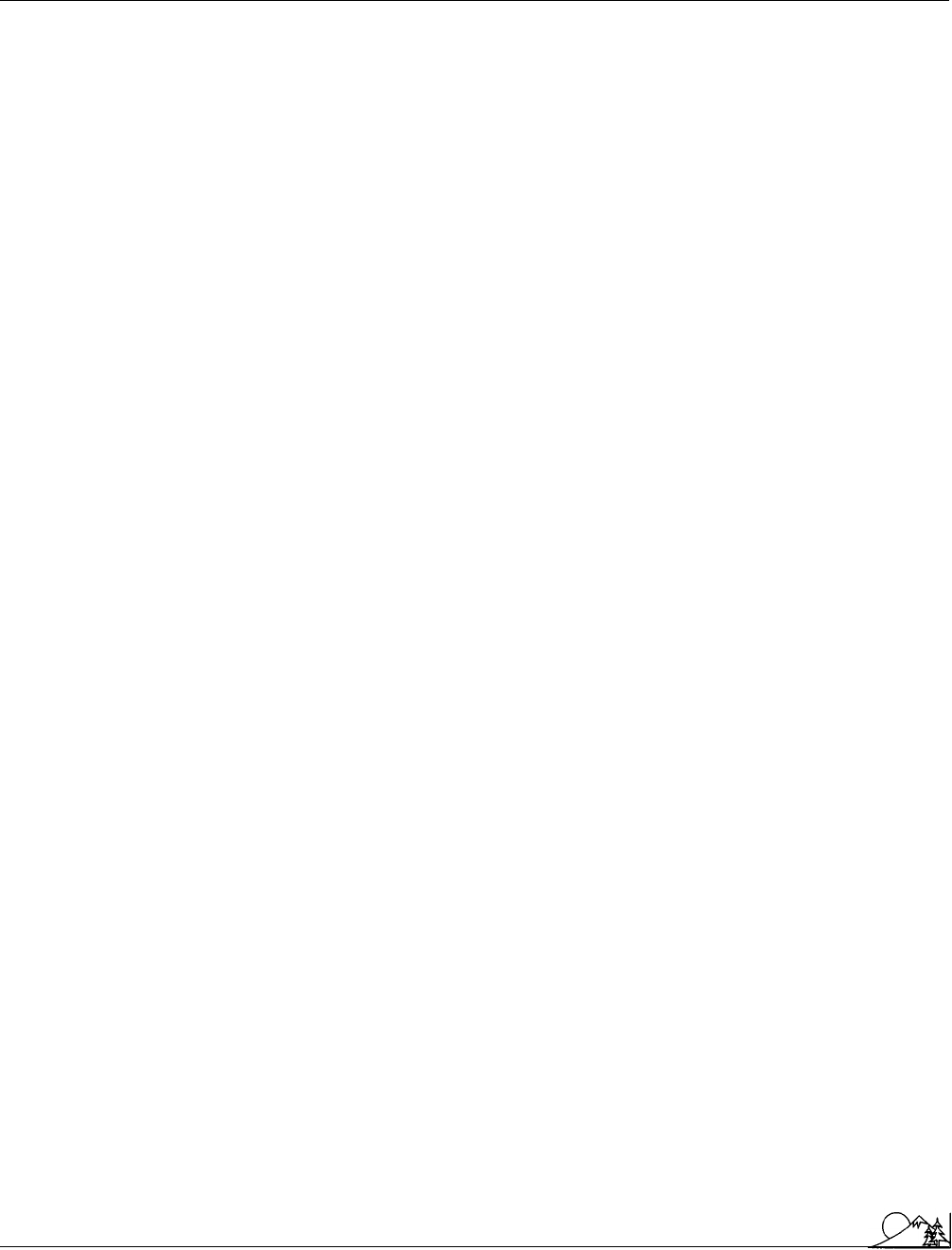
Environmental Encyclopedia 3
Refuse-derived fuels
nature, most solid wastes are potentially valuable as fuels. A
typical sample of municipal waste in the United States, for
instance, may consist of about 30–40% paper, 5% textiles,
5% wood, and 20–30% organic material. All of these materi-
als are combustible. Metals, glass,
plastics
, sand, and other
non-combustible materials constitute the remaining portion
of a waste sample. Each of these non-combustible materials
is potentially recyclable.
Even though 70% or more of municipal wastes appear
to have potential value as sources of fuel, that potential has
not, as yet, been extensively developed. In most countries,
solid wastes are mainly disposed of in landfills. A small
fraction is incinerated or used for other purposes. However,
conversion of solid wastes to a useable fuel is still an experi-
mental process.
The primary roadblock to the commercial develop-
ment of RDFs is the economic cost of preparing such fuels.
Given that most RDFs produced have only about half the
energy value of a typical sample of industrial
coal
and given
the relatively low price of coal, there is little economic incen-
tive for municipalities to build energy systems based on
refuse-derived fuels.
Many scientists, engineers, and environmentalists see
a positive future for refuse-derived fuels. They argue that as
fossil fuel reserves are consumed, the cost of traditional fuels
such as coal, gas, and oil will inevitably increase. In addition,
RDFs tend to burn more cleanly and have a significant
environmental advantage over coal and other
fossil fuels
.
Research must continue, therefore, to develop more efficient
and less expensive RDFs and associated processes to obtain
and use them.
One of the fundamental problems in the development
of refuse-derived fuels is obtaining the raw materials in a
physical condition that will allow the extraction of combusti-
ble organic matter. The solid waste material entering most
landfills consists of a complex mixture of substances. Some
of these are combustible while others are not. Some have
other commercial values while others have none. Plastics
provide a convenient example that illustrates both of these
aspects.
The first step in preparing wastes for the production
of refuse-derived fuels is known as size reduction. In this
step, waste materials are shredded, chopped, sliced, pulver-
ized, or otherwise treated in order to break them up into
smaller pieces. Most methods for separating combustible
from non-combustible materials require that waste particles
be small in size. Both
magnetic separation
and air classifi-
cation will work only with small particles.
Size reduction also serves a number of other functions.
For example, it breaks open plastic and glass bottles, releasing
any contents that may still be in them. It also reduces clump-
ing and tangling that often occurs with larger particles. Fi-
1184
nally, when used as a fuel, particles of small size burn more
efficiently than larger particles.
One indication of the importance of size reduction in
the production of RDFs is the number of different machines
that have been developed to accomplish this step. Bag break-
ers are used to tear open plastic bags and cardboard boxes.
Machines called chippers reduce cut wood into small pieces.
Granulators have sharp knives on rotating blades. These
devices cut materials against a stationary blade, somewhat
similar to a pair of scissors. Flail mills are rotary machines
that swing hammers around in a circle to smash materials.
Ball and rod mills consist of cylindrical drums that hold
balls or rods. When the drums spin, balls or rods smash
against the inside of the drum, crushing solid wastes also
present in them.
Once waste materials have been reduced in size, the
portion that is combustible must be removed from that which
is not. Several different procedures can be used. A common
process, for example, is to pass the solid wastes under a
magnet. The magnet will extract all metals containing iron
(ferrous) from the mixture.
Another technique is rotary screening, in which wastes
are spun in a drum and sorted using screens that have open-
ings of either 50 mm or 200 mm diameter. Sand, broken
glass, dust, and other non-organic materials that do not burn
tend to be removed by this procedure.
A third process is known as air classification. When
solid wastes are exposed to a blast of air, various components
are separated from each other on the basis of their size,
shape, density, and moisture content. A number of different
kinds of air classifiers exist, and all are reasonably efficient
in separating organic from inorganic materials.
One type of air classifier is the horizontal model, in
which size-reduced wastes are dropped into a horizontal
stream of air. Various types of material are separated on the
basis of the horizontal distance they travel from their point
of origin. Vertical classifiers separate on a similar principle
except that particles are injected into a rising stream of air.
The rotary classifier consists of an inclined cylindrical col-
umn into which wastes are injected and then separated by
a rotating, rising column of air.
The organic matter that remains after size reduction
and separation can be used as a fuel in four distinct ways.
First of all, it can be converted to other combustible forms
through pyrolysis. Pyrolysis is a process in which organic
materials are heated to high temperatures in an oxygen-
free or oxygen-deficient
atmosphere
. The product of this
reaction is a mixture of gaseous, liquid, and solid compounds.
The solid compounds can be used as fuels and are collectively
called char.
Two particularly valuable fuels,
methane
(a gas) and
ethanol
(ethyl alcohol, a liquid), can also be produced from