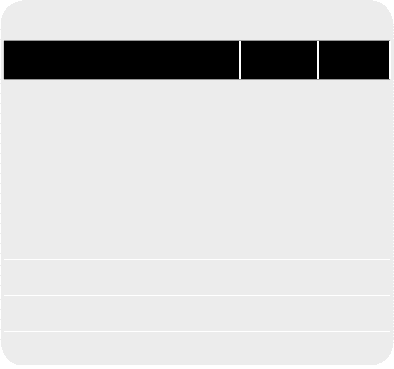
reductions of around 50 per cent without significantly increasing fuel con-
sumption and is offered as an option for UEC–LSE engines (see Chapter 3 and
more in the Emissions Reduction section in this chapter).
uEC-H TyPE EnginE
Although superseded by the LA, LS and LSII designs, and no longer in pro-
duction, the UEC-H type engine remains in service and warrants more detailed
description. The UEC-H type engine (Figure 11.16) is of cast iron construc-
tion with the three separate blocks of bedplate, entablature and cylinder block
secured to one another by long tiebolts. Unlike other designers of two-stroke
engines, Mitsubishi retained the solid cast iron construction (Figure 11.17)
to achieve greater rigidity with less deformation in service and lower vibra-
tion and noise levels. The shell type main bearings are supported in housings
machined in the bedplate. The running gear is of straightforward conventional
design using shell type or white metal–lined large end bearings and a crosshead
of traditional table type (Figure 11.18) with four guide slippers and twin white
metal–lined top end bearings and the piston rod bolted direct to the crosshead
pin. The connecting rod itself is machined from forged steel.
Compared with the two-stage turbocharged E type engine, the constant
pressure turbocharged UEC-H engine has a delayed exhaust valve opening and
consequently more effective work done during each power stroke.
Exhausting and Scavenging
Referring to the cross-sectional drawing (Figure 11.16), the exhaust gases leave
the engine by way of a diffuser type pipe to enter the exhaust gas manifold.
The Super MET non-water-cooled turbocharger, or two chargers in the case of
a large number of cylinders, is located above this manifold on a pedestal. The
uEC-H type engine 373
Table 11.3 Mitsubishi uEC programme
LSii LSE
Bore (mm) 330
370
430
500
600
750
850
450
500
520
600
680
–
–
Stroke–bore ratio 2.8–3.9 4.1–4
Mean eective pressure (bar) 17–18 19–20
Mean piston speed (m/s) 8 8/8.5