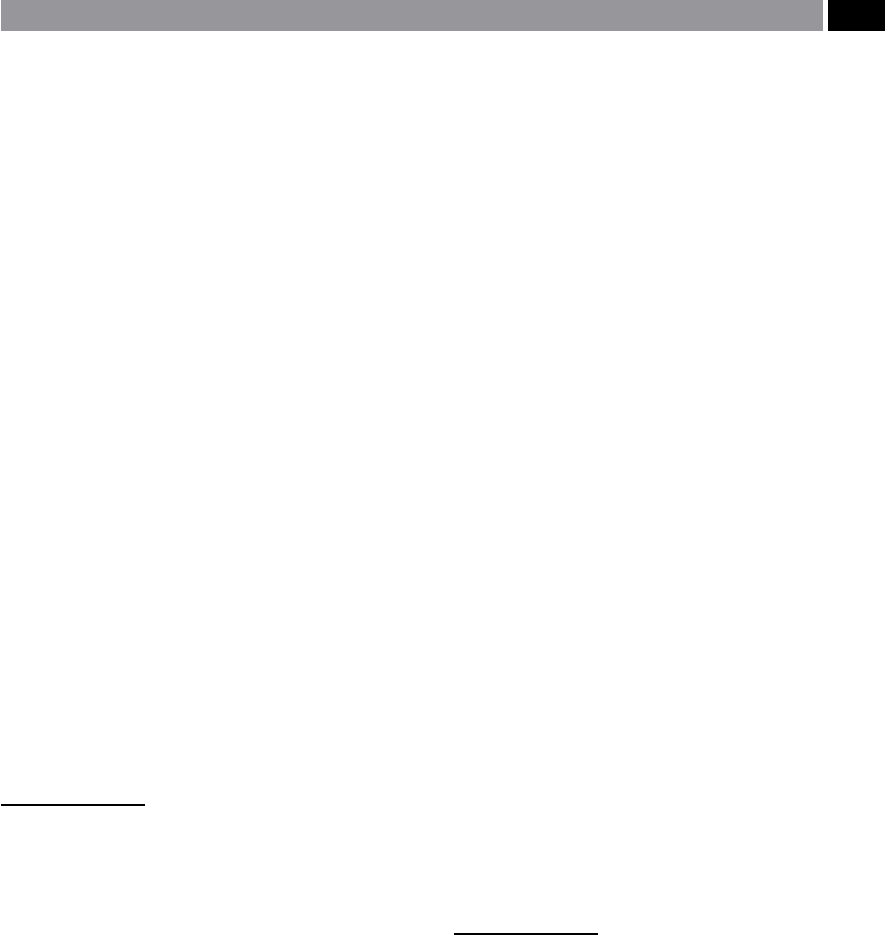
‘full’ production operational machining, meaning that
with some degree of condence, manufacturing dic-
tates and objectives will be met.
In Fig. 146, a commercial (PPT) testpiece has been
developed showing typical machining data employed,
based upon the secondary machining operations de-
manded by many companies on Powder Metallurgy
(P/M) components – where light nishing cuts, or ac-
curate and precise screwthreads are demanded. Here,
the cutting insert can turn three dierent diameters
– usually in some form of arithmetic progression
9
, so
that feedrate longitudinally can be metrologically as-
sessed. Moreover, the insert’s passage over the surface
can be metallographically-inspected and a micro-
hardness ‘footprint’ across a tapered section can be
undertaken, to see if any surface/sub-surface modica-
tions have occurred. More will be said on this subject
later in the chapter, when discussing the eects of ‘ma-
chined surface integrity’. is design of using a thick-
walled tube (Fig. 146), that can be produced from ei-
ther wrought stock, or P/M compact processing – the
latter, giving a controlled ‘density’
10
across and along
the part, makes it particularly ‘ideal’ for any secondary
machining machinability trials. Boring operations can
also be conducted on such a testpiece geometry, al-
lowing roundness parameters and its associated ‘har-
monic prole’ to be metrologically assessed, in conjuc-
tion with any ‘eccentricity’ with respect to the OD and
9 ‘Arithmetic progressions’ , are normally utilised for many ap-
plied machining (PPT) trials as they give a ‘base-line’ for the
research work and increase at a controlled amount. For ex-
ample, a feedrate, could begin and increase as follows: 0.1, 0.4,
0.7, 1.0, 1.3, … mm rev
–1
– with the ‘common dierence’ being
3. As a mathematical expression, this simple arithmetic pro-
gression, can be written as follows:
a, a+d, a+2d, a+3d, a+4d, a+5d, … where the ‘common dier-
ence’ is ‘d’ , giving the:
n´
th
term as: a+(n–1)d.
10
‘P/M Density’ , refers to either the uncompacted, or free-par-
ticulates and is termed its ‘Apparent density’ (AD). is term
AD, is used to refer to the loose material particulates prior to
PM compacting, to describe the density of a powder mass ex-
pressed in grammes per cubic centimetre of a standard volume
of powder. is AD diers from that of its ‘compacted density’
– which will vary depending upon the consolidation (i.e. com-
pacting) technique utilised. For example, double-compaction
– pressing the powder in the dieset from both ends, or us-
ing ‘oating diesets’ – to simulate double compaction, in this
latter case, pressing from one end only, will produce a more
uniform bulk density throughout the ‘green compact’ as it is
known – prior to its subsequent sintering process.
ID – these machined surfaces both being produced in
a ‘one-hit machining’ operation – then inspected by a
suitable roundness testing machine.
e main advantage of using industrial-based
(PPT) testpieces similar to that shown in Fig. 146, is
that ‘canned-cycles’
11
, can be used to produce the un-
dercuts, turning passes, or screwcutting operations
on each part. Moreover, optional ‘programmed-stops’
can be written, allowing the research-worker/operator,
to have the facility to stop machining at a convenient
point as desired, at the press of a button – giving a
measure of control to the automated CNC machining
processes. If a series of testpieces are to be machined, it
is important that all of the parts machining sequences
are known and that they are laid-out in a consequtive
logical fashion. is allows one to measure the dete-
rioration with machining time for the sequence of tes-
tpieces produced. To this end, not only should some
unique and logical part numbering system be used,
but in the case of P/M testpieces, the top and bottom
for each compact should be established. As when each
one was initially compacted, its local density have var-
ied and, for consistency for all machining undertaken
with each test piece, it needs to be held in the same
orientation.
Oen it is possible to amalgamate two previous
ranking machining test regimes into one, this is the
case with ‘Accelerated Wear Test’ (AWT) illustrated
in Fig. 147, this test being a combination of both the:
‘Rapid Facing’ and ‘Degraded Tool’ tests – previously
described. In the case of the AWT technique, this hy-
brid test’s aim is to assess the relative machinability of
either wrought, or secondary machined P/M compacts
11 ‘Canned-cycles’ , this is a preset sequence of events that is ex-
ecuted by issuing a single command, which may remain active
throughout the program, or in this case will not, for a par-
ticular ‘canned-cycle’ *. For example, once the preset values/
dimensions together with the required tool osets have been
established, then a preparatory function entitled a ‘G-code’
can be used, such as a G81 code, which would initiate a sim-
ple drilling cycle, in association with the following G84 code
which would then specify a tapping cycle on this drilled hole,
or alternatively, a G32 code commences a threading cycle and
so on. – which considerably reduces both the complesaty and
overall length of a CNC program.
*G-codes fall into two categories, they are either ‘modal’ , or
‘non-modal’. A ‘modal’ G-code, remains ‘active’ for all subse-
quent programmed blocks, unless replaced by another ‘modal’
G-code. Conversely, a ‘non-modal’ G-code will only aect the
programmed block in which it appears.
Machinability and Surface Integrity 277