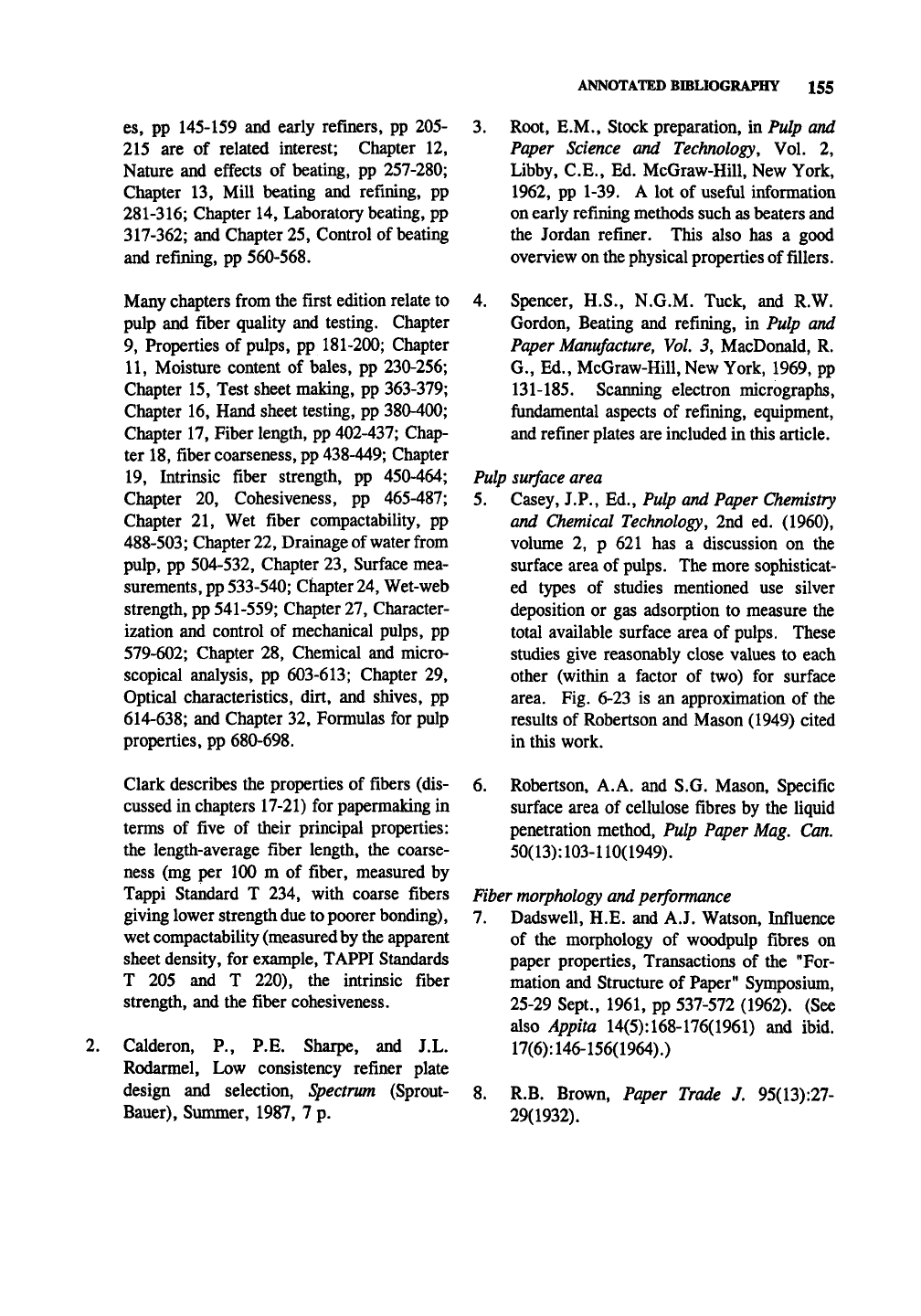
ANNOTATED BIBLIOGRAPHY 155
es,
pp 145-159 and early refiners, pp 205-
215 are of related interest; Chapter 12,
Nature and effects of beating, pp 257-280;
Chapter 13, Mill beating and refining, pp
281-316; Chapter 14, Laboratory beating, pp
317-362;
and Chapter 25, Control of beating
and refining, pp 560-568.
Many chapters from the first edition relate to
pulp and fiber quality and testing. Chapter
9, Properties of pulps, pp 181-200; Chapter
11,
Moisture content of bales, pp 230-256;
Chapter 15, Test sheet making, pp 363-379;
Chapter 16, Hand sheet testing, pp 380-400;
Chapter 17, Fiber length, pp 402-437; Chap-
ter 18,
fiber
coarseness,
pp
438-449; Chapter
19,
Intrinsic fiber strength, pp 450-464;
Chapter 20, Cohesiveness, pp 465-487;
Chapter 21, Wet fiber compactability, pp
488-503;
Chapter
22,
Drainage of
water
from
pulp,
pp 504-532, Chapter 23, Surface mea-
surements,
pp
533-540;
Chapter
24,
Wet-web
strength, pp 541-559; Chapter 27, Character-
ization and control of mechanical pulps, pp
579-602;
Chapter 28, Chemical and micro-
scopical analysis, pp 603-613; Chapter 29,
Optical characteristics, dirt, and shives, pp
614-638; and Chapter 32, Formulas for pulp
properties, pp 680-698.
Clark describes the properties of fibers (dis-
cussed in chapters 17-21) for papermaking in
terms of five of their principal properties:
the length-average fiber length, the coarse-
ness (mg per 100 m of fiber, measured by
Tappi Standard T 234, with coarse fibers
giving lower strength
due to
poorer bonding),
wet compactability (measured by the apparent
sheet density, for example, TAPPI Standards
T 205 and T 220), the intrinsic fiber
strength, and the fiber cohesiveness.
Calderon, P., P.E. Sharpe, and J.L.
Rodarmel, Low consistency refiner plate
design and selection. Spectrum (Sprout-
Bauer), Summer, 1987, 7 p.
3.
Root, E.M., Stock preparation, in Pulp and
Paper Science and Technology, Vol. 2,
Libby, C.E., Ed. McGraw-Hill, New York,
1962,
pp 1-39. A lot of useful information
on early refining methods such as beaters and
the Jordan refiner. This also has a good
overview
on the
physical properties of fillers.
4.
Spencer, H.S., N.G.M. Tuck, and R.W.
Gordon, Beating and refining, in Pulp and
Paper
Manufacture,
Vol 5, MacDonald, R.
G., Ed., McGraw-Hill, New York, 1969, pp
131-185. Scanning electron micrographs,
fundamental aspects of refining, equipment,
and refiner plates are included in this article.
Pulp
surface
area
5. Casey, J.P., Ed., Pulp and Paper
Chemistry
and Chemical
Technology,
2nd ed. (1960),
volume 2, p 621 has a discussion on the
surface area of
pulps.
The more sophisticat-
ed types of studies mentioned use silver
deposition or gas adsorption to measure the
total available surface area of pulps. These
studies give reasonably close values to each
other (within a factor of two) for surface
area. Fig. 6-23 is an approximation of the
results of Robertson and Mason (1949) cited
in this work.
6. Robertson, A.A. and S.G. Mason, Specific
surface area of cellulose fibres by the liquid
penetration method. Pulp Paper Mag. Can,
50(13):
103-110(1949).
Fiber morphology and performance
7. Dadswell, H.E. and A.J. Watson, Influence
of the morphology of woodpulp fibres on
paper properties. Transactions of the "For-
mation and Structure of
Paper"
Symposium,
25-29 Sept., 1961, pp 537-572 (1962). (See
also Appita
14(5):
168-176(1961) and ibid.
17(6):
146-156(1964).)
8. R.B. Brown, Paper Trade J. 95(13):27-
29(1932).