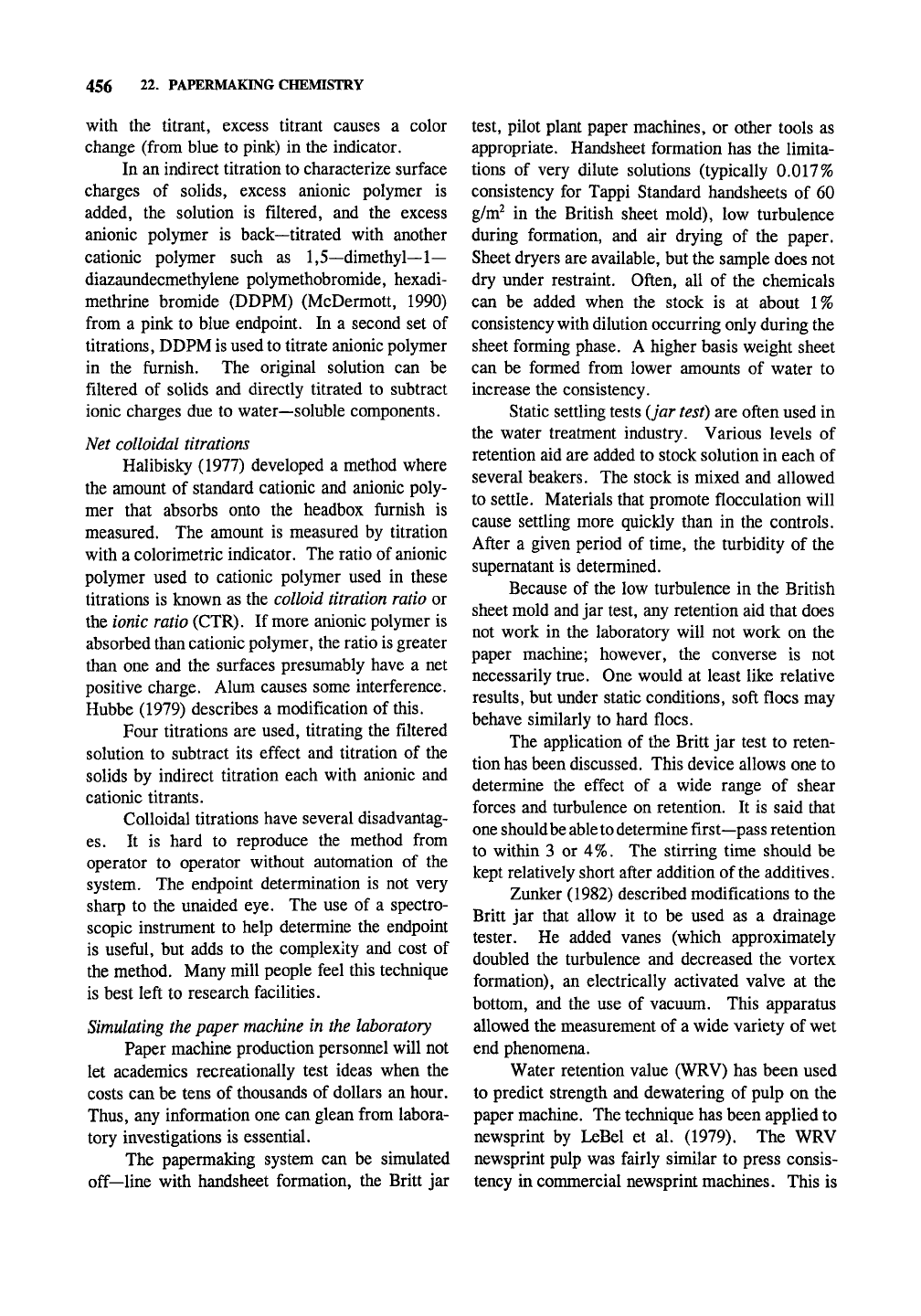
456 22. PAPERMAKING CHEMISTRY
with the titrant, excess titrant causes a color
change (from blue to pink) in the indicator.
In an indirect titration to characterize surface
charges of solids, excess anionic polymer is
added, the solution is filtered, and the excess
anionic polymer is back—titrated with another
cationic polymer such as l,5~dimethyl—1—
diazaundecmethylene polymethobromide, hexadi-
methrine bromide (DDPM) (McDermott, 1990)
from a pink to blue endpoint. In a second set of
titrations, DDPM is used to titrate anionic polymer
in the furnish. The original solution can be
filtered of solids and directly titrated to subtract
ionic charges due to water—soluble components.
Net colloidal titrations
Halibisky (1977) developed a method where
the amount of standard cationic and anionic poly-
mer that absorbs onto the headbox furnish is
measured. The amount is measured by titration
with a colorimetric indicator. The ratio of anionic
polymer used to cationic polymer used in these
titrations is known as the colloid titration ratio or
the ionic ratio (CTR). If more anionic polymer is
absorbed than cationic polymer, the ratio is greater
than one and the surfaces presumably have a net
positive charge. Alum causes some interference.
Hubbe (1979) describes a modification of this.
Four titrations are used, titrating the filtered
solution to subtract its effect and titration of the
solids by indirect titration each with anionic and
cationic titrants.
Colloidal titrations have several disadvantag-
es.
It is hard to reproduce the method from
operator to operator without automation of the
system. The endpoint determination is not very
sharp to the unaided eye. The use of a spectro-
scopic instrument to help determine the endpoint
is useful, but adds to the complexity and cost of
the method. Many mill people feel this technique
is best left to research facilities.
Simulating the paper machine in the laboratory
Paper machine production personnel will not
let academics recreationally test ideas when the
costs can be tens of thousands of dollars an hour.
Thus,
any information one can glean from labora-
tory investigations is essential.
The papermaking system can be simulated
off—line with handsheet formation, the Britt jar
test, pilot plant paper machines, or other tools as
appropriate. Handsheet formation has the limita-
tions of very dilute solutions (typically 0.017%
consistency for Tappi Standard handsheets of 60
g/m^ in the British sheet mold), low turbulence
during formation, and air drying of the paper.
Sheet dryers are available, but the sample does not
dry under restraint. Often, all of the chemicals
can be added when the stock is at about 1%
consistency with dilution occurring only during the
sheet forming phase. A higher basis weight sheet
can be formed from lower amounts of water to
increase the consistency.
Static settling tests {jar test) are often used in
the water treatment industry. Various levels of
retention aid are added to stock solution in each of
several beakers. The stock is mixed and allowed
to settle. Materials that promote flocculation will
cause settling more quickly than in the controls.
After a given period of time, the turbidity of the
supernatant is determined.
Because of the low turbulence in the British
sheet mold and jar test, any retention aid that does
not work in the laboratory will not work on the
paper machine; however, the converse is not
necessarily true. One would at least like relative
results, but under static conditions, soft floes may
behave similarly to hard floes.
The application of the Britt jar test to reten-
tion has been discussed. This device allows one to
determine the effect of a wide range of shear
forces and turbulence on retention. It is said that
one should
be
able to determine first—pass retention
to within 3 or 4%. The stirring time should be
kept relatively short after addition of the additives.
Zunker (1982) described modifications to the
Britt jar that allow it to be used as a drainage
tester. He added vanes (which approximately
doubled the turbulence and decreased the vortex
formation), an electrically activated valve at the
bottom, and the use of vacuum. This apparatus
allowed the measurement of a wide variety of wet
end phenomena.
Water retention value (WRV) has been used
to predict strength and dewatering of pulp on the
paper machine. The technique has been applied to
newsprint by LeBel et al. (1979). The WRV
newsprint pulp was fairly similar to press consis-
tency in commercial newsprint machines. This is