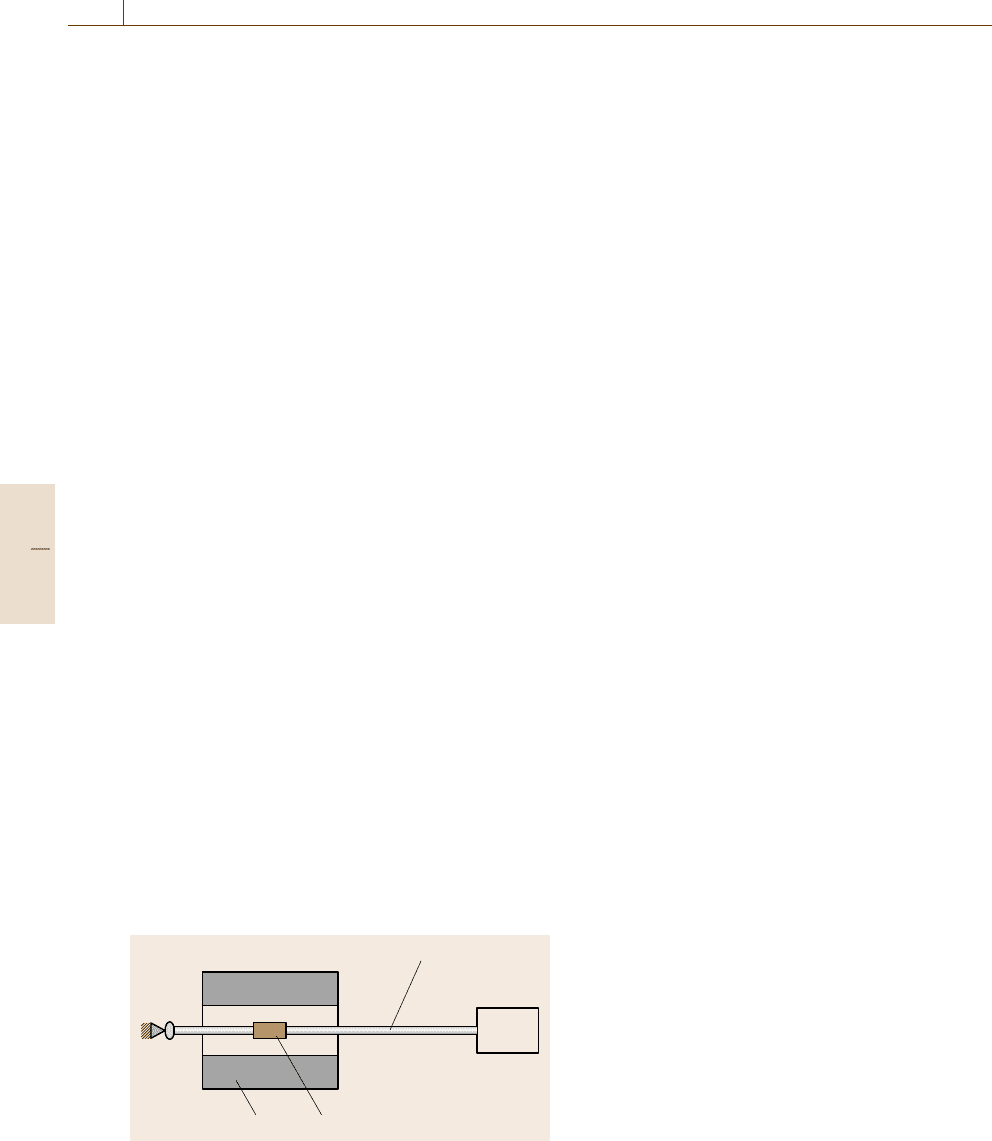
564 Part C Materials Properties Measurement
At higher frequencies the resistance of the winding dif-
fers from the DC resistance due to the skin effect. In
this case mutual inductance bridges provide more accu-
rate results, as in these circuits the resistance of the wire
does not enter the measuring result. The specimens must
be equipped with two windings. Suitable circuits are the
Wilde [10.18] and Hartshorn bridges. Further methods
are compiled in [10.19].
Measurement of Magnetostriction. Magnetostriction
comprises all dimensional changes of a specimen that
are caused by changes in magnetization. For both the
volume-invariant shape effect and the volume magne-
tostriction, a measurement of a change of the specimen
length in one or more dimensions can be carried out.
The specimen is placed in the center of a solenoid,
which generates the magnetic field required. The
change in length is transferred via a rod to a dis-
placement transducer that is located outside the stray
field of the solenoid. The material of the rod must be
properly chosen to keep the outer force acting on the
specimen as small as possible and to avoid errors due
to temperature-induced changes in length. Capacitive,
inductive or optical sensors are used to measure the
displacement.
Another method uses strain gauges that are directly
attached to the specimen. To cancel out errors due to the
magnetic and thermal properties of the strain-sensing
element, a second element of the same type can be at-
tached to a substrate that shows no magnetostriction but
is exposed to the same environment. The two sensing
elements can be connected to opposite paths of a bridge
circuit.
A third method uses a single-mode optical fiber
attached to the specimen. The fiber is part of an inter-
ferometer. The change in length is detected as a phase
shift in the electromagnetic wave propagating in the
fiber [10.20].
12
3
4
Fig. 10.25 Magnetostriction measurement: 1 – solenoid, 2
– specimen, 3 – specimen rod, 4 – displacement transducer
The volume magnetostriction can also be measured
by the conventional measuring method for volumetric
content. The specimen, immersed in a liquid, is exposed
to the magnetic field.
Magnetostriction is an important parameter in many
applications of electrical steel. A comprehensive de-
scription of magnetostriction measuring methods for
these materials can be found in [10.21].
Measurement of the Hysteresis Loop
of Amorphous or Nanocrystalline Ribbons
Sample Shape. In the case of soft magnetic ribbons the
hysteresis loop can be measured on
1. open ribbons, in which case the demagnetizing fac-
tor has to be considered,
2. toroids.
The temperature the loop is measured is also important.
In the case of low- or high-temperature measurements
the system has to withstand the desired temperature.
In principle, magnetic measurements should always
be carried out on a toroid instead of open ribbons be-
cause only then is a closed magnetic circuit realized.
For ribbons this method has the disadvantage that the
material is not in a stress-free state – there is a tensile
stress on the outer surface and comprehensive stress on
the inner surface. Another possibility is to use a single
straight ribbon but then the demagnetizing field has to
be considered.
Hysteresis Loop on a Single Ribbon. When hystere-
sis is measured on a single open ribbon a well-defined
external stress can be applied. Temperature-dependent
measurements are possible, although technically more
complex. The facilities necessary for measuring the hys-
teresis loop are field coils, a compensated pickup coil,
a current source, an ammeter and an integrator (flux-
meter). For the measurement of coercivity a Helmholtz
coil is mainly used, and for the measurement of satura-
tion magnetization the field is applied by a cylindrical
coil producing a sufficient high field. The coils are en-
ergized by a computer-controlled power supply.
The devices are connected and controlled by a data-
acquisition and control unit, forming a full automatic
hysteresis-loop system. Figure 10.26 shows as an exam-
ple a set up for such a hysteresis measurement on single
strip ribbons.
In this case a compensated pickup system has to be
used. When the pickup and the compensation coils are
connected, so that the induction signals due to the field
Part C 10.2