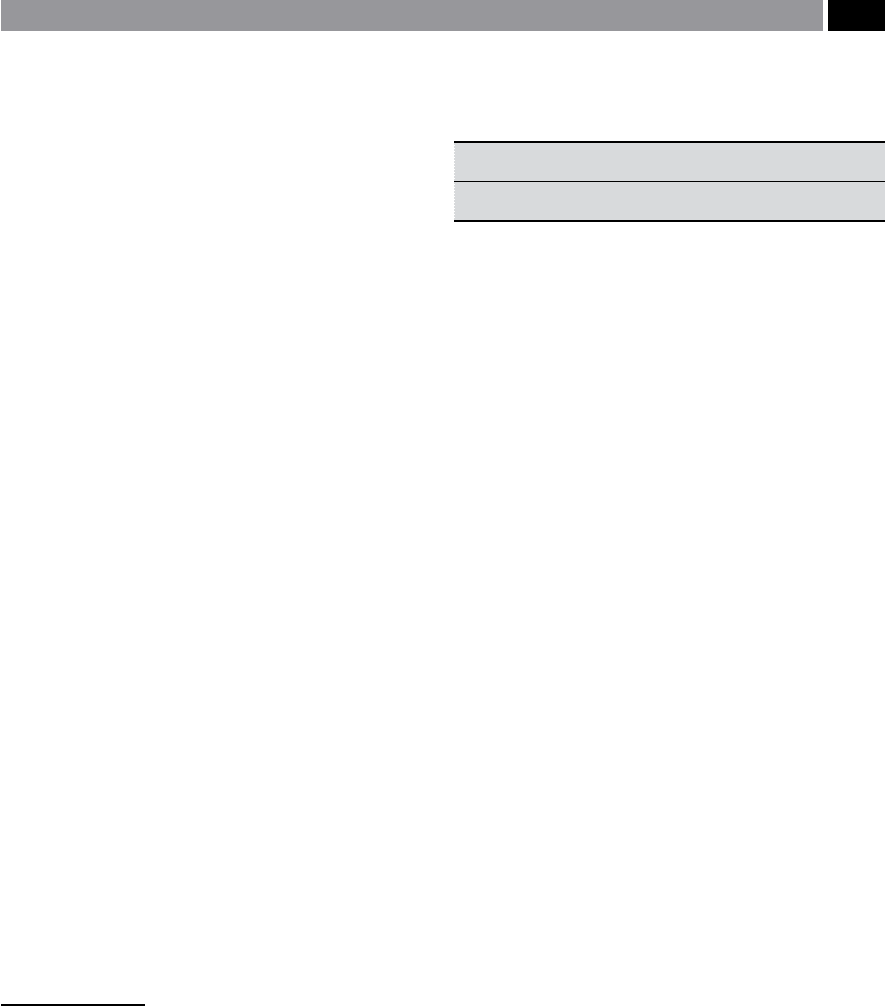
and operations, can be successfully utilised from the
comparisons of cutting uids, through to complex and
dicult-to-machine aerospace machinability trials. If
a more sophisticated technique is required, then it is
also possible to utilise ‘Quality Function Deployment’
16
(QFD), to obtain a complete picture of the outcomes
from machining trials. QFD is oen used by indus-
try as a means for its ‘Continuous-improvement pro-
grammes’
17
. Here for ‘simplicity’s-sake’ , the more basic
and somewhat less complex VA tabulated data-colla-
tion approach, will be briey reviewed.
e application of VA to a series of collated and
compiled massed-data is not new. In fact, it was
widely-used during the 1960’s, but fell into disfavour,
partly because its function and operation were oen
not well-dened – this being exacerbated by poor im-
plementation of its recommendations. However, VA
techniques are useful, allowing one to interpret data
trends both quickly and objectively – without undue
bias – at a glance of a spreadsheet. Not only can signi-
cant trends be readily seen, but the spreadsheet shown
in Fig. 151 – shows a typical machinability data for P/
M compacts drilled by two diering drill-point geom-
etries. By using the spreadsheet, not only can overall
trends be readily seen, it also can depict sub-set trends
as well, giving a complete picture (i.e. globally) of the
important criteria in assessing machining data. As a
simple ranking system is used, considerable objectiv-
ity can be gained and with little undue inuence – bias,
aecting the outcome from these tabulated results. In
employing the ranking of the results, it is normal prac-
tice to decrement down and if two values are ranked
identically, then they are given the same rankings, fol-
lowed by the next lower ranking, being two numbers
lower, as following example shows:
16 ‘Quality Function Deployment’ (QFD), is a general term that
means the: ‘Deployment of quality through deployment of qual-
ity functions’ (Akao, 1988). It is oen known as the ‘House of
Quality’ , because the tabulated graphical representation looks
similar to that of a house – when all the interacting factors
for subsequent analysis have been included on the chart. is
QFD technique, is a wide-ranging philosophy for the com-
plete analysis of both simple and intricate designs and can be
successfully exploited for machinability trials.
17 ‘Continuous-improvement programmes’ ,
can be dened as
an: ‘Operational philosophy that makes the best use of resources
in order to increase product, or service quality and result in
more eective satisfaction of customers’ (Swanson, 1995).
For example, in Fig. 151 – for the values shown in
column two (i.e. le-hand side: Jobber drill, rust
F
orce 0.254 N):
Compact type: 1 2 3 4 5 6 7 8
Ranking: 6 8 5 1 5 7 3 2
NB Here, two 5’s were ranked, meaning that the next
decremented value would rank as 3. Hence, in this case
the Low compaction Compact type No. 2 this was best
and Low compaction No. 4 worst – as jobber drilled.
is ‘truncated approach’ the elementary and easily
comprehended VA tabulation (Fig. 151) , enables non-
specialists, together with knowlegdible experimenter,
to recognize the inuence various machining param-
eters have on the potential performance of the trials
undertaken. By judicious use, the VA technique in
conjunction with a strictly controlled and limited ma-
chining strategy – based upon some form of ‘orthogo-
n
al array’ , in combination with the ‘strength’ (i.e >5%
‘F-ratio’) of parameters by ANOVA, this will enable a
researcher to conduct a speedy, compact, realistic, yet
meaningful machinability assessment.
7.2 Machined Roundness
Roundness is a condition of a ‘surface of revolution’ ,
which can take the form of a: cylinder, cone, or sphere,
where all the peripheral data points (i.e. measure-
ments) intersect. In reality, the radius of say, a nomi-
nally round workpiece tends to deviate – from the
‘true circle’ – around the periphery of the part, making
these variations the theme to subjective interpretation
of the measured results. In fact, in the past, the sim-
plistic technique for the assessment of roundness was
usually measuring three diameters on a workpiece, to
determine the diametrical variations, then ‘averaging’
to give its overall dimensional size. Moreover, for vari-
ations in a workpiece’s radius about an axis of rotation,
this was oen found by positioning the part between a
‘
bench-’ , or sine-centres’ – the latter equipment is em-
ployed for turned tapered features, then rotating and
monitoring it with dial gauges both at and along its
length. In the past, this rather supercial metrologi-
cal workpiece assessment was supposed to inform the
inspector as to its potential in-service performance.
If some radial variations occurred, this geometrical
Machinability and Surface Integrity 285