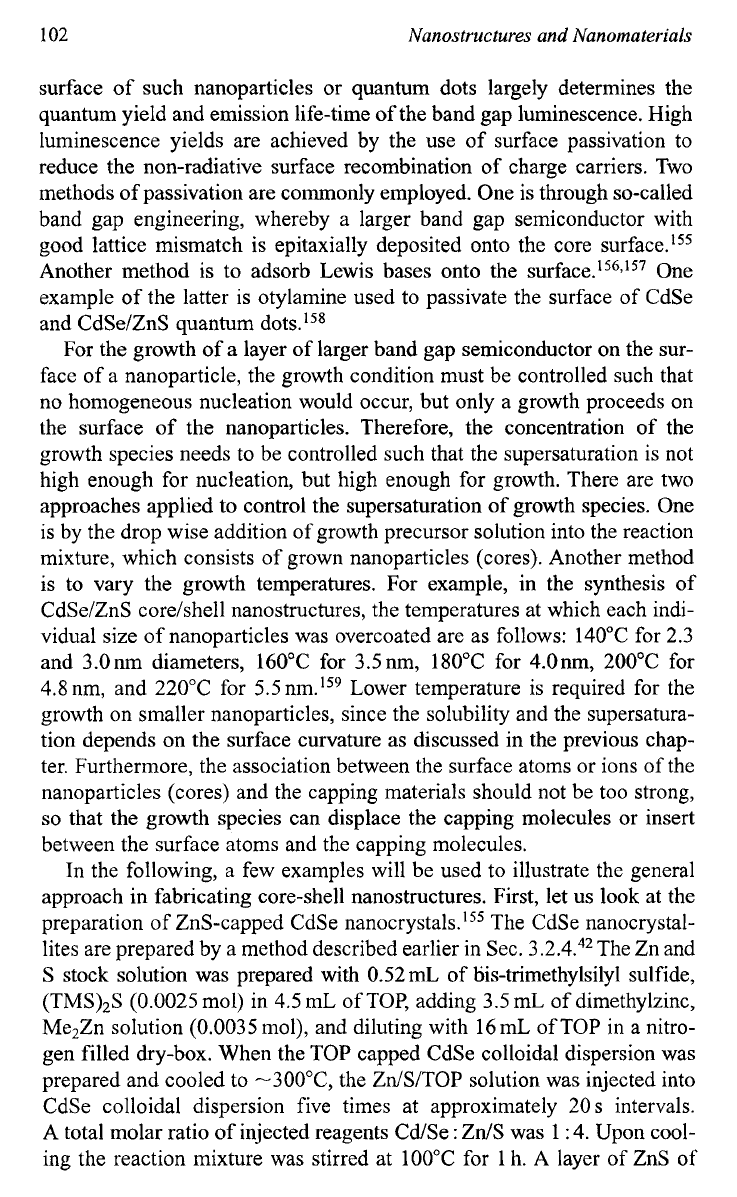
102
Nanostructures and Nanomaterials
surface of such nanoparticles or quantum dots largely determines the
quantum yield and emission life-time of the band gap luminescence. High
luminescence yields are achieved by the use of surface passivation to
reduce the non-radiative surface recombination of charge carriers. Two
methods of passivation are commonly employed. One is through so-called
band gap engineering, whereby a larger band gap semiconductor with
good lattice mismatch
is
epitaxially deposited onto the core surface.
lS5
Another method is to adsorb Lewis bases onto the ~urface.'~~,'~~ One
example of the latter is otylamine used to passivate the surface of CdSe
and CdSefZnS quantum dots.'58
For the growth of a layer of larger band gap semiconductor on the sur-
face of a nanoparticle, the growth condition must be controlled such that
no homogeneous nucleation would occur, but only a growth proceeds on
the surface of the nanoparticles. Therefore, the concentration of the
growth species needs to be controlled such that the supersaturation is not
high enough for nucleation, but high enough for growth. There are two
approaches applied to control the supersaturation of growth species. One
is by the drop wise addition of growth precursor solution into the reaction
mixture, which consists of grown nanoparticles (cores). Another method
is
to vary the growth temperatures. For example, in the synthesis of
CdSe/ZnS core/shell nanostructures, the temperatures at which each indi-
vidual size of nanoparticles was overcoated are
as
follows: 140°C for 2.3
and 3.0nm diameters, 160°C for 3.5nm, 180°C for 4.0nm, 200°C for
4.8nm, and 220°C for 5.5nm.Is9 Lower temperature is required for the
growth on smaller nanoparticles, since the solubility and the supersatura-
tion depends on the surface curvature as discussed in the previous chap-
ter. Furthermore, the association between the surface atoms or ions of the
nanoparticles (cores) and the capping materials should not be too strong,
so
that the growth species can displace the capping molecules or insert
between the surface atoms and the capping molecules.
In the following, a few examples will be used to illustrate the general
approach in fabricating core-shell nanostructures. First, let us
look
at the
preparation of ZnS-capped CdSe nanocrystal~.'~~ The CdSe nanocrystal-
lites are prepared by a method described earlier in Sec. 3.2.4.42 The Zn and
S
stock solution was prepared with 0.52 mL of ljis-trimethylsilyl sulfide,
(TMS)$3 (0.0025 mol) in 4.5 mL of
TOP,
adding
3.5
mL of dimethylzinc,
Me,Zn solution (0.0035 mol), and diluting with 16 mL of TOP in a nitro-
gen filled dry-box. When the TOP capped CdSe colloidal dispersion was
prepared and cooled to -3OO"C, the Zn/S/TOP solution was injected into
CdSe colloidal dispersion five times at approximately 20
s
intervals.
A
total molar ratio of injected reagents CdfSe
:
ZnfS was
1
:
4. Upon cool-
ing the reaction mixture was stirred at 100°C for
1
h.
A
layer of ZnS of