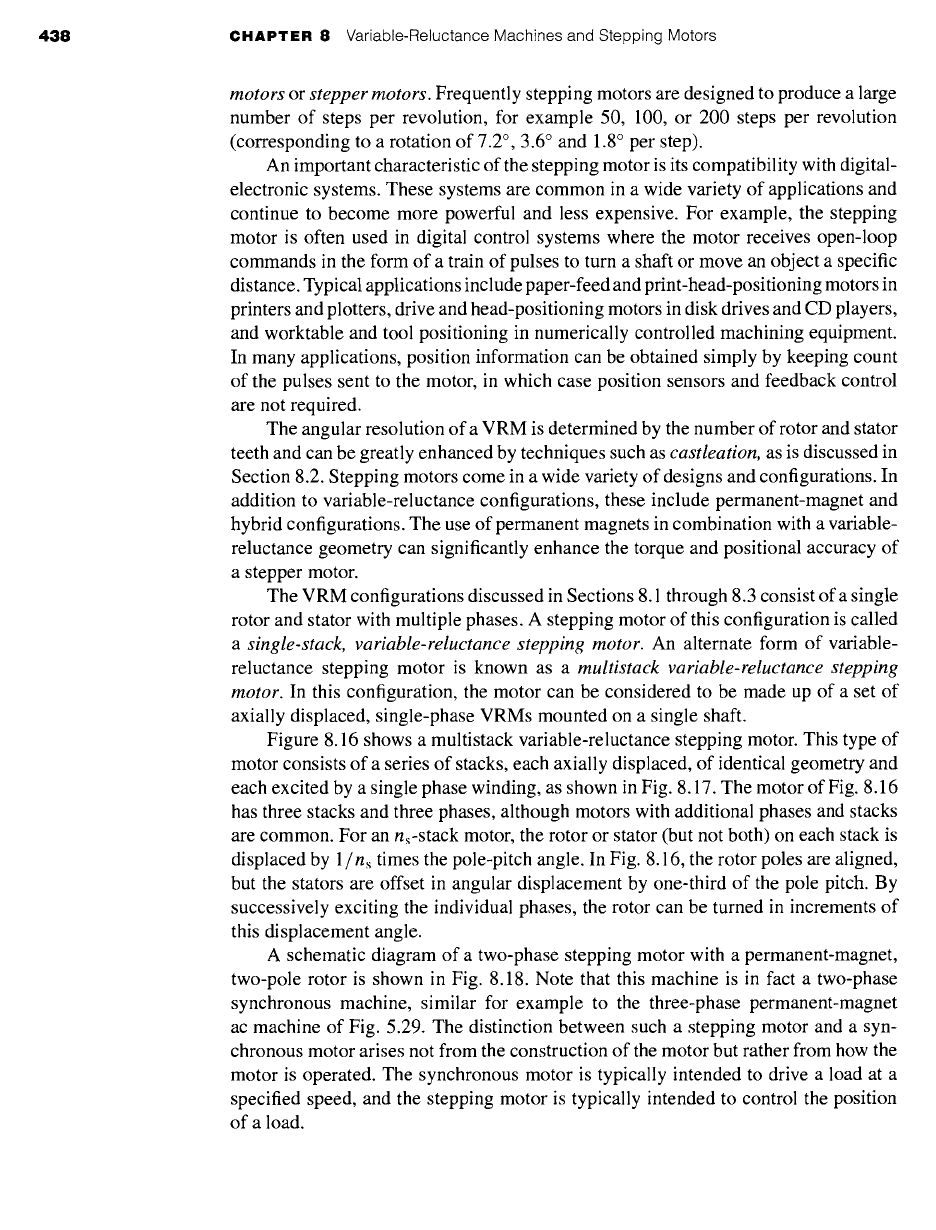
438 CHAPTER 8 Variable-Reluctance Machines and Stepping Motors
motors
or
stepper motors.
Frequently stepping motors are designed to produce a large
number of steps per revolution, for example 50, 100, or 200 steps per revolution
(corresponding to a rotation of 7.2 °, 3.6 ° and 1.8 ° per step).
An important characteristic of the stepping motor is its compatibility with digital-
electronic systems. These systems are common in a wide variety of applications and
continue to become more powerful and less expensive. For example, the stepping
motor is often used in digital control systems where the motor receives open-loop
commands in the form of a train of pulses to turn a shaft or move an object a specific
distance. Typical applications include paper-feed and print-head-positioning motors in
printers and plotters, drive and head-positioning motors in disk drives and CD players,
and worktable and tool positioning in numerically controlled machining equipment.
In many applications, position information can be obtained simply by keeping count
of the pulses sent to the motor, in which case position sensors and feedback control
are not required.
The angular resolution of a VRM is determined by the number of rotor and stator
teeth and can be greatly enhanced by techniques such as
castleation,
as is discussed in
Section 8.2. Stepping motors come in a wide variety of designs and configurations. In
addition to variable-reluctance configurations, these include permanent-magnet and
hybrid configurations. The use of permanent magnets in combination with a variable-
reluctance geometry can significantly enhance the torque and positional accuracy of
a stepper motor.
The VRM configurations discussed in Sections 8.1 through 8.3 consist of a single
rotor and stator with multiple phases. A stepping motor of this configuration is called
a single-stack, variable-reluctance stepping motor.
An alternate form of variable-
reluctance stepping motor is known as a
multistack variable-reluctance stepping
motor.
In this configuration, the motor can be considered to be made up of a set of
axially displaced, single-phase VRMs mounted on a single shaft.
Figure 8.16 shows a multistack variable-reluctance stepping motor. This type of
motor consists of a series of stacks, each axially displaced, of identical geometry and
each excited by a single phase winding, as shown in Fig. 8.17. The motor of Fig. 8.16
has three stacks and three phases, although motors with additional phases and stacks
are common. For an n~-stack motor, the rotor or stator (but not both) on each stack is
displaced by 1 / n~ times the pole-pitch angle. In Fig. 8.16, the rotor poles are aligned,
but the stators are offset in angular displacement by one-third of the pole pitch. By
successively exciting the individual phases, the rotor can be turned in increments of
this displacement angle.
A schematic diagram of a two-phase stepping motor with a permanent-magnet,
two-pole rotor is shown in Fig. 8.18. Note that this machine is in fact a two-phase
synchronous machine, similar for example to the three-phase permanent-magnet
ac machine of Fig. 5.29. The distinction between such a stepping motor and a syn-
chronous motor arises not from the construction of the motor but rather from how the
motor is operated. The synchronous motor is typically intended to drive a load at a
specified speed, and the stepping motor is typically intended to control the position
of a load.