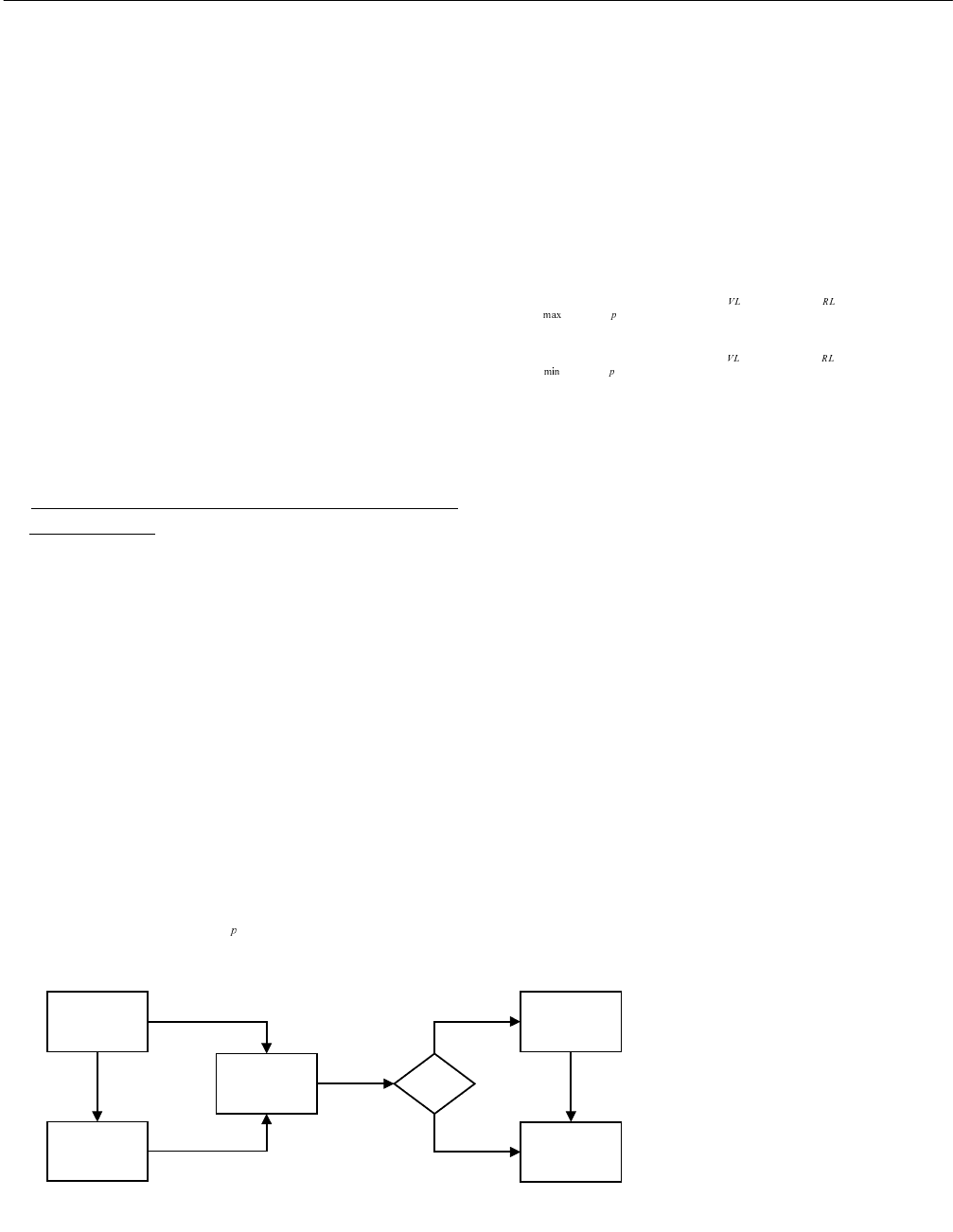
3 SOLAR COLLECTOR TECHNOLOGIES AND SYSTEMS
761
Advantages of the method are that only very few sensors
are required additionally to those which are anyway
necessary to control the system and that failures can easily
be reported due to the connection of the monitoring PC to
internet and email. A disadvantage is that reduced yields of
the system cannot be quantified so far. Thus, it is difficult
to decide whether measures to improve the function of the
system are worthwhile. Also, identification algorithm could
not be identified for all conceivable system failures.
Furthermore, most of the large solar heating systems are
individually planned. Even after very careful adaptations of
the algorithms to the respective solar heating system, some
probability remains that a failure with considerably reduced
solar yields remains undetected. To avoid this, a further
control procedure is recommended which is based on
dynamic system simulations.
3. SYSTEM MONITORING BASED ON DYNAMIC
SIMULATIONS
The aim of the proposed procedure using system
simulations is to determine numerically the designed solar
gain in order to compare these values automatically with
the actual gain derived from measured values. This
comparison indicates whether the system is operating in the
respective period without important solar gain reductions,
cf. fig. 4. For the comparison, enthalpy values for charging
and discharging of the storage tanks are selected.
Actual system gain: The actual system gain can be
determined using the enthalpy flow through the heat
exchanger using the following equation:
QcVTρ=⋅ ⋅⋅Δ
As measured values, the flow rate as well as inlet and outlet
temperatures on one side of the heat exchanger (either
primary or secondary) are required. To consider sensor
uncertainties, maximum errors D and DT can be
estimated and considered. With an integration of the
measured values over time an estimation of maximum Q
max
and minimum Q
min
gains can be made. Q
max
and Q
min
are
forming a confidential range, in which the real values
considering the sensor uncertainties can be expected.
()
()()
Q c VV T TT T tρ
⎡⎤
=⋅⋅ +Δ ⋅ +Δ − −Δ ⋅Δ
⎣⎦
()
()()
QcVVTTTTtρ
⎡⎤
=⋅⋅ −Δ ⋅ −Δ − +Δ ⋅Δ
⎣⎦
System design yield: In order to determine the design yield
of a solar heating system for a desired period (e.g. one day),
the installed solar heating system including the complete
control strategy has been implemented in a powerful
simulation tool (TRNSYS). To reduce the effort of
implementing new solar heating systems in the simulation
environment, only standardized system designs have been
investigated so far. The simulations are carried out with
measured irradiation, ambient temperature, cold water inlet
temperature and flow rate as boundary conditions. The
simulations supply the cumulated enthalpy transfer through
the heat exchangers.
For a validated system implementation, the determined
solar gain can be considered as the design yield of a well
functioning solar heating system. However, even for the
determination of the modelled solar gain, uncertainties of
the measurement of the boundary conditions as well as
uncertainties of the numerical models need to be considered.
For instance, the reliability of the simulation result depends
on simplifications in the reproduction of the system,
uncertainties of parameters, and the
time step of the simulation and the
input data. In (Wiese 06),
comprehensive investigations have
been carried out to determine the
influence of various factors. Very
influential are the simulation input
data in the order irradiance, ambient
temperature, water demand profile
and cold water inlet temperature as
monitoring of
system and
climate
simulation of
system behaviour
boundary
conditions
comparison daily
energy gain
evaluation
storage
alerting if
necessery
calculated gain
measured gain
Fig. 4: Rough scheme of the simulation based system monitoring.