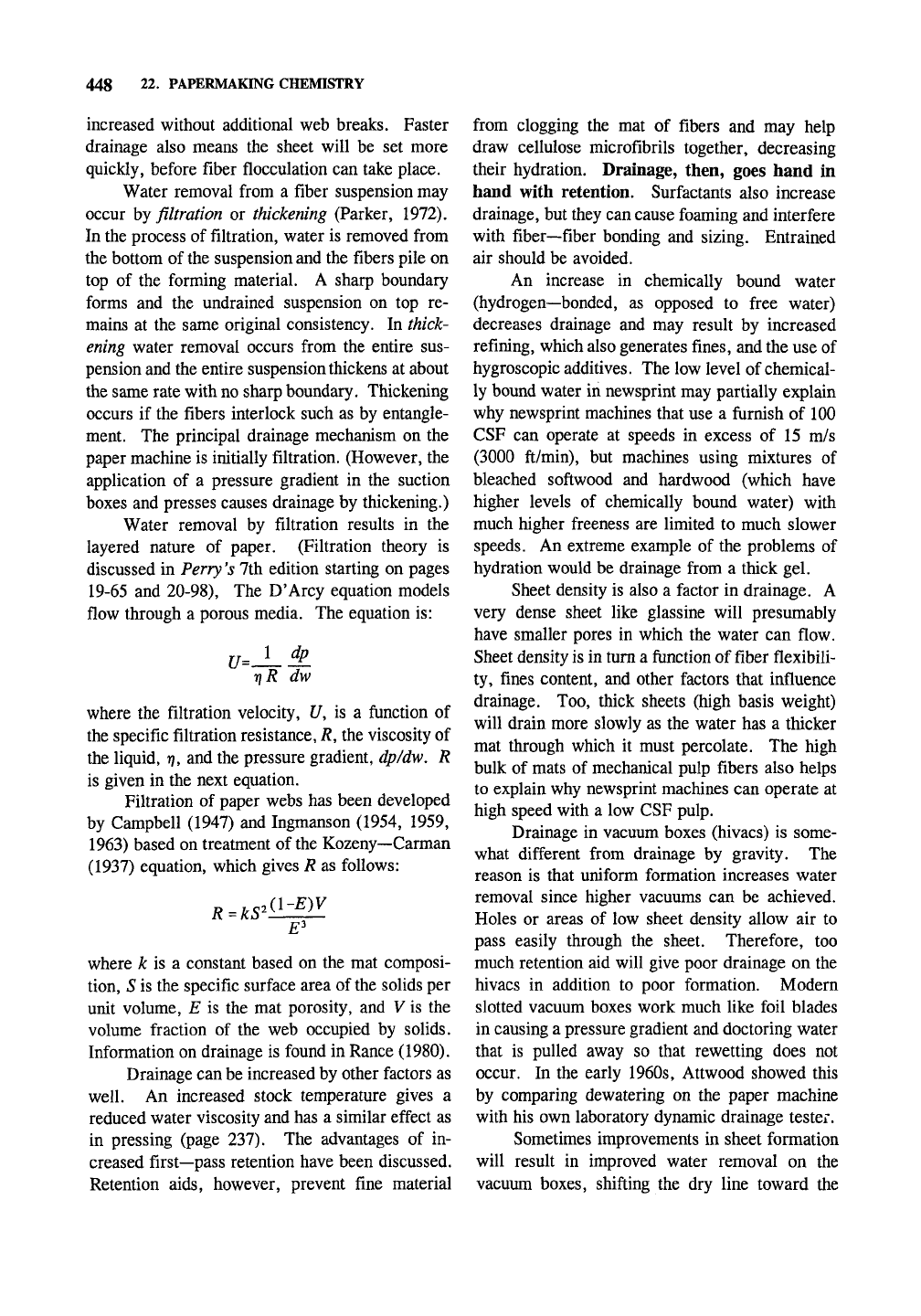
448 22. PAPERMAKING CHEMISTRY
increased without additional web breaks. Faster
drainage also means the sheet will be set more
quickly, before fiber flocculation can take place.
Water removal from a fiber suspension may
occur hy filtration or thickening (Parker, 1972).
In the process of fihration, water is removed from
the bottom of the suspension and the fibers pile on
top of the forming material. A sharp boundary
forms and the undrained suspension on top re-
mains at the same original consistency. In thick-
ening water removal occurs from the entire sus-
pension and the entire suspension
thickens
at about
the same rate with no sharp boundary. Thickening
occurs if the fibers interlock such as by entangle-
ment. The principal drainage mechanism on the
paper machine is initially filtration. (However, the
application of a pressure gradient in the suction
boxes and presses causes drainage by thickening.)
Water removal by filtration results in the
layered nature of paper. (Filtration theory is
discussed in
Perry *s
7th edition starting on pages
19-65 and 20-98), The D'Arcy equation models
flow through a porous media. The equation is:
U=
I dp
rjR dw
where the filtration velocity, U, is a function of
the specific filtration resistance, R, the viscosity of
the liquid, rj, and the pressure gradient, dp/dw. R
is given in the next equation.
Filtration of paper webs has been developed
by Campbell (1947) and Ingmanson (1954, 1959,
1963) based on treatment of the Kozeny—Carman
(1937) equation, which gives R as follows:
R-kS^(±E}I
where
A:
is a constant based on the mat composi-
tion, S is the specific surface area of the solids per
unit volume, E is the mat porosity, and V is the
volume fraction of the web occupied by solids.
Information on drainage is found in Ranee (1980).
Drainage can be increased by other factors as
well. An increased stock temperature gives a
reduced water viscosity and has a similar effect as
in pressing (page 237). The advantages of in-
creased first—pass retention have been discussed.
Retention aids, however, prevent fine material
from clogging the mat of fibers and may help
draw cellulose microfibrils together, decreasing
their hydration. Drainage, then, goes hand in
hand with retention. Surfactants also increase
drainage, but they can cause foaming and interfere
with fiber—fiber bonding and sizing. Entrained
air should be avoided.
An increase in chemically bound water
(hydrogen—bonded, as opposed to free water)
decreases drainage and may result by increased
refining, which also generates fines, and the use of
hygroscopic additives. The low level of chemical-
ly bound water in newsprint may partially explain
why newsprint machines that use a furnish of 100
CSF can operate at speeds in excess of 15 m/s
(3000 ft/min), but machines using mixtures of
bleached softwood and hardwood (which have
higher levels of chemically bound water) with
much higher freeness are limited to much slower
speeds. An extreme example of the problems of
hydration would be drainage from a thick gel.
Sheet density is also a factor in drainage. A
very dense sheet like glassine will presumably
have smaller pores in which the water can flow.
Sheet density is in turn a function of fiber flexibili-
ty, fines content, and other factors that influence
drainage. Too, thick sheets (high basis weight)
will drain more slowly as the water has a thicker
mat through which it must percolate. The high
bulk of mats of mechanical pulp fibers also helps
to explain why newsprint machines can operate at
high speed with a low CSF pulp.
Drainage in vacuum boxes (hivacs) is some-
what different from drainage by gravity. The
reason is that uniform formation increases water
removal since higher vacuums can be achieved.
Holes or areas of low sheet density allow air to
pass easily through the sheet. Therefore, too
much retention aid will give poor drainage on the
hivacs in addition to poor formation. Modern
slotted vacuum boxes work much like foil blades
in causing a pressure gradient and doctoring water
that is pulled away so that rewetting does not
occur. In the early 1960s, Attwood showed this
by comparing dewatering on the paper machine
with his own laboratory dynamic drainage tester.
Sometimes improvements in sheet formation
will result in improved water removal on the
vacuum boxes, shifting the dry line toward the