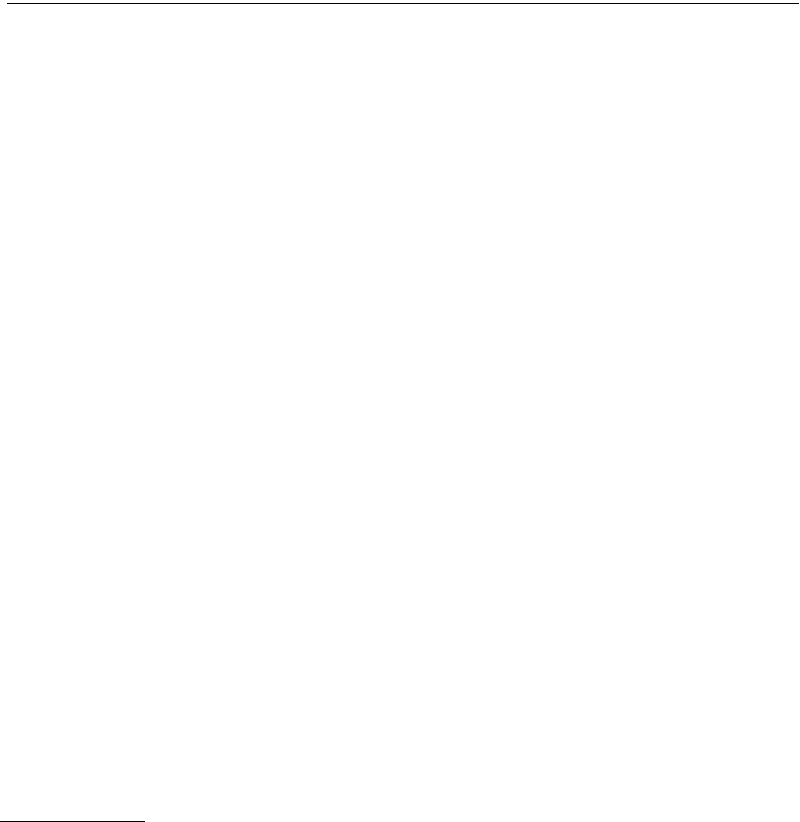
© 1999 by CRC Press LLC
can be acquired and displayed on the display monitor. Hardness value can be obtained from the load–dis-
placement data, as well as from direct measurement of the projected residual area of the indent after
imaging. Young’s modulus of elasticity is obtained from the slope of the unloading curve.
A three-sided Berkovich indenter with tip radius of about 100 nm is generally used for the measure-
ments, see Chapter 10 on Nanomechanical Properties in this book. Sharper diamond tips with included
angle of 60 to 90° and tip radii of 30 to 60 nm are sometimes employed for shallower indentation (on
the order of 1 nm). To obtain an accurate relation between the indentation depth and the projected
contact area, tip shape calibration needs to be done. Also for surfaces with rms roughness on the order
of indentation depth, the original (unindented) profile is subtracted from the indented profile (Bhushan
et al., 1994a,d).
In a typical indentation experiment, the tip is lowered close to the sample (ideally <100 µm). Scan
size and scan rate are selected. The tip is engaged to the sample surface by a stepper motor with a set
point of 1 nA (about 1 µN). A desired image area is captured prior to indentation. The feedback is set
to zero to disable the scanner; the scan size is set to zero so that the indenter will be positioned at the
center of the image. An appropriate set point for the preload condition is selected. The indentation rate
can be varied by changing the load/unload period.
7.3 Microscratching/Microwear Studies
By using a standard or sharp diamond tip mounted on a stiff cantilever beam, AFMs can be used to
investigate how surface materials can be moved or removed on micro- to nanoscales, for example, in
scratching and wear (where these things are undesirable) and nanofabrication/nanomachining (where
they are desirable) (Hamada and Kaneko, 1992; Miyamoto et al., 1991; Bhushan and Koinkar, 1994b,
1995a–c,e, 1997; Bhushan et al., 1994 a,c; 1995d; Bhushan, 1995a,b, 1997, 1998a,b; Koinkar and Bhushan,
1997a,b). A variety of polymers and ceramics and hard coatings have been studied. Many examples of
scratching/wear of magnetic recording materials have been presented in Chapter 14 on magnetic storage
devices in this book. This chapter focuses on the studies with silicon material.
Figure 7.2a shows microscratches made on Si(111) at various loads (Bhushan and Koinkar, 1994b).
As expected, the scratch depth increases linearly with load. Such microscratching measurements can be
used to study failure mechanisms on the microscale and to evaluate the mechanical integrity (scratch
resistance) of ultrathin films at low loads. To study the effect of scanning velocity, unidirectional scratches,
5 µm in length, were generated at scanning velocities ranging from 1 to 100 µm/s at normal loads ranging
from 40 to 140 µN. There is no effect of scanning velocity obtained at a given normal load. For repre-
sentative scratches profiles at 80 µN, see Figure 7.2b (Koinkar, 1997). Insensitivity to scanning velocity
may be because of a small effect of frictional heating with the change in scanning velocity used here.
Furthermore, for a small change in interface temperature, there is a large underlying volume to dissipate
the heat generated during scratching (Bhushan, 1998a).
By scanning the sample in two dimensions with the AFM, wear scars are generated on the surface.
Figure 7.3 shows the effect of normal load on the wear rate. We note that wear rate is very small below
20 µN of normal load. A normal load of 20 µN corresponds to contact stresses comparable to the hardness
of the silicon. Primarily, elastic deformation at loads below 20 µN is responsible for low wear (Bhushan
et al., 1995d; Bhushan and Kulkarni, 1995f; Koinkar and Bhushan, 1997b).
Typical wear mark generated at a normal load of 40 µN for one scan cycle and imaged using AFM at
300 nN load is shown in Figure 7.4a (Koinkar and Bhushan, 1997b). The inverted map of a wear mark
shown in Figure 7.4b indicates the uniform material removal at the bottom of the wear mark. Next we
examine the mechanism of material removal on microscale at low loads, in AFM wear experiments.
Figure 7.5 shows a secondary electron image of a wear mark and associated wear particles. The specimen
used for the SEM was not scanned after initial wear, to retain wear debris in the wear region. Wear debris
is clearly observed. An AFM image of the wear mark shows small debris at the edges, swiped during AFM
scanning. Thus, the debris is “loose” (not sticky) and can be removed during the AFM scanning. SEM
micrographs show both cutting-type and ribbonlike debris. TEM studies were performed to understand