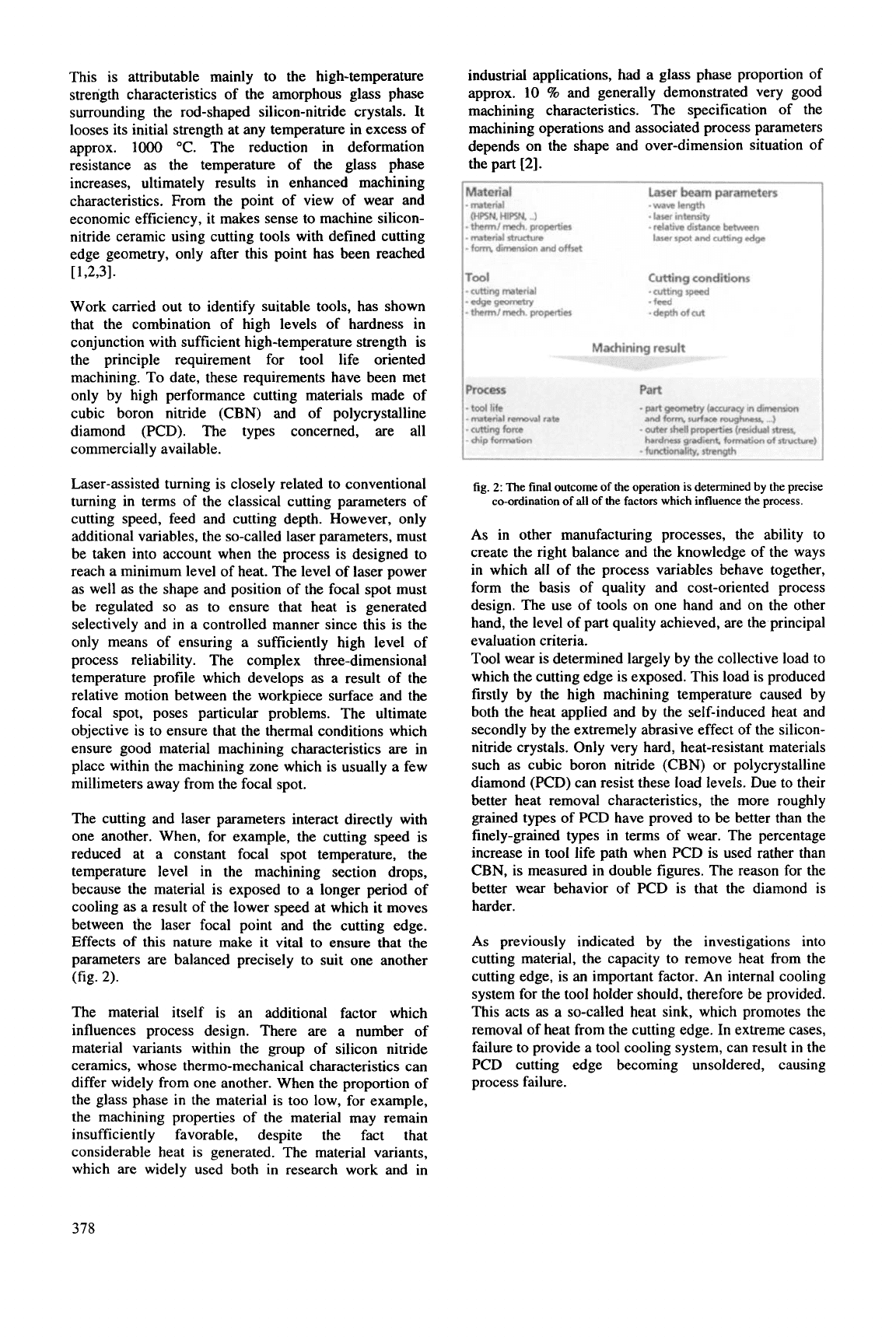
This is attributable mainly to the high-temperature
strength characteristics of the amorphous glass phase
surrounding the rod-shaped silicon-nitride crystals. It
looses its initial strength at any temperature in excess of
approx.
lo00
"C. The reduction in deformation
resistance
as
the temperature of the glass phase
increases, ultimately results in enhanced machining
characteristics. From the point of view of wear and
economic efficiency, it makes sense to machine silicon-
nitride ceramic using cutting tools with defined cutting
edge geometry, only after this point has been reached
[1,2,31.
Work carried out to identify suitable tools, has shown
that the combination of high levels of hardness in
conjunction with sufficient high-temperature strength is
the principle requirement for tool life oriented
machining. To date, these requirements have been met
only by high performance cutting materials made of
cubic boron nitride (CBN) and of polycrystalline
diamond (PCD). The types concerned, are all
commercially available.
Laser-assisted turning is closely related to conventional
turning in terms of the classical cutting parameters of
cutting speed, feed and cutting depth. However, only
additional variables, the so-called laser parameters, must
be taken into account when the process is designed to
reach a minimum level of heat. The level of laser power
as well as the shape and position of the focal spot must
be regulated
so
as to ensure that heat is generated
selectively and in a controlled manner since this is the
only means of ensuring a sufficiently high level of
process reliability. The complex three-dimensional
temperature profile which develops
as
a result of the
relative motion between the workpiece surface and the
focal spot, poses particular problems. The ultimate
objective
is
to ensure that the thermal conditions which
ensure good material machining characteristics are in
place within the machining zone which is usually a few
millimeters away from the focal spot.
The cutting and laser parameters interact directly with
one another. When, for example, the cutting speed is
reduced at a constant focal spot temperature, the
temperature level
in
the machining section drops,
because the material is exposed to a longer period of
cooling as a result of the lower speed at which it moves
between the laser focal point and the cutting edge.
Effects of this nature make it vital to ensure that the
parameters are balanced precisely to suit one another
(fig.
2).
The material itself is an additional factor which
influences process design. There are a number of
material variants within the group of silicon nitride
ceramics, whose thermo-mechanical characteristics can
differ widely from one another. When the proportion of
the glass phase in the material is too low, for example,
the machining properties of the material may remain
insufficiently favorable, despite the fact that
considerable heat is generated. The material variants,
which are widely used both in research work and in
industrial applications, had a glass phase proportion of
approx. 10
96
and generally demonstrated very good
machining characteristics. The specification of the
machining operations and associated process parameters
depends on the shape and over-dimension situation of
the part [2].
fig.
2:
The final outcome of the operation
is
determined
by
the precise
co-ordination of
all
of the factors which influence the process.
As in other manufacturing processes, the ability to
create the right balance and the knowledge of the ways
in which all of the process variables behave together,
form the basis of quality and cost-oriented process
design. The use of tools on one hand and on the other
hand, the level of part quality achieved, are the principal
evaluation criteria.
Tool wear is determined largely by the collective load to
which the cutting edge is exposed. This load is produced
firstly by the high machining temperature caused by
both the heat applied and by the self-induced heat and
secondly by the extremely abrasive effect of the silicon-
nitride crystals. Only very hard, heat-resistant materials
such as cubic boron nitride (CBN)
or
polycrystalline
diamond (PCD) can resist these load levels. Due to their
better heat removal characteristics, the more roughly
grained types of PCD have proved to be better than the
finely-grained types in terms of wear. The percentage
increase in tool life path when PCD is used rather than
CBN, is measured in double figures. The reason for the
better wear behavior of PCD is that the diamond is
harder.
As
previously indicated by the investigations into
cutting material, the capacity to remove heat from the
cutting edge, is an important factor. An internal cooling
system for the tool holder should, therefore be provided.
This acts as a so-called heat sink, which promotes the
removal of heat from the cutting edge. In extreme cases,
failure to provide a tool cooling system, can result
in
the
PCD cutting edge becoming unsoldered, causing
process failure.
378