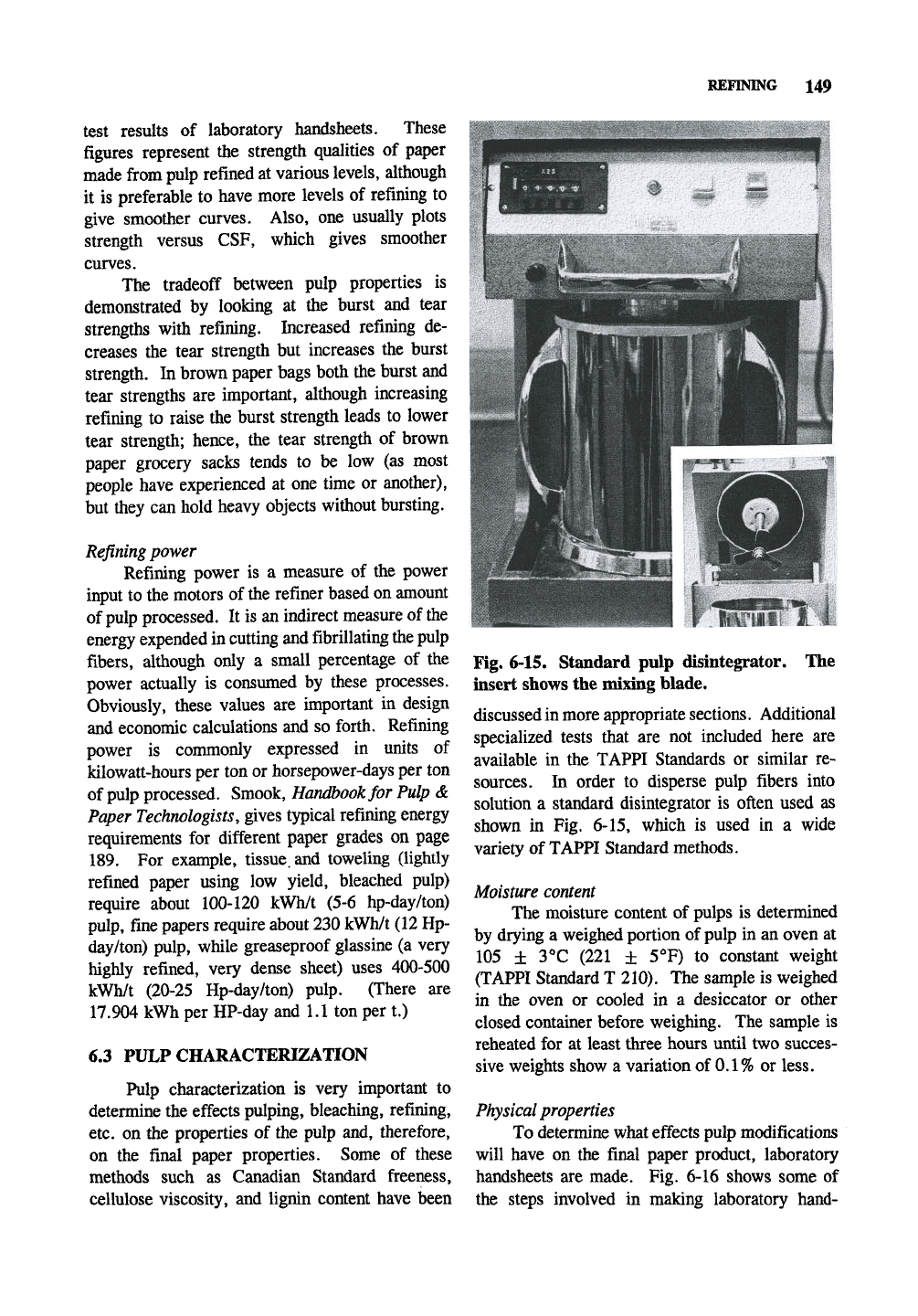
REFINING 149
test results of laboratory handsheets. These
figures represent the strength qualities of paper
made from pulp refined at various levels, although
it is preferable to have more levels of refining to
give smoother curves. Also, one usually plots
strength versus CSF, which gives smoother
curves.
The tradeoff between pulp properties is
demonstrated by looking at the burst and tear
strengths with refining. Increased refining de-
creases the tear strength but increases the burst
strength. In brown paper bags both the burst and
tear strengths are important, although increasing
refining to raise the burst strength leads to lower
tear strength; hence, the tear strength of brown
paper grocery sacks tends to be low (as most
people have experienced at one time or another),
but they can hold heavy objects without bursting.
Refining
power
Refining power is a measure of the power
input to the motors of the refiner based on amount
of
pulp
processed. It is an indirect measure of the
energy expended in cutting and fibrillating the pulp
fibers, although only a small percentage of the
power actually is consumed by these processes.
Obviously, these values are important in design
and economic calculations and so forth. Refining
power is commonly expressed in units of
kilowatt-hours per ton or horsepower-days per ton
of pulp processed. Smook, Handbook for Pulp &
Paper
Technologists,
gives typical refining energy
requirements for different paper grades on page
189.
For example, tissue, and toweling (lightly
refined paper using low yield, bleached pulp)
require about 100-120 kWh/t (5-6 hp-day/ton)
pulp,
fine papers require about 230 kWh/t (12 Hp-
day/ton) pulp, while greaseproof glassine (a very
highly refined, very dense sheet) uses 400-500
kWh/t (20-25 Hp-day/ton) pulp. (There are
17.904 kWh per HP-day and 1.1 ton per t.)
6.3 PULP CHARACTERIZATION
Pulp characterization is very important to
determine the effects pulping, bleaching, refining,
etc.
on the properties of the pulp and, therefore,
on the final paper properties. Some of these
methods such as Canadian Standard freeness,
cellulose viscosity, and lignin content have been
Fig, 6-15. Standard pulp disintegrator. The
insert shows the mixing blade.
discussed in more appropriate sections. Additional
specialized tests that are not included here are
available in the TAPPI Standards or similar re-
sources. In order to disperse pulp fibers into
solution a standard disintegrator is often used as
shown in Fig. 6-15, which is used in a wide
variety of TAPPI Standard methods.
Moisture content
The moisture content of pulps is determined
by drying a weighed portion of pulp in an oven at
105 ± 3°C (221 ± 5T) to constant weight
(TAPPI Standard T 210). The sample is weighed
in the oven or cooled in a desiccator or other
closed container before weighing. The sample is
reheated for at least three hours until two succes-
sive weights show a variation of 0.1
%
or less.
Physical properties
To determine what effects pulp modifications
will have on the final paper product, laboratory
handsheets are made. Fig. 6-16 shows some of
the steps involved in making laboratory hand-