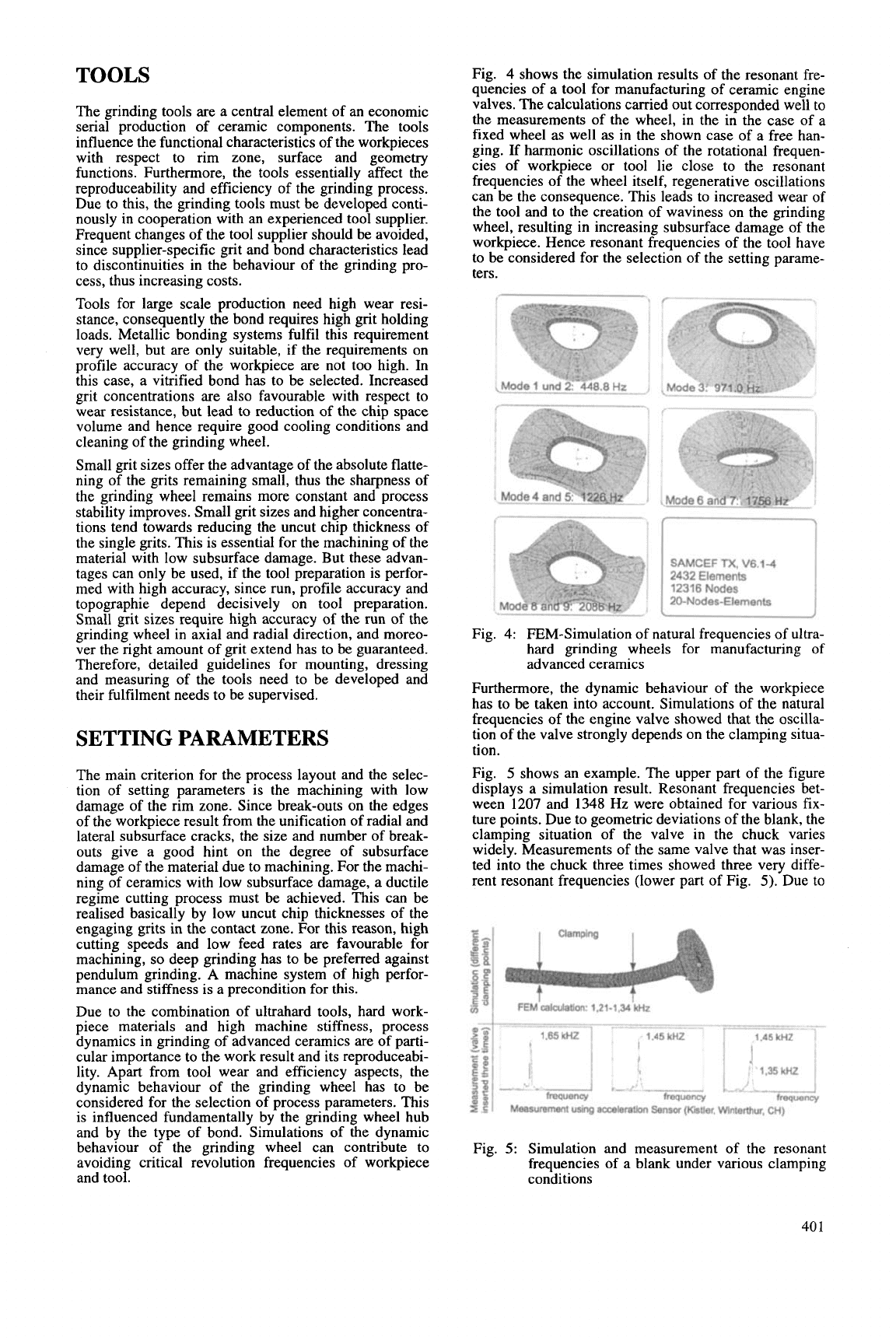
TOOLS
The grinding tools are a central element of an economic
serial production of ceramic components. The tools
influence the functional characteristics of the workpieces
with respect to rim zone, surface and geometry
functions. Furthermore, the tools essentially affect the
reproduceability and efficiency of the grinding process.
Due to this, the grinding tools must be developed conti-
nously
in
cooperation with an experienced tool supplier.
Frequent changes of the tool supplier should be avoided,
since supplier-specific grit and bond characteristics lead
to discontinuities in the behaviour of the grinding pro-
cess, thus increasing costs.
Tools for large scale production need high wear resi-
stance, consequently the bond requires high grit holding
loads. Metallic bonding systems fulfil this requirement
very well, but are only suitable, if the requirements on
profile accuracy of the workpiece are not too high. In
this case, a vitrified bond has to be selected. Increased
grit concentrations are also favourable with respect to
wear resistance, but lead to reduction of the chip space
volume and hence require good cooling conditions and
cleaning of the grinding wheel.
Small grit sizes offer the advantage of the absolute flatte-
ning of the grits remaining small, thus the sharpness of
the grinding wheel remains more constant and process
stability improves. Small grit sizes and higher concentra-
tions tend towards reducing the uncut chip thickness of
the single grits. This is essential for the machining of the
material with low subsurface damage. But these advan-
tages can only be used, if the tool preparation is perfor-
med with high accuracy, since run, profile accuracy and
topographie depend decisively on tool preparation.
Small grit sizes require high accuracy of the run of the
grinding wheel
in
axial and radial direction, and moreo-
ver the right amount of grit extend has to be guaranteed.
Therefore, detailed guidelines for mounting, dressing
and measuring of the tools need to be developed and
their fulfilment needs to be supervised.
SETTING PARAMETERS
The main criterion for the process layout and the selec-
tion of setting parameters is the machining with low
damage of the rim zone. Since break-outs on the edges
of the workpiece result from the unification of radial and
lateral subsurface cracks, the size and number of break-
outs give a good hint on the degree of subsurface
damage of the material due to machining. For the machi-
ning of ceramics with low subsurface damage, a ductile
regime cutting process must be achieved. This can be
realised basically by low uncut chip thicknesses of the
engaging grits in the contact zone. For this reason, high
cutting speeds and low feed rates are favourable for
machining,
so
deep grinding has to be preferred against
pendulum grinding. A machine system of high perfor-
mance and stiffness is a precondition
for
this.
Due
to
the combination of ultrahard tools, hard work-
piece materials and high machine stiffness, process
dynamics in grinding of advanced ceramics are
of
parti-
cular importance to the work result and its reproduceabi-
lity. Apart from tool wear and efficiency aspects, the
dynamic behaviour of the grinding wheel has to be
considered for the selection of process parameters. This
is influenced fundamentally by the grinding wheel hub
and by the type of bond. Simulations of the dynamic
behaviour of the grinding wheel can contribute to
avoiding critical revolution frequencies of workpiece
and tool.
Fig.
4
shows the simulation results of the resonant fre-
quencies of a tool for manufacturing of ceramic engine
valves. The calculations carried out corresponded well to
the measurements of the wheel, in the in the case of a
fixed wheel as well
as
in
the shown case of a free han-
ging. If harmonic oscillations of the rotational frequen-
cies of workpiece
or
tool lie close to the resonant
frequencies of the wheel itself, regenerative oscillations
can be the consequence. This leads to increased wear of
the tool and to the creation of waviness on the grinding
wheel, resulting in increasing subsurface damage of the
workpiece. Hence resonant frequencies of the tool have
to be considered for the selection of the setting parame-
ters.
Fig.
4:
FEM-Simulation
of
natural frequencies of ultra-
hard grinding wheels for manufacturing of
advanced ceramics
Furthermore, the dynamic behaviour of the workpiece
has to be taken into account. Simulations of the natural
frequencies of the engine valve showed that the oscilla-
tion of the valve strongly depends on the clamping situa-
tion.
Fig.
5
shows an example. The upper part of the figure
displays a simulation result. Resonant frequencies bet-
ween
1207
and
1348
Hz were obtained for various fix-
ture points. Due to geometric deviations of the blank, the
clamping situation of the valve in the chuck varies
widely. Measurements of the same valve that was inser-
ted into the chuck three times showed three very diffe-
rent resonant frequencies (lower part of Fig.
5).
Due to
Fig.
5:
Simulation and measurement of the resonant
frequencies of a blank under various clamping
conditions
40
1