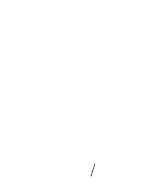
© 1999 by CRC Press LLC
macroscopic model of friction by Bowden and Tabor (1964). If this shear strength is assumed constant,
then the friction is only determined by the contact area. Another simple relation is
where p is the pressure on the contact, which can be shown to follow from a thermally activated model
of the Erying type (Eyring, 1935; Briscoe and Evans, 1982). With this dependence, Equation 6.13 can be
written as
(6.14)
The first term is proportional to the contact area, while the second is proportional to the normal force,
as in the case of macroscopic friction. Note that this conceptually simple linear dependence on normal
force is due to a nontrivial dependence of the friction on the area and on the shear strength.
In their experiments Schwarz et al. (1996) investigated the friction of C
60
on a GeS substrate as a
function of load. Interestingly, they found a different behavior on these two materials. While the friction
vs. load curve on the C
60
followed excellently an F
2/3
dependence, the friction vs. load curve on the GeS
substrate was approximately linear. For a good fit to the experimental data on the GeS substrate, however,
the friction had to be described by both factors of Equation 6.14, which implies a complex relation.
In a similar experiment, Carpick et al. (1996a,b) found that the friction vs. load curve of a Pt tip on
mica was described almost perfectly assuming a constant shear strength and a load–area relation as
predicted by the JKR theory (see Section 6.4.2, Equation 6.20) of elastic contacts. To avoid possible
contamination, the experiments were performed in UHV, including the cleaving of the mica to expose
a fresh surface. To ensure a well-defined tip shape, the tip was imaged using a faceted SrTiO
3
(305)
surface, as proposed by Sheiko et al. (1993), and found to be paraboloidal to a very good approximation.
To acquire one friction vs. load curve, images were taken by varying the load for every line, as discussed
above. Typical friction vs. load curves are shown in Figure 6.27. The nonlinear behavior is evident. The
experimental data points have been fitted to a contact area vs. load curve as predicted by the JKR theory.
Since the agreement between the fit and the data is very good, the shear strength of the contact can be
assumed to be constant, so that the dependence on friction is determined only by the contact area.
Another result of these experiments was that adhesion and friction decreased by more than an order
of magnitude during the experiments, that is, as more and more curves were acquired (Carpick et al.,
1996b). The authors checked that this decrease was not due to wear of the tip, which in any case would
increase the radius of curvature and thus also adhesion as well as friction. Every friction vs. load curve
could be fitted by a JKR curve as described above (see Figure 6.28). From this, the authors deduce that
the decrease in friction is due to changes in the chemistry of the interface, which appears in the JKR
equation through the surface energy (see Equation 6.20). Since the experiments were performed in UHV,
not many mechanisms can explain this behavior. The authors propose either progressive graphitization
of hydrocarbon residues on the tip, or adsorption of K from the mica on the tip as possible explanations.
Nevertheless, it is quite surprising that even under UHV conditions, where contaminant layers are absent,
the friction of the tip–sample junction can be affected in such a dramatic way.
To investigate the effect of tip shape on the friction vs. load curve, Carpick et al. deliberately blunted
the tip and showed that unlike in the previous experiment the corresponding friction vs. load curve did
not follow the JKR area–load relation for a spherical tip in contact with a flat sample (Carpick et al.,
1996a). As shown in Figure 6.27, an appropriate extension of the JKR theory for a tip with a general
shape y(r) = c · r
n
, however, could be fitted almost perfectly to the experimental data. The best fit
corresponded to the exponent n which was deduced from the measured tip shape by imaging a faceted
SrTiO
3
(305) surface. Therefore, although tip shape determines the friction vs. load curve in a nontrivial
way, if the tip shape is known its contribution can be taken into account.
Sp S p
()
=+⋅
0
α ,
FaFbF
nnfric
=⋅ +⋅
23
.