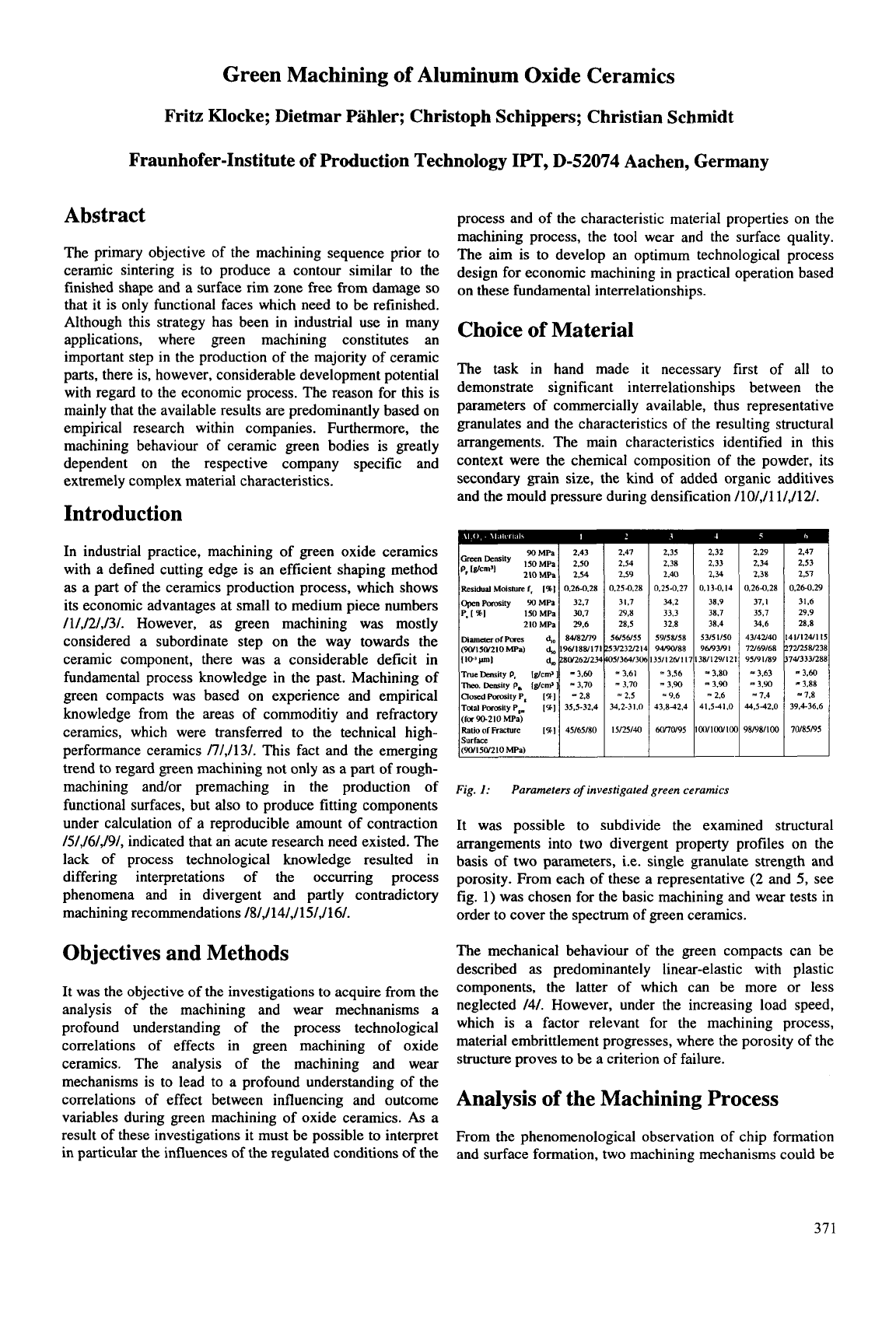
Green Machining
of
Aluminum Oxide Ceramics
Fritz Klocke; Dietmar Pahler; Christoph Schippers; Christian Schmidt
Fraunhofer-Institute of Production Technology IPT,
D-52074
Aachen, Germany
Residual Moislure
f,
[%I
0.260.28
open
porosity
WMPa 32.7
p.
151
150MPa 30.7
210MPa 29.6
Dimanofks
d,,
84/82/79
(901150/210MF%)
4.
11O’Wunl
d,
28Cb‘262/234405/364/3G+
TrueDensity
P,
[@cM]
-3.60
Theo.
Densuy
P.
IglcM
1
-
3.70
Closed
porosity
P,
[a]
=
2.8
~aal
Pwosityp,
[a]
35.5-32.4
(fa
90-210
MPa)
Ratio
of
FracNre
ICI
45/65/80
Abstract
2.47
2.54
2.59
0.254.28
31.7
29.8
28.5
56/56/55
196/188/171253/232/214
I
=3,6l
=
3,70
=
2.5
34.2-31.0
15/25/40
The primary objective of the machining sequence prior to
ceramic sintering is to produce a contour similar to the
finished shape and a surface rim zone
free
from damage
so
that
it
is only functional faces which need to be refinished.
Although this strategy has been in industrial use
in
many
applications, where green machining constitutes an
important step
in
the production of the majority of ceramic
parts, there is, however, considerable development potential
with regard to the economic process. The reason for this is
mainly that the available results are predominantly based on
empirical research within companies. Furthermore, the
machining behaviour of ceramic green bodies is greatly
dependent on the respective company specific and
extremely complex material characteristics.
Introduction
process and of the characteristic material properties on the
machining process, the tool wear and the surface quality.
The aim is to develop an optimum technological process
design for economic machining in practical operation based
on these fundamental interrelationships.
Choice
of
Material
The
task
in hand made
it
necessary first of all to
demonstrate significant interrelationships between the
parameters of commercially available, thus representative
granulates and the characteristics of the resulting structural
arrangements. The main characteristics identified in this
context were the chemical composition of the powder, its
secondary grain size, the kind of added organic additives
and the mould pressure during densification /10/,/11/,/12/.
In industrial practice, machining of green oxide ceramics
with a defined cutting edge is an efficient shaping method
as a part of the ceramics production process, which shows
its economic advantages at small to medium piece numbers
/1/,/2/,/3/. However, as green machining was mostly
considered a subordinate step on the way towards the
ceramic component, there was a considerable deficit in
fundamental process knowledge
in
the past. Machining of
green compacts was based on experience and empirical
knowledge from the areas of commoditiy and refractory
ceramics, which were transferred to the technical high-
performance ceramics i7/,/13/. This fact and the emerging
trend to regard green machining not only
as
a part of rough-
machining and/or premaching in the production of
functional surfaces, but also to produce fitting components
under calculation of a reproducible amount
of
contraction
/5/,/6/,/9/,
indicated that an acute research need existed. The
lack of process technological knowledge resulted in
differing interpretations of the occurring process
phenomena and in divergent and partly contradictory
machining recommendations /8/,/14/,/15/,/16/.
Objectives and Methods
It was the objective of the investigations
to
acquire from the
analysis of the machining and wear mechnanisms a
profound understanding of the process technological
correlations of effects in green machining of oxide
ceramics. The analysis of the machining and wear
mechanisms is to lead to a profound understanding of the
correlations of effect between influencing and outcome
variables during green machining of oxide ceramics. As a
result of these investigations it must be possible to interpret
in particular the influences of the regulated conditions of the
2.35
2.38
2.40
0.25-0.27
34.2
33.3
32.8
59/58/58
9W88
135/126/1
I
=
3.56
=
3.90
-9.6
43,842.4
mw95
0.13-0,
I4
53/51/50
96/93/91
-
3.80
=
3.90
=
2.6
41.541.0
2.29
2.34
2.38
o,260,2n
37.1
35.7
34.6
43/42/40
72/69/68
9519 1/89
3.63
=
3.90
-
7.4
44.542.0
98/Y8/100
0.26-0.29
31.6
29.9
72/258/238
743331288
-
3.60
=
3.88
-
7.8
39,636.6
Fig.
I:
Parameters
of
investigated green ceramics
It was possible to subdivide the examined structural
arrangements into two divergent property profiles on the
basis of two parameters, i.e. single granulate strength and
porosity. From each of these a representative (2 and
5,
see
fig. 1) was chosen for the basic machining and wear tests
in
order to cover the spectrum of green ceramics.
The mechanical behaviour of the green compacts can be
described as predominantely linear-elastic with plastic
components, the latter of which can be more or less
neglected
141.
However, under the increasing load speed,
which is a factor relevant for the machining process,
material embrittlement progresses, where the porosity of the
structure proves
to
be a criterion of failure.
Analysis
of
the Machining Process
From the phenomenological observation of chip formation
and surface formation, two machining mechanisms could be
371