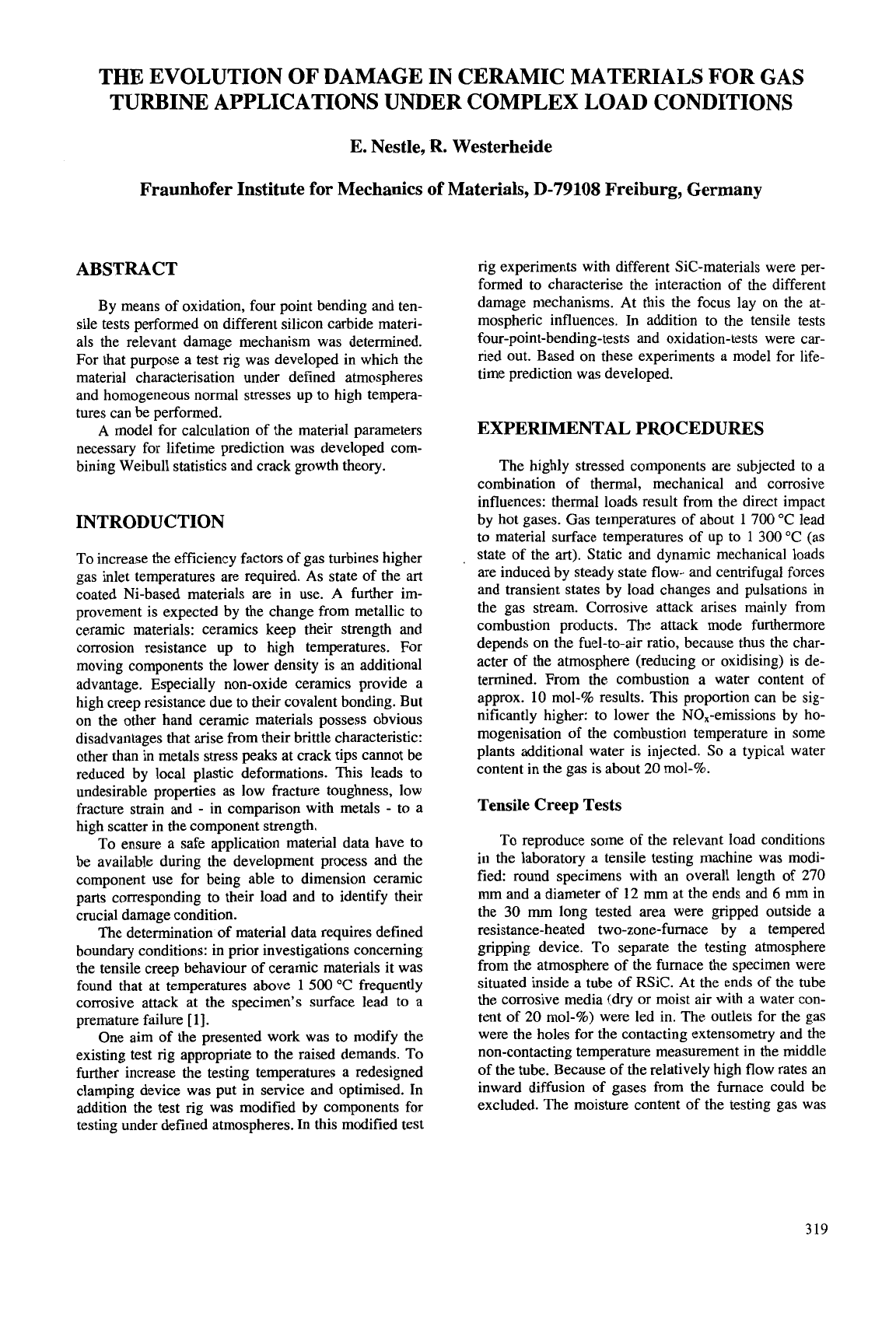
THE EVOLUTION OF DAMAGE IN CERAMIC MATERIALS FOR GAS
TURBINE APPLICATIONS UNDER COMPLEX LOAD CONDITIONS
E. Nestle, R. Westerheide
Fraunhofer Institute for Mechanics of Materials, D-79108 Freiburg, Germany
ABSTRACT
By means of oxidation, four point bending and ten-
sile tests performed on different silicon carbide materi-
als the relevant damage mechanism was determined.
For that purpose a test rig was developed in which the
material characterisation under defined atmospheres
and homogeneous normal stresses up to high tempera-
tures can be performed.
A model for calculation of the material parameters
necessary for lifetime prediction was developed com-
bining Weibull statistics and crack growth theory.
INTRODUCTION
To
increase the efficiency factors of gas turbines higher
gas inlet temperatures are required. As state of the art
coated Ni-based materials are in use.
A
further im-
provement is expected by the change from metallic to
ceramic materials: ceramics keep their strength and
corrosion resistance up to high temperatures. For
moving components the lower density is an additional
advantage. Especially non-oxide ceramics provide a
high creep resistance due to their covalent bonding. But
on the other hand ceramic materials possess obvious
disadvantages that arise from their brittle characteristic:
other than in metals stress peaks at crack tips cannot be
reduced by local plastic deformations. This leads to
undesirable properties as low fracture toughness, low
fracture strain and
-
in comparison with metals
-
to a
high scatter in the component strength.
To ensure a safe application material data have to
be available during the development process and the
component use for being able to dimension ceramic
parts corresponding to their load and to identify their
crucial damage condition.
The determination of material data requires defined
boundary conditions: in prior investigations concerning
the tensile creep behaviour
of ceramic materials it was
found that at temperatures above
1
500
"C frequently
corrosive attack at the specimen's surface lead to
a
premature failure
[I].
One aim of the presented work was to modify the
existing test rig appropriate
to
the raised demands.
To
further increase the testing temperatures a redesigned
clamping device was put in service and optimised. In
addition the test rig was modified by components for
testing under defined atmospheres. In this modified test
rig experiments with different Sic-materials were per-
formed to characterise the interaction of the different
damage mechanisms. At this the focus lay on the at-
mospheric influences. In addition to the tensile tests
four-point-bending-tests and oxidation-tests were car-
ried out. Based on these experiments a model for life-
time prediction was developed.
EXPERIMENTAL PROCEDURES
The highly stressed components are subjected to a
combination
of
thermal, mechanical and corrosive
influences: thermal loads result from the direct impact
by hot gases. Gas temperatures of about
1
700
"C lead
to material surface temperatures of up to
1
300
"C (as
state of the
art).
Static and dynamic mechanical loads
are induced by steady state flow- and centrifugal forces
and transient states by load changes and pulsations
in
the gas stream. Corrosive attack arises mainly from
combustion products. The attack mode furthermore
depends on the fuel-to-air ratio, because thus the char-
acter of the atmosphere (reducing or oxidising) is de-
termined. From the combustion a water content of
approx.
10
mol-% results. This proportion can be sig-
nificantly higher: to lower the NO,-emissions by ho-
mogenisation of the combustion temperature in some
plants additional water is injected.
So
a typical water
content in the gas is about
20
mol-%.
Tensile
Creep
Tests
To
reproduce some of the relevant load conditions
in the laboratory a tensile testing machine was modi-
fied: round specimens with an overall length of
270
mm and a diameter of
12
mm at the ends and
6
mm in
the
30
mm
long tested area were gripped outside a
resistance-heated two-zone-furnace by a tempered
gripping device.
To
separate the testing atmosphere
from the atmosphere of the furnace the specimen were
situated inside a tube of RSiC. At the ends of the tube
the corrosive media (dry or moist air with a water con-
tent of
20
mol-%) were led in. The outlets for the gas
were the holes for the contacting extensometry and the
non-contacting temperature measurement in the middle
of the tube. Because of the relatively high flow rates an
inward diffusion of gases from the furnace could be
excluded. The moisture content of the testing gas was
319