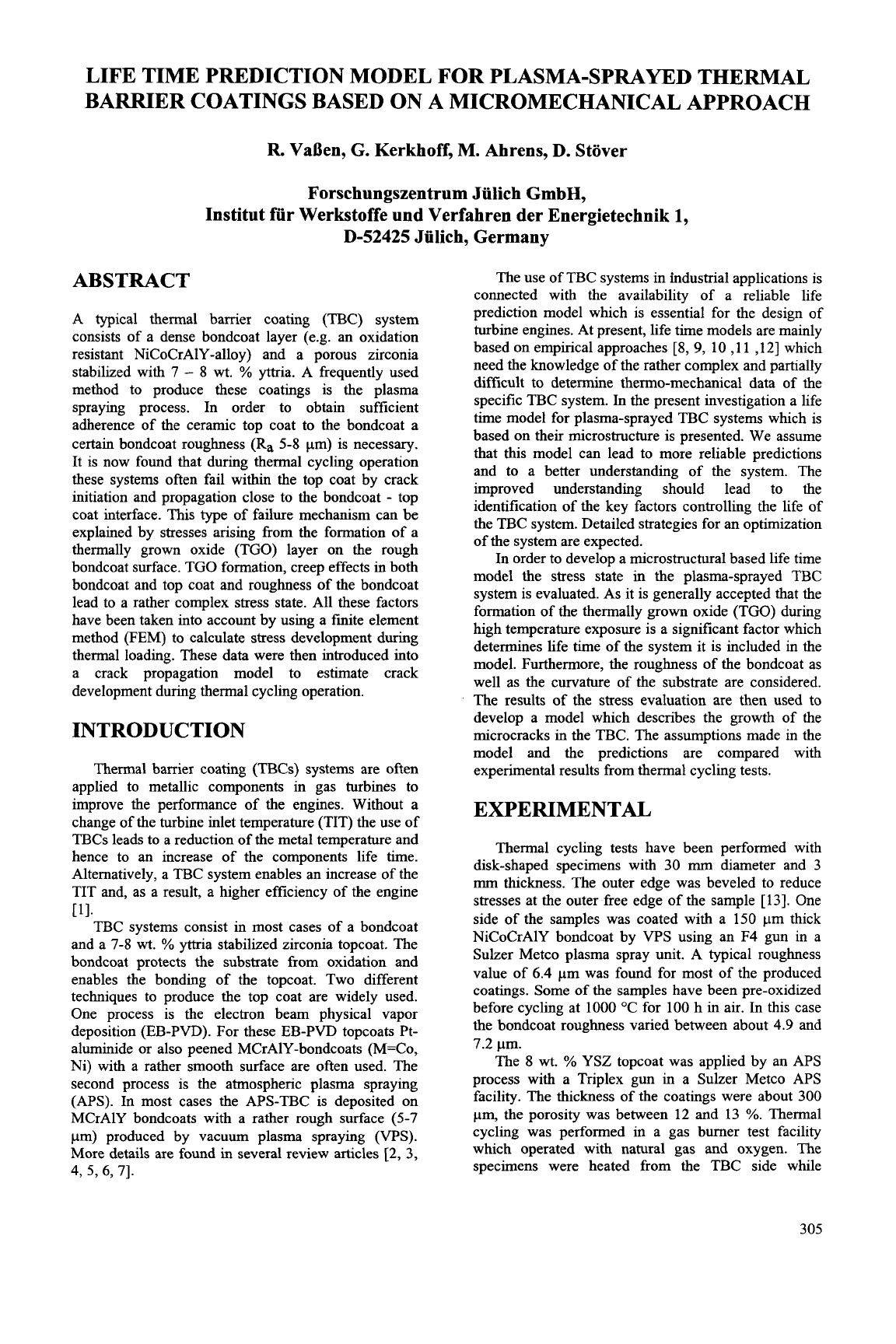
LIFE TIME PREDICTION MODEL FOR PLASMA-SPRAYED THERMAL
BARRIER COATINGS BASED ON A MICROMECHANICAL APPROACH
R
VaSen, G. Kerkhoff,
M.
Ahrens,
D.
Stover
Forschungszentrum Julich GmbH,
Institut fur Werkstoffe und Verfahren der Energietechnik
1,
D-52425
Jiilich, Germany
ABSTRACT
A typical thermal barrier coating (TBC) system
consists of a dense bondcoat layer (e.g. an oxidation
resistant NiCoCrAIY-alloy) and a porous zirconia
stabilized with 7
-
8
wt.
%
ma. A frequently used
method to produce these coatings is the plasma
spraying process. In order to obtain sufficient
adherence of the ceramic top coat to the bondcoat a
certain bondcoat roughness (Ra 5-8 pm) is necessary.
It is now found that during thermal cycling operation
these systems often fail within the top coat by crack
initiation and propagation close to the bondcoat
-
top
coat interface. This type of failure mechanism can be
explained by stresses arising from the formation of a
thermally grown oxide (TGO) layer on the rough
bondcoat surface. TGO formation, creep effects in both
bondcoat and top coat and roughness
of
the bondcoat
lead to a rather complex stress state. All these factors
have been taken into account by using a finite element
method (FEM) to calculate stress development during
thermal loading. These data were then introduced into
a crack propagation model to estimate crack
development during thermal cycling operation.
INTRODUCTION
Thermal barrier coating (Tl3Cs) systems are often
applied
to
metallic components in gas turbines to
improve the performance of the engines. Without a
change of the turbine inlet temperature (TIT) the use of
TBCs leads to a reduction
of
the metal temperature and
hence to an increase of the components life time.
Alternatively, a TBC system enables an increase of the
TIT and, as a result, a higher efficiency of the engine
TBC systems consist in most cases of a bondcoat
and a 7-8
wt.
%
yttria stabilized zirconia topcoat. The
bondcoat protects the substrate from oxidation and
enables the bonding of the topcoat. Two different
techniques to produce the top coat are widely used.
One process is the electron beam physical vapor
deposition (EB-PVD). For these EB-PVD topcoats Pt-
aluminide or also peened MCrAlY-bondcoats (M=Co,
Ni) with a rather smooth surface are often used. The
second process is the atmospheric plasma spraying
(APS). In most cases the APS-TBC is deposited on
MCrAlY bondcoats with a rather rough surface
(5-7
pm) produced by vacuum plasma spraying
(VPS).
More details are found in several review articles
[2,
3,
4, 5,671.
PI.
The use of TBC systems in industrial applications is
connected with the availability of a reliable life
prediction model which is essential for the design of
turbine engines. At present, life time models are mainly
based on empirical approaches
[8,
9, 10 ,11 ,121 which
need the knowledge of the rather complex and partially
difficult to determine thermo-mechanical data of the
specific TBC system. In the present investigation a life
time model for plasma-sprayed TBC systems which is
based on their microstructure is presented. We assume
that this model can lead to more reliable predictions
and to a better understanding
of
the system. The
improved understanding should lead to the
identification
of
the key factors controlling the life of
the TBC system. Detailed strategies for an optimization
of the system are expected.
In order to develop a microstructural based life time
model the stress state in the plasma-sprayed TBC
system is evaluated. As it is generally accepted that the
formation of the thermally grown oxide (TGO) during
high temperature exposure is a significant factor which
determines life time of the system it
is
included in the
model. Furthermore, the roughness of the bondcoat as
well as the curvature of the substrate are considered.
The results of the stress evaluation are then used to
develop a model which describes the growth of the
microcracks in the TBC. The assumptions made in the
model and the predictions are compared with
experimental results from thermal cycling tests.
EXPERIMENTAL
Thermal cycling tests have been performed with
disk-shaped specimens with 30
mm
diameter and 3
mm
hckness. The outer edge was beveled to reduce
stresses at the outer free edge of the sample [13]. One
side of the samples was coated with a 150 pm thick
NiCoCrAlY bondcoat by VPS using an F4 gun in a
Sulzer Metco plasma spray unit. A typical roughness
value of
6.4
pm was found for most of the produced
coatings. Some of the samples have been pre-oxidized
before cycling at
1000
"C for 100 h in air. In this case
the bondcoat roughness varied between about 4.9 and
7.2
pm.
The
8
wt.
%
YSZ topcoat was applied by an APS
process with a Triplex gun in a Sulzer Metco APS
facility. The thickness of the coatings were about 300
pm, the porosity was between 12 and 13
%.
Thermal
cycling was performed in a gas burner test facility
which operated with natural gas and oxygen. The
specimens were heated from the TBC side while
305