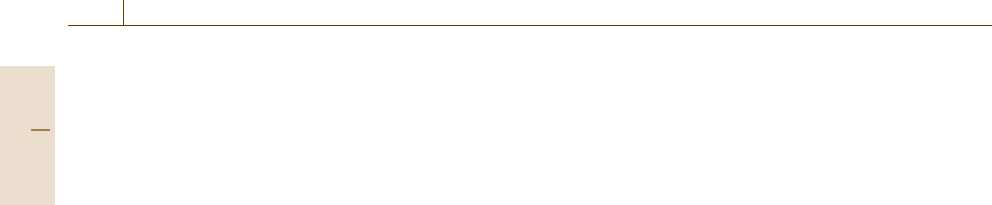
352 Part C Materials Properties Measurement
Comparing the Static and Dynamic Methods
From a historical perspective, the static methods of
determining elastic constants were the first to be devel-
oped. Dynamic methods were only discovered in the
1930s [7.33, 34] and required some time to become
known and then popular. Standards for the static meth-
ods of determining elastic constants were developed in
the 1950s. For example, ASTM E 111 was first issued
in 1955. The dynamic techniques required a rather com-
plex theoretical analysis and a numerical evaluation in
order to know the resonant frequencies as a function of
specimen shape, density and dimensions. Also, mod-
ern electronics had to have been developed before the
measurements could be made to determine resonant fre-
quencies. It was not until the late 1950s that progress
was sufficient that the dynamic techniques could be de-
velopedinsuchawayastobeeasytouseanduseful.
The first ASTM designation for measurement of elastic
constants by resonance was C 623 in 1969, i. e., about
10 years after the technique was developed.
Ide [7.33] recognized the advantages of dynamic
techniques over static techniques of determining elastic
constants as early as 1935. He stated,
Dynamic methods for measuring Young’s modu-
lus of elasticity possess advantages over the usual
static methods. The dynamic modulus is obtained
for minute alternating stresses far below the elastic
limit, which do not give rise to complex creep ef-
fects or to elastic hysteresis. This accurately fulfills
the assumptions of the mathematical theory.
This opinion about the inherent superiority is still held
today. In a study by Smith et al. [7.11], the authors
used dynamic test techniques to determine the Young’s
modulus of an Inconel alloy to an accuracy of bet-
ter than 1% of the mean value. The static techniques
could only achieve an accuracy of between 5 and 7%
on the same alloy. These authors recommend one of
the dynamic techniques (impulse excitation) for rou-
tine quality-control work because of their accuracy and
simplicity. The continuous excitation method was rec-
ommended for more complete elastic characterization
studies of materials. A major advantage of the impulse
technique is that a nodal analysis is not required to de-
termine the resonance frequencies. They feel that the
static method is not desirable for quality-control work,
because it is a labor-intensive technique that is time-
consuming.
There are fundamental reasons for differences be-
tween the dynamic and static techniques [7.39]. Static
tests are isothermal because there is plenty of time
for heat conduction during the test. Ultrasonic tests
take place so fast that the conditions are adiabatic and
the sample’s temperature actually changes during the
test. Resonant tests are usually adiabatic, but this de-
pends on the resonant frequency and the size of the
specimen. Dislocation bowing and other sources of in-
ternal friction always take place during static tests and
never during ultrasonic tests. Again, resonant tests may
or may not be affected by these phenomena. In fact,
tests in which the frequency is changed are used to
characterize these effects. Static tests tend to explore
higher stresses than dynamic tests. Therefore, higher-
order elastic behavior is implicitly included in static
measurements.
If the application is highly loaded and static in na-
ture, such as in a building, ship, or bridge, the static
methods for measuring modulus are more appropriate
despite the uncertainty levels mentioned above. If the
application is dynamic in nature, such as ballistic pen-
etration or elastic wave propagation, one should use
dynamic methods to evaluate the elastic constants.
7.1.5 Instrumented Indentation
as a Method of Determining
Elastic Constants
Up to this point, the discussion has involved what
may be regarded as standard test methods. The meth-
ods are standard in the sense that they were developed
to evaluate the elastic constants of materials that are
of a macroscopic size. The materials are uniform and
can be considered to behave as a continuum. Chem-
ically and microstructurally the materials are uniform
throughout. Most standard materials are first manufac-
tured and then are machined to the size and shape of
the part. The elastic constants of the materials are the
same in the part as in the bulk. In the case of mater-
ials that are manufactured directly into parts (H-beams,
motor castings, etc.), the parts are large enough that
pieces can be removed to measure their property, and
the property measured in this way is assumed to be
identical to the property in the part. For certain appli-
cations, however, removal of pieces from the part is not
an easy option; the parts may be too small to have pieces
removed from them in such a way as to be representa-
tive of the part on the whole. Also, the piece removed
may be too small to be tested by standard means. Ma-
terials that fit this category include multilayers, and
interlayers in electronic components, component parts
of microelectromechanical systems (MEMS), and ther-
Part C 7.1