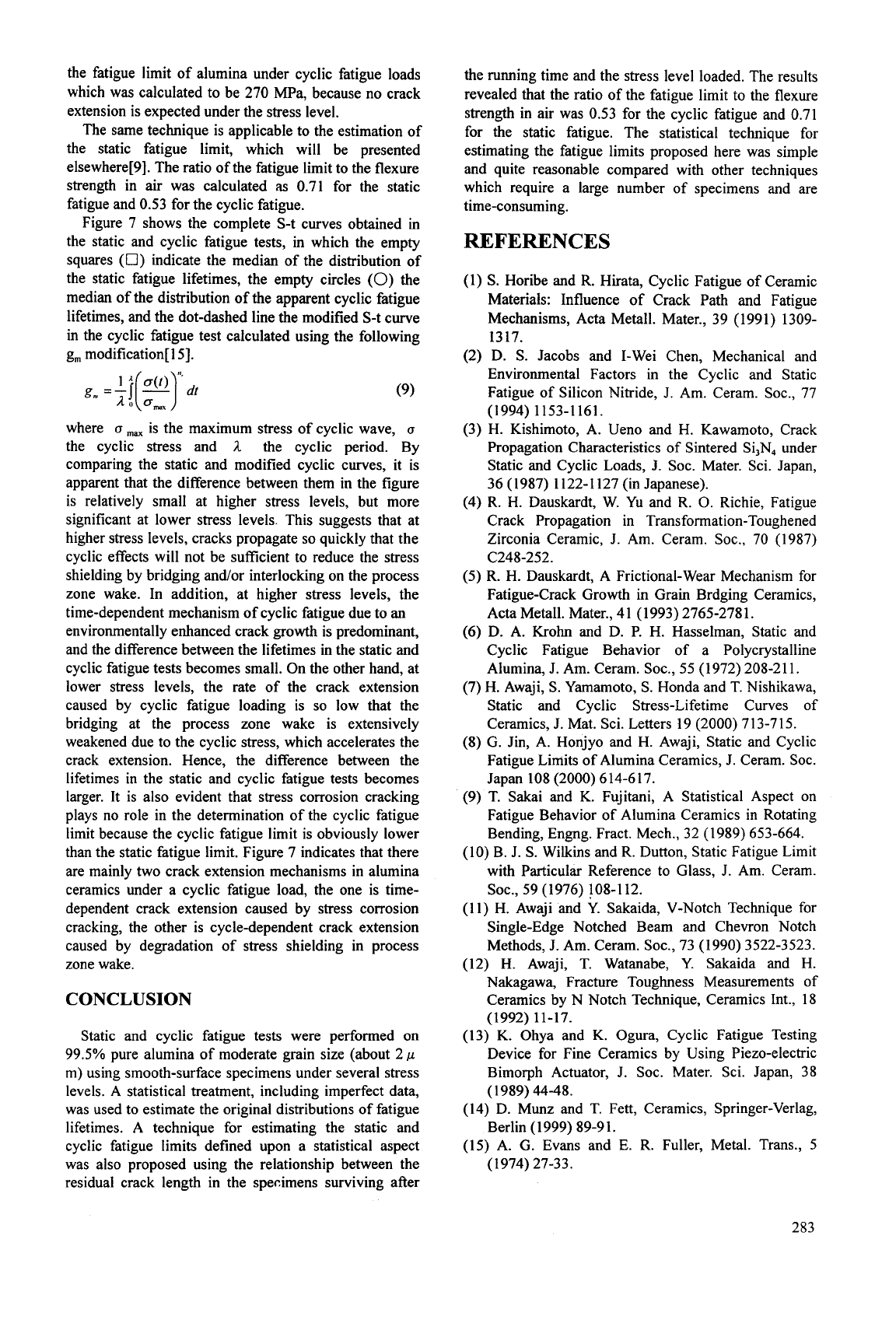
the fatigue limit of alumina under cyclic fatigue loads
which was calculated to be
270
MPa, because no crack
extension is expected under the stress level.
The same technique is applicable to the estimation of
the static fatigue limit, which will be presented
elsewhere[9]. The ratio of the fatigue limit to the flexure
strength in air was calculated
as
0.71 for the static
fatigue and 0.53 for the cyclic fatigue.
Figure 7 shows the complete S-t curves obtained in
the static and cyclic fatigue tests, in which the empty
squares
(0)
indicate the median of the distribution of
the static fatigue lifetimes, the empty circles
(0)
the
median of the distribution of the apparent cyclic fatigue
lifetimes, and the dot-dashed line the modified S-t curve
in the cyclic fatigue test calculated using the following
g, modification[ 151.
(9)
where
u
max
is the maximum stress of cyclic wave,
u
the cyclic stress and
;1
the cyclic period. By
comparing the static and modified cyclic curves, it is
apparent that the difference between them in the figure
is relatively small at higher stress levels, but more
significant at lower stress levels. This suggests that at
higher stress levels, cracks propagate
so
quickly that the
cyclic effects will not be sufficient to reduce the stress
shielding by bridging and/or interlocking on the process
zone wake. In addition, at higher stress levels, the
time-dependent mechanism of cyclic fatigue due to an
environmentally enhanced crack growth is predominant,
and the difference between the lifetimes in the static and
cyclic fatigue tests becomes small. On the other hand, at
lower stress levels, the rate of the crack extension
caused by cyclic fatigue loading is
so
low that the
bridging at the process zone wake is extensively
weakened due to the cyclic stress, which accelerates the
crack extension. Hence, the difference between the
lifetimes in the static and cyclic fatigue tests becomes
larger. It is also evident that stress corrosion cracking
plays no role in the determination of the cyclic fatigue
limit because the cyclic fatigue limit is obviously lower
than the static fatigue limit. Figure 7 indicates that there
are mainly two crack extension mechanisms in alumina
ceramics under a cyclic fatigue load, the one is time-
dependent crack extension caused by stress corrosion
cracking, the other is cycle-dependent crack extension
caused by degradation of stress shielding in process
zone wake.
CONCLUSION
Static and cyclic fatigue tests were performed on
99.5% pure alumina of moderate grain size (about 2
p
m)
using smooth-surface specimens under several stress
levels.
A
statistical treatment, including imperfect data,
was used to estimate the original distributions of fatigue
lifetimes.
A
technique for estimating the static and
cyclic fatigue limits defined upon a statistical aspect
was also proposed using the relationship between the
residual crack length in the specimens surviving after
the running time and the stress level loaded. The results
revealed that the ratio of the fatigue limit to the flexure
strength in air was 0.53 for the cyclic fatigue and 0.71
for the static fatigue. The statistical technique for
estimating the fatigue limits proposed here was simple
and quite reasonable compared with other techniques
which require a large number of specimens and are
time-consuming.
REFERENCES
(1)
S.
Horibe and R. Hirata, Cyclic Fatigue of Ceramic
Materials: Influence of Crack Path and Fatigue
Mechanisms, Acta Metall. Mater., 39 (1991) 1309-
1317.
(2) D.
S.
Jacobs and Lwei Chen, Mechanical and
Environmental Factors in the Cyclic and Static
Fatigue of Silicon Nitride,
J.
Am. Ceram. SOC., 77
(3) H. Kishimoto, A. Ueno and H. Kawamoto, Crack
Propagation Characteristics of Sintered Si,N, under
Static and Cyclic Loads, 3. SOC. Mater. Sci. Japan,
36 (1987) 1122-1127 (in Japanese).
(4) R. H. Dauskardt, W. Yu and R.
0.
Richie, Fatigue
Crack Propagation in Transformation-Toughened
Zirconia Ceramic, J. Am. Ceram. SOC., 70 (1987)
(5)
R.
H. Dauskardt, A Frictional-Wear Mechanism for
Fatigue-Crack Growth in Grain Brdging Ceramics,
Acta Metall. Mater., 4 1
(1
993) 2765-278 1.
(6)
D. A. Krohn and D. P.
H.
Hasselman, Static and
Cyclic Fatigue Behavior of a Polycrystalline
Alumina, J. Am. Ceram. SOC.,
55
(1972) 208-211.
(7)
H.
Awaji,
S.
Yamamoto,
S.
Honda and T. Nishikawa,
Static and Cyclic Stress-Lifetime Curves
of
Ceramics,
J.
Mat. Sci. Letters 19 (2000) 713-715.
(8)
G.
Jin, A. Honjyo and H. Awaji, Static and Cyclic
Fatigue Limits of Alumina Ceramics, J. Ceram. SOC.
Japan 108 (2000) 614-617.
(9) T. Sakai and K. Fujitani,
A
Statistical Aspect on
Fatigue Behavior of Alumina Ceramics in Rotating
Bending, Engng. Fract. Mech., 32 (1989) 653-664.
(10) B. J.
S.
Wilkins and
R.
Dutton, Static Fatigue Limit
with Particular Reference to Glass, J. Am. Ceram.
(1
1)
H.
Awaji and Y. Sakaida, V-Notch Technique for
Single-Edge Notched Beam and Chevron Notch
Methods, J. Am. Ceram. SOC., 73 (1990) 3522-3523.
(12)
H.
Awaji, T. Watanabe,
Y.
Sakaida and
H.
Nakagawa, Fracture Toughness Measurements
of
Ceramics by N Notch Technique, Ceramics Int., 18
(13)
K.
Ohya and K. Ogura, Cyclic Fatigue Testing
Device for Fine Ceramics by Using Piezo-electric
Bimorph Actuator, J. SOC. Mater. Sci. Japan, 38
(14) D. Munz and T. Fett, Ceramics, Springer-Verlag,
(15)
A. G. Evans and E. R. Fuller, Metal. Trans.,
5
(
1
994) 1
1
53-
1
1 6
1
.
C248-252.
SOC., 59 (1976) 108-112.
(1992) 11-17.
(1989) 44-48.
Berlin
(1
999) 89-9
1.
(1974) 27-33.
283