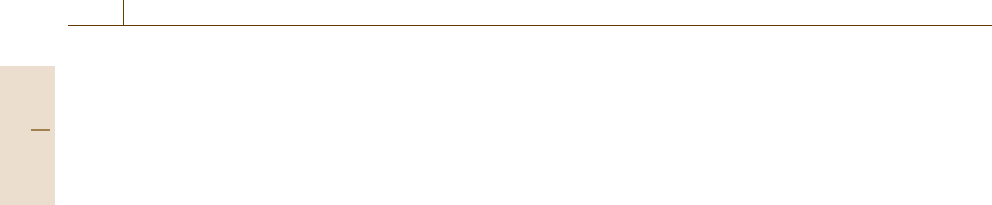
358 Part C Materials Properties Measurement
for plastic behavior that employ each of these loading
modes and are the subject of this section on plasticity.
In uniaxial tension, a bar or sheet is pulled along its
long axis. The stress in the bar is calculated by dividing
the applied force by the cross-sectional area of the bar.
The strain is determined from the change in length of
an initial, fiducial length. In uniaxial compression abar
is subject to compressive loading along one axis and
the stress and strain are determined in much the same
way as for tension. Both tension and compression have
components of hydrostatic tension or pressure which
may affect the ultimate behavior, but not the yielding
or workhardening behavior. One of the great values of
tension and compression testing arises from the fact
that the stress and strain are uniform and simply calcu-
lated from applied forces, displacements, and specimen
dimensions.
In practice, shear results in some bending and bend-
ing results in some shear loading. The shear stress is
the tangential surface force divided by the surface area.
The shear strain is defined as the change in angle that
results. Bending develops additional tensile and com-
pressive loading away from the neutral axis resulting in
mean stress effects. Pure shear and torsion (which gen-
erates pure shear) do not develop any significant level
of mean stress.
Lastly, combinations of loading modes are used to
assess the effect of complex stress or strain states on
plasticity and ultimate behavior. Bulge testing or cup
testing is largely a biaxial tension test for sheet ma-
terial with a small component of bending. The ratio
of the stress or strain in the two orthogonal directions
can be adjusted by cut outs or specimen shape. One of
the most popular tests for plasticity, the hardness test,
is a complex multiaxial compression test with a high,
superimposed pressure (Sect. 7.3).
7.2.3 Standard Methods
of Measuring Plastic Properties
This section lists and briefly describes standard tests
used to measure plastic behavior. Some of the most crit-
ical features of each method and their limitations are
discussed. As noted above, plasticity is highly sensitive
to the stress and strain state. Thus, the methods are clas-
sified according to loading mode and listed in order of
importance or frequency of performance.
Hardness Tests
Whereas hardness is treated in detail in the next sec-
tion, Sect. 7.3, a glimpse of plasticity in hardness is also
made here. The hardness of a material as measured by
the indentation test methods quantifies a material’s re-
sistance to plastic flow. By definition, a soft material
deforms plastically more easily than a hard mater-
ial. Indentation tests are used industrially for quality
control. They are the most frequently performed me-
chanical tests because of their simplicity, rapidity, low
cost, and usually nondestructive nature. In the inden-
tation test, a spherical or pointed indenter is pressed
into the surface of a material by a predetermined force.
The depth of the resulting indentation or the force
divided by the area of the resulting indentation is
a measure of the hardness. However, these tests mea-
sure the resistance to plastic deformation in complex,
multiaxial, and nonuniform stress and strain fields at
varying strain rates. Thus, the interpretation of these
tests in terms of more common concepts is difficult.
The yield strength, workhardening, or ultimate tensile
strength can only be estimated by empirical correla-
tion. The ductility cannot be estimated by any means.
It is extremely difficult to use the results from these
tests analytically to accurately describe plastic defor-
mation in other applications. This drawback is being
addressed by instrumented indentation test standards
(ISO 14577 [7.62] and efforts underway at ASTM). The
commercial importance of hardness testing cannot be
underestimated and justifies an entire Sect. 7.3 devoted
entirely to hardness.
Tension Tests
The uniaxial tension test is the most important test for
measuring the plastic properties of materials for specifi-
cation and analytical purposes. It provides well-defined
measures of yielding, workhardening, ultimate tensile
strength, and ductility. It is also used to measure the
temperature dependence and strain rate sensitivity of
these quantities. Versions of the tension test provide im-
portant parameters for predicting forming behavior. The
tension test is carried out on a bar, plate, or strip of ma-
terial that has a region of reduced cross-sectional area,
the gage section (Fig. 7.22). The reduced area causes all
plastic deformation to occur in the gage section. The
unreduced ends are held in grips (Fig. 7.4 of Sect. 7.1)
and the specimen is elongated parallel to its long axis.
Initially, the sample deforms elastically, as described
in Sect. 7.1, and in linear proportion to the applied stress
as shown schematically in Fig. 7.23. At some applied
force, nonlinear and unrecoverable deformation, i. e.,
plasticity begins. The proportional limit is the force
at the onset of plasticity divided by the initial cross-
sectional area of the sample.
Part C 7.2