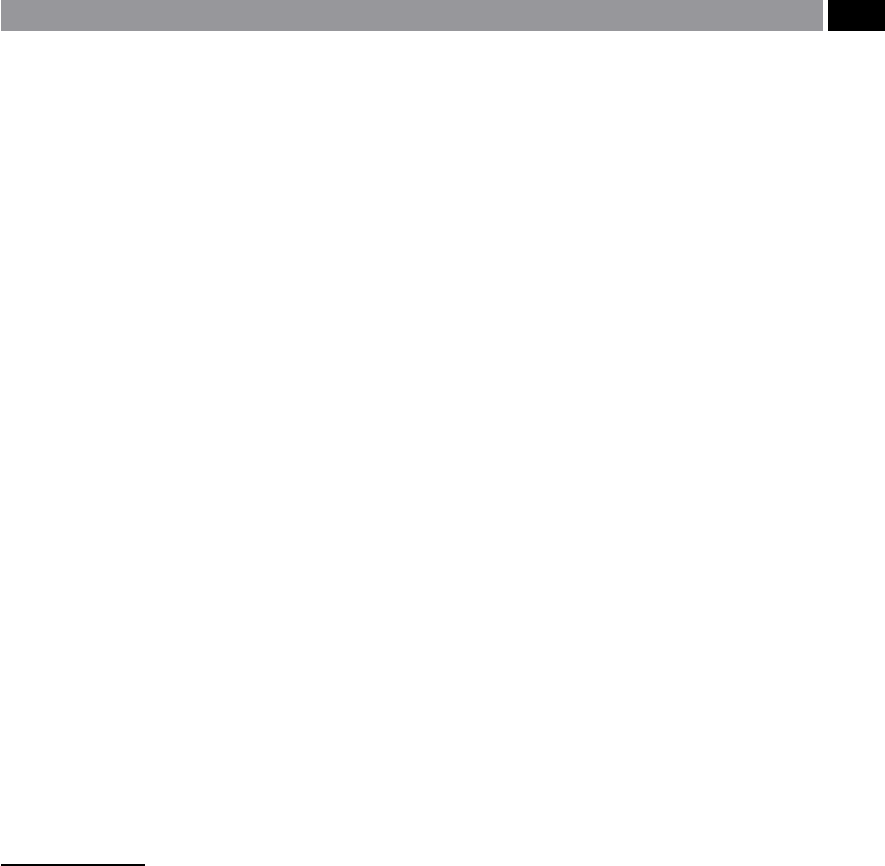
If special-purpose applications are required, such as
when form milling the ubiquitous ‘Vee-and-Flat’ con-
guration for an conventional engine-/centre-lathe
bed, ‘gangs’
42
of: side-and-face, angled- and helical-cut-
ters are deployed to form and generate these slideways.
Here, it is important to ensure that when presetting
the cutters on the tool presetter, that the whole cut-
ter assembly is held in the exact manner that they will
be utilised when ‘gang-milling’. is ‘gang-milling’ set-
up, allows their dimensions and forms to be inspected/
measured, while slowly rotating the whole assembly. If
two ‘
helical cutters’
43
are utilised in a ‘gang-milling’ op-
eration, then their helices should be of the same pitch,
but of dierent ‘hands’ (i.e. le-ward and right-ward
respectively), as this arrangement will balance-out any
end-thrust due to opposite cutter helices.
Setting up ‘Long-edge milling cutters’ – these are
sometimes termed ‘Porcupine cutters’ (i.e. see Fig.
124 – centre), which are normally required for the
heavier and longer cutting applications, is quite a com-
plex presetting process. As the individual cutting in-
serts must be slowly rotated to ensure that axial and ra-
dial run-out values are kept to a minimum. Otherwise
those inserts ‘standing-proud’ of the remainder will
suer from greater wear rates, thereby prematurely re-
ducing the cutter’s eective life quite signicantly while
milling an unwanted step into the machined sidewall.
On standard face mills, ‘face run-out’ can be as high
as >50 µm, so when close tolerances and good milled
surface texture is mandatory, then extreme care must
42 ‘Gang-milling’ , is a complex forming process utilising two,
or more milling cutters adjacent to one another. So, a side-
and-face cutter, located directly together with a helical cutter,
represents a ‘gang’ in its simplest form. is ‘gang’ of cutters, is
normally permanently mounted together for re-grinding and
tool presetting – this is assuming that the cutting edges are
not made-up from a series of strategically-positions indexable
inserts (see Fig. 76).
NB ‘Straddle milling’ , should not be confused with ‘gang-
milling’ , as here, it is normal to use two side-and-face cutters
with spacing collars between them – of a specic and known
dimensional size. erefore, the cutters ‘straddle’ the part –
hence its name – while they machine two faces at the required
distance apart in one pass along the workpiece.
43 ‘Helical cutters’ ,
are sometimes known as ‘Slab-mills’ , hav-
ing either a le-, or right-hand helix, which ensures that the
length of cut and its shearing mechanism are reduced by a
‘quick-helix’ , which is necessary for the milling of more duc-
tile materials.
be taken when presetting such tooling assemblies. In
order to assist the presetting of such tooling on some
face mills, ‘barrel screws’ allow ne adjustment to the
cutting insert (Fig. 140a). Such ‘barrel screw’ designs
are quite simply-designed, but surprising eective in
both adjusting and retaining the cutting inserts, the
following remarks explain how they are designed and
their method of operation. ‘Barrel screws’ (Fig. 140a),
are hardened to resist deformation and have a black-
oxide nish to minimise corrosion. To prevent them
from shiing during a face milling operation, a nylon
pellet is embedded in the thread of the ‘barrel screw’.
Right-hand cutting inserts use le-hand ‘barrel screws’
and vice versa, as this counter-acting rotation keeps the
insert locked rmly in its pocket. e mating surface
of a ‘barrel screw’ is reamed produce a minimum con-
tact of 120° occurs, which ensures accuracy and preci-
sion, while minimising wear. e ‘barrel screw’ hole is
o-set toward the reamed surface, to provide positive
contact with the mating surface throughout the range
of adjustment of this screw. It should be noted, that
these ‘barrel screws’ cannot adjust the eective ‘gauge-
length’ of the tooling, as the amount of adjustment is
limited by the position of the cutting insert’s clamping
screw.
e face-milling cutting inserts shown in Fig. 140a
are tangentially-mounted, oering considerable sup-
port and additional strength to the cutting edge. When
presetting the face mill’s cutting edges when the cut-
t
er body is equipped with ‘barrel screws’ , the following
procedure should be adopted:
•
To adjust the insert outward – leave the cutting in-
sert tight and simply turn the ‘barrel screw’ to move
the insert to the desired setting.
NB A
djustment to the cutting insert’s position,
should only be made in one direction only.
•
To adjust the insert inward – loosen both the cut-
ting insert and ‘barrel screw’ , push the insert in-
ward, then tighten the insert’s screw and adjust out
again to the desired position.
In Fig. 140b, the simple ‘ow-chart’ highlights why it is
important to keep any face milling cutter insert’s run-
out to a minimum. If the run-out o
f both the minor
and peripheral cutting edges is large, then this can
create several undesirable problems for the tooling as-
sembly, including:
•
Poor surface nish – if a cutting insert ‘stands-
proud’ of the others in the face mill, then it will cut
Modular Tooling and Tool Management 259