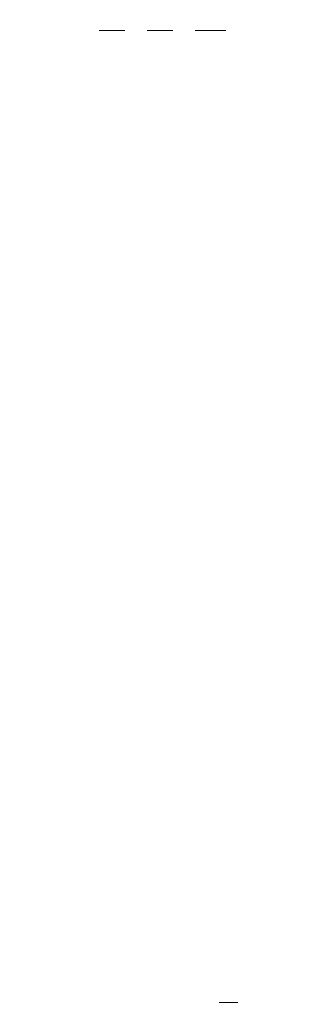
© 1999 by CRC Press LLC
to account for the elastic energy stored in the tip–sample contact by introducing the corresponding
potential (Colchero et al., 1996b). Within this generalized model, the total elastic energy stored in the
SFM setup can be approximated by assuming that this energy is stored in an effective spring with an
effective force constant c
eff
defined by
where c
con
= 2E
*
·r
c
is the stiffness of the tip–sample contact (see Equation 6.17).
To illustrate the formal description of the SFM setup presented above and to analyze the dissipation
of energy, a typical force vs. distance curve will be discussed in physical terms (see also Tabor, 1992).
First, the tip is far from the sample, feels no surface potential, and is not deflected. As the (base of the)
cantilever approaches the sample, surface forces begin to act. Due to the attractive surface potential, the
tip approaches the surface more than the increase of the separation: δz = δ∆ + δd, where δz is the increase
in tip–sample distance, δd the increase in deflection, and δ∆ the increase in separation. Eventually, the
spring is not “strong” enough to hold the tip and the tip jumps onto the surface. During this process,
the tip is first accelerated, then hits the surface, and is suddenly stopped. This will induce vibrations of
the cantilever, but also a sudden elastic deformation of the microscopic tip–sample contact, which in
turn will result in elastic waves propagating out of the tip–sample contact. After some time, the kinetic
energy gained by the tip during the snapping process will be effectively removed from the tip–sample
system either into the macroscopic cantilever or into the two solids tip and sample. A similar process
happens when the tip is separated from the sample. Due to adhesion, the tip sticks to the sample. Elastic
energy is built up in the deformation of the cantilever, but also in the microscopic deformation of the
tip–sample contact. When this contact breaks, the cantilever will vibrate and the elastic deformation of
the tip–sample contact will relax. Again, the elastic energy stored in the system will be converted into
kinetic energy of the cantilever, or into waves in the tip and the sample, and will in the end be dissipated
due to some kind of friction (for example, internal friction in the solids or air damping in the case of
the cantilever).
6.4.3.3 SFFM and Lateral Forces
In the preceding section a general model for an SFM setup was described. However, this model was
applied only to study the behavior of the tip–sample system as the tip approaches the sample. In the
present section, the model will be applied to study the behavior of the tip–sample contact as the separation
between the support and the sample is varied in a direction parallel to the surface (Zhong and Tománek,
1990; Tománek et al., 1991). This is the situation that corresponds to the usual scanning motion of the
tip. Essentially, the description is as before: the tip is attached to a rigid support by means of a spring
and the sample is moved relative to this support by varying the separation ∆
x
. Again, the tip position is
not controlled directly, but follows from the equilibrium condition. The only difference compared to the
description above is that in order to describe the atomic corrugation of the surface, a surface potential
with the periodicity of the sample is assumed. Ideally, this is the potential that a perfect tip with only
one atom at its apex would “see,” and can be computed from first principles. However, also if a nonideal
tip is in contact with the sample on an area with radius r
c
the effective interaction between tip and sample
will show a modulation with lattice spacing (see Section 6.4.1). The total potential seen by the tip is
therefore (Tománek et al., 1991).
(6.27)
where E
0
is the amplitude of the surface potential, k the reciprocal lattice vector of the surface, and c
x
the
force constant of the system. The stability condition for this potential is c
x
> E
0
· k
2
; therefore, if the
amplitude of the surface potential is sufficiently large, the range of postions with |x| < cos
–1
(c/E
0
· k
2
)/k
111
ccc
eff tip con
=+ ,
Vx E kx
c
x
x
x
xtot
, cos ,∆∆
()
=
()
+⋅−
()
0
2
2