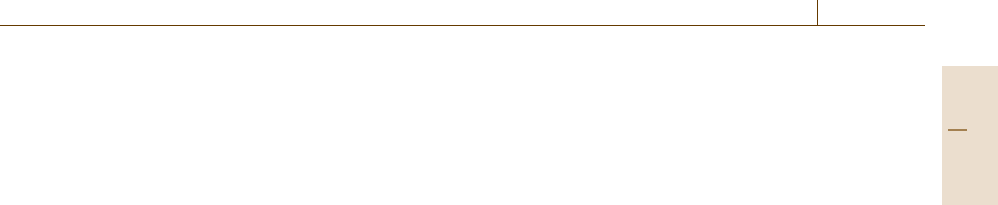
Mechanical Properties 7.3 Hardness 375
test material, the deformation surrounding the indenta-
tion may extend to the edge and push out the material,
thus affecting the measured hardness value. Similarly, if
the deformation extends completely through the thick-
ness of thin test material, then the deformed material
may flow at the interface with the supporting anvil, or
the anvil material may contribute to the hardness mea-
surement. These problems can influence the deformation
process likely causing the test to give erroneous hardness
results. Consequently, in cases where a hardness test is
to be made on narrow-width or thin material or mater-
ial having a small area, an appropriate hardness test and
scale must be chosen that produces indentations small
enough to prevent this edge interaction. Also keep in
mind that the area surrounding a previously made inden-
tation may also affect a new hardness test due to induced
residual stress and areas of workhardening surrounding
the indentation. Therefore, the number of indentations
that will be made must be taken into consideration when
small test areas are involved.
Material Composition and Homogeneity
The size and location of metallurgical features within
the test material should be considered when choosing
the hardness test method and hardness scale. For mater-
ials that are not homogeneous, an appropriate hardness
test and scale should be chosen that will produce a suf-
ficiently large indentation representative of the material
as a whole. For example, forgings and cast iron are typ-
ically tested using the Brinell method. If the subject of
interest is a material artifact, such as a decarburization
zone or a thin material layer, then a hardness test and
scale should be chosen that produces a small or shal-
low indentation. In an analogous way to the issues of
test-piece size, the closeness to adjacent regions of a dif-
fering hardness, such as the heat-affected zone of a weld,
should also be considered. If the deformation zone sur-
rounding an indentation extends into these regions, the
test measurement may be influenced. In such cases, an
appropriate hardness test and scale should be chosen that
uses test forces and indenter that produce a small enough
indentation to avoid the influence of these areas.
Permissible Damage
One of the greatest attributes of a hardness test is that it
is essentially a nondestructive test, leaving only a small
indentation which usually does not detract from a prod-
uct’s function or appearance. However, there are some
applications for which a hardness indentation of a cer-
tain size could be detrimental to a product’s service or
appearance. For example, it is possible that an inden-
tation could act as an initiation point for a fracture in
a part subjected to cyclic loading, or a large visible in-
dentation could affect the appearance of a product. In
these cases, smaller indentations may be the solution.
Test Surface Preparation
When the ability to prepare the testing surface is not
possible or practical or is limited, a hardness method
and hardness scale must be chosen that is less sensi-
tive to the level of surface preparation. The degree of
surface roughness that can be tolerated by the different
hardness testing methods is generally dependent on the
force levels to be applied, indenter size and resultant
indentation size. In general, the larger the indentation
size and depth, the less sensitive is the hardness test to
the level of surface roughness and imperfections, and
the more likely the measurement will represent the true
hardness value of a material. This is particularly true
for the Brinell, Vickers and Knoop methods because of
the need to accurately resolve and measure the resultant
indentation. The larger the sizes of surface anomalies
with respect to the indentation size, the more likely it
becomes that errors in the indentation measurement and
the hardness result will increase.
An important feature of the Rockwell test method,
which bases the hardness result on depth measurement
rather than indentation size, is the use of the prelimi-
nary force as part of the testing cycle. Application of the
preliminary force acts to push the indenter through mi-
nor surface imperfections and to crush residual foreign
particles present on the test surface. By establishing
a reference beneath the surface prior to making the first
depth measurement, it allows testing of materials with
slight surface flaws while maintaining much of the test
accuracy.
As a general guide, the high-force scales of the
Brinell test method requires the least surface prepa-
ration, such as a surface that has been filed, ground,
machined or polished with no. 000 emery paper. Mater-
ial tested by the Rockwell test method usually does not
need to be polished, but should be smooth, clean and
free of scale. The Brinell test method and the heavy-
force Vickers scales producing small indentations are
likely to require polished surfaces to allow accurate
measurement of the indentation sizes.
Permissible Measurement Uncertainty
The measurement uncertainty of a hardness test is in-
fluenced by many factors, including, among others, the
operator, the machine’s repeatability and reproducibil-
ity, and the testing environment (Sect. 7.3.3). With
Part C 7.3