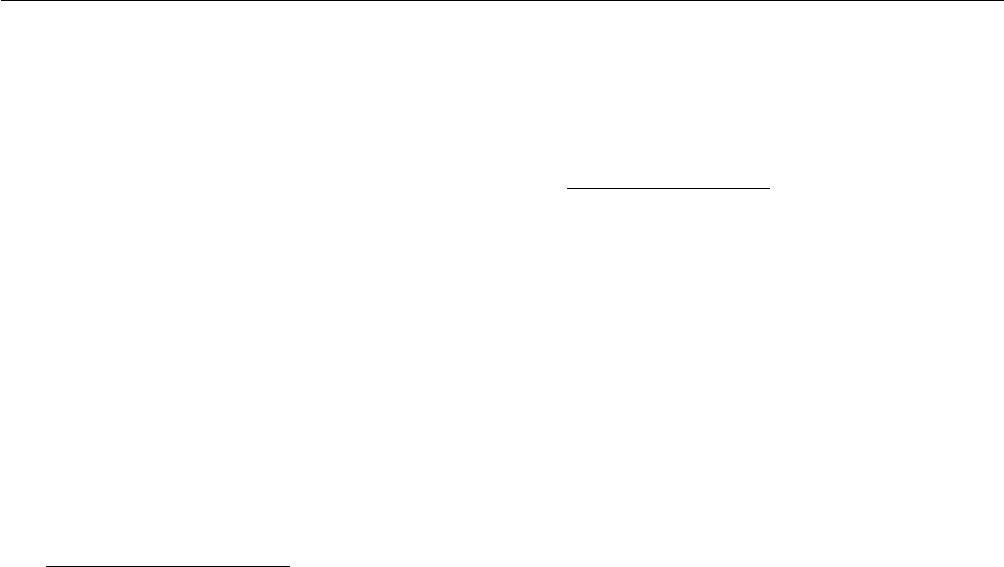
3 SOLAR COLLECTOR TECHNOLOGIES AND SYSTEMS
743
rationally and smartly applied, the quality of annealing can
guarantee to be good.
The hydrogen is a reducing gas, it can reduce metallic
oxide, when its temperature reaches above 700ć, it can
decarburize from the metal. The vapor also has the
intensive ability to decarburize. Therefore, the Kovar is
often degassed and decarburized in the humidified
hydrogen atmosphere. Some papers present when the
Kovar is decarburized at 1100ć, 15-30 minutes, the carbon
content in the Kovar can reduce to 0.01%, and it rarely
produces gas bubbles in the sealing joint. But discovered in
the actual experiment and research that, the annealing
temperature of the Kovar is at the scope of 970ć ~1050ć,
about 30 minutes, it can obtain pure and contains less
impurity material, and can avoids the high temperature
causing the material twice recrystallization and the crystal
grain to non-uniformly grow up.
3.3 The Preoxidation of the Kovar
The purpose of the preoxidation is to form a certain layer of
the metal oxide on the surface of the Kovar body, and the
sealing is to make the glass bond the oxide film. According
to the mechanism of matched glass-to-metal sealing, it is
important and necessary to preoxidize the Kovar alloy for
fine wetting between the glass and Kovar. The extent of
preoxidation directly influences the strength and
hermeticity of the resulting matched seal. When the oxide
depths are too thick or overoxidation, the oxide layer can
saturate the glass, and the oxide layer forms porous path to
permeate gases, especially, the thick oxide layer is easy to
desquamate from the surface of the metal and results in
seals of reduced bond strength. When the oxide depths are
too thin, the glass can not be good wetting with the metal,
the strength and hermeticity of sealing is so bad that
resulting in the failure of sealing. The depth of Kovar
oxidation is often through the use of a humidified H
2
-N
2
atmosphere to precise control.
A paper presents that oxidizing the Kovar to a 2-10μm
intergranular depth can promote strong chemical/
mechanical bonding between the metal and the borosilicate
glass typically used in the production of matched
glass-to-metal seals [7].
In the actual production, the preoxidation temperature
recommends at 800ć, about 10 minutes. Generally it may
be judged the quality of oxide film through the color of
oxide layer, the deep grayness or blue grayness is better for
the glass-to-metal seals.
3.4 The Glass-to-Metal Seals
In the solar receiver, the tubular seals, so-called
“Housekeeper” seals, are those in which the edge of the
metal tube is embedded in glass and the edge of the metal
tube is surrounded by the glass. This metal is formed to a
thin edge so that it is able to yield as it expands with heat
relative to the glass, and the stresses in the glass do not
exceed its tensile strength.
The length and thickness at sealing edge of the metal is
determined to the basis of the specific situation, if the
contact surface is too little to have enough sealing strength.
Recently, owing to the adoption of the latest transistor type
induction heating to replace the traditional vacuum tube
induction heating, the high frequency induction heating
equipment is much safer in performance and smaller in
volume. It’s more convenient in operation comparing the
operation of the glass lathe, therefore, it is selected to seal
the glass to metal in the experiment, which has got very
fine effect of sealing.
The temperature, time, and atmosphere are called three key
factors in the glass-to-metal sealing process, the threes
are complement each other, can't stand alone to treatment.
Generally, the sealing process adopts a H
2
-N
2
atmosphere
or a N
2
atmosphere. The temperature is the most important
factor in the three factors, when the temperature is too high,
the glass will flow like a fluid and is prone to produce
glass bead, even bubble formation in the glass because the
glass and metal release gases from them bodies. When the
temperature is too low, the viscosity of glass is so great that
the liquidity of the glass is not good, causing some leaks,
unsmooth in the surface of the glass and to be not “wet. Its
sealing strength is also not good. Through the experiment
study, the temperature of sealing is recommended in the
scope of 950ć-1020ć, and the color after sealing should
be gray, if the color is silver white, the oxide is not enough,
but if the color is black, the metal might be over oxidized
or the sealing time is too long.