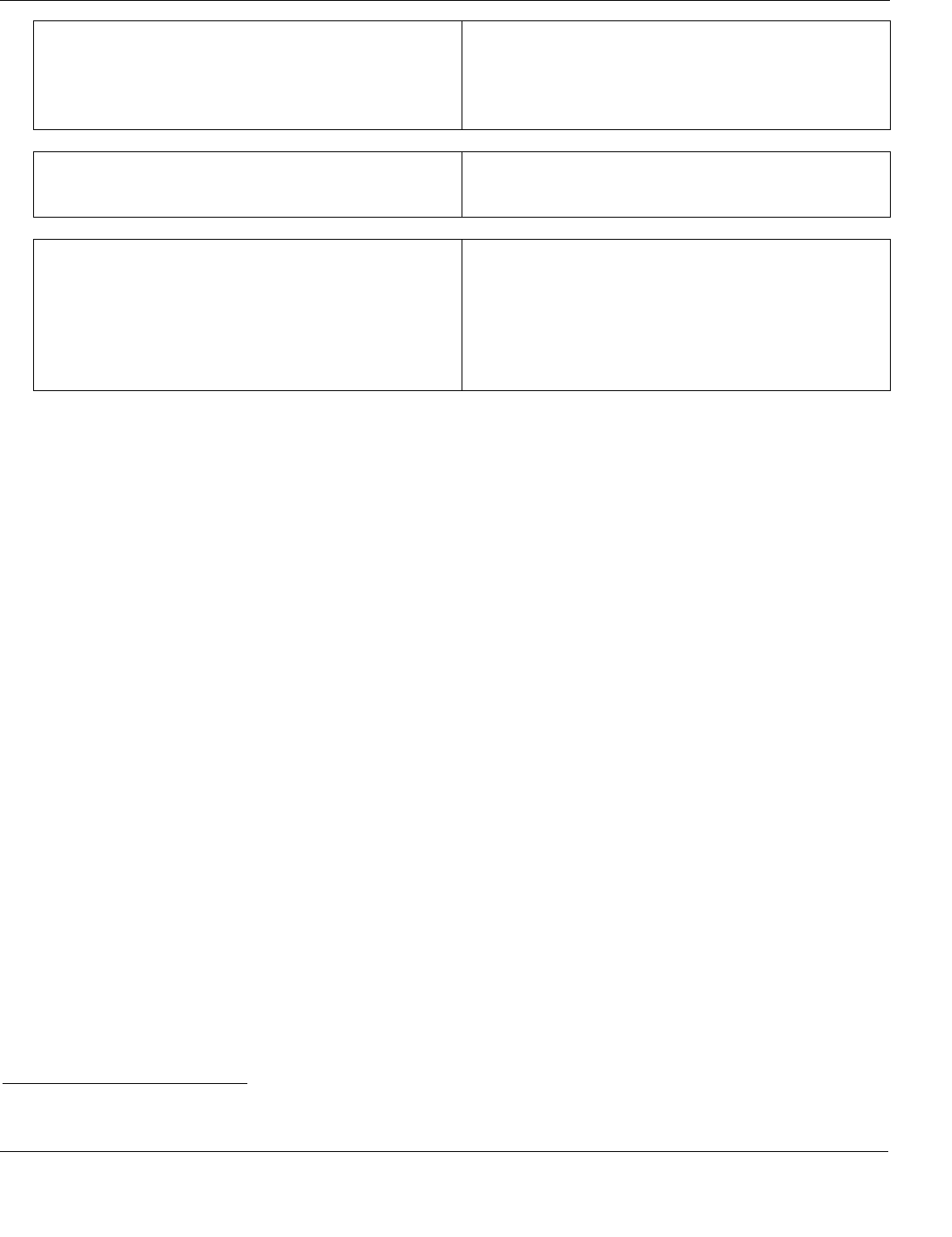
ptg6843605
lean six sigma − lean thinking
Page 195 The Encyclopedia of Operations Management
Graphical analysis (histograms, scatter plots, box
plots, etc.)
Statistical process control (x-bar charts, r-charts, c-
charts, p-charts, run charts)
Regression analysis
Design of experiments (Taguchi methods, full
factorial, factional factorial, ANOVA)
Non-parametric statistics
Microsoft Excel (for simple statistical analysis)
Minitab, SAS, or SPSS (for statistical analysis)
Voice of the customer tools
Customer satisfaction surveys
Marketing research surveys
Quality Function Deployment/House of Quality
Kano analysis
Conjoint analysis
Pugh matrix
New product development tools
Design for Six Sigma (DFSS)
Design for manufacturing (plus other DFx concepts,
such as Design for Assembly, Design for
Disassembly, Design for Environment, Design for
Reliability, etc.)
IDOV and DMADV
TRIZ
Taguchi methods
New product development organization (e.g.,
heavyweight NPD teams)
Service blueprinting
Service guarantees
Experience engineering
Designing and managing a NPD stage-gate process
Source: Professor Arthur V. Hill
See benchmarking, brainstorming, C&E Diagram, C&E Matrix, Capability Maturity Model (CMM), causal
map, champion, control chart, control plan, Critical to Quality (CTQ), cross-functional team, defect, Defects per
Million Opportunities (DPMO), Deming’s 14 points, deployment leader, Design for Six Sigma (DFSS), Design of
Experiments (DOE), DMAIC, entitlement, external setup, Failure Mode and Effects Analysis (FMEA), Gauge
R&R, human resources, impact wheel, implementation, inductive reasoning, ISO 9001:2008, just do it, Key
Process Output Variable (KPOV), lean thinking, linear regression, Metrology, PDCA (Plan-Do-Check-Act),
post-project review, process, process capability and performance, process improvement program, process map,
program management office, project charter, project hopper, Pugh Matrix, quality management, quality trilogy,
quick hit, RACI Matrix, sigma level, stage-gate process, stakeholder analysis, Statistical Process Control (SPC),
statistical quality control (SQC), strategy map, Taguchi methods, Total Quality Management (TQM),
transactional process improvement, value chain, value stream map, voice of the customer (VOC), zero defects.
lean six sigma – See lean sigma.
lean thinking – A philosophy and set of practices originally developed at Toyota that seeks to eliminate waste; also
known as lean manufacturing or just lean.
A brief history of lean – Lean concepts were first introduced at Toyota by Taiichi Ohno in Japan (Ohno
1978). Richard Schonberger played an important role in popularizing “just-in-time” (JIT) concepts in the U.S. in
the 1980s, which emphasized the material flow aspects of lean (Schonberger 1982, 1986). The term “lean” was
coined by John Krafcik
28
in the MIT International Motor Vehicles Program, but popularized in the book The
Machine That Changed the World (Womack, Jones, & Roos 1991). More recently, Jim Womack at LEI has led
a resurgence of interest in lean thinking with a view of lean that goes well beyond materials flow and
manufacturing (Womack & Jones 2003). Today, the term “lean thinking” is used to emphasize that lean is more
of a philosophy than a set of tools and that lean principles can be applied in services, government, and other non-
manufacturing contexts.
Benefits of lean – Lean thinking focuses on reducing waste though a high level of engagement of the people
in the “gemba” (the place that real work is done). Many firms that embraced lean thinking have been able to
achieve significant benefits, such as reduced cycle time, inventory, defects, waste, and cost while improving
quality and customer service and developing workers.
The basic concepts of lean – Many lean experts argue that promoters of lean sigma programs “just don’t get
it.” They argue lean sigma programs use some lean tools but miss the lean philosophy, which means they do not
truly understand lean. Clearly, lean is much more than a set of tools.
28
Interestingly, John Krafcik was named President and CEO of Hyundai North America in 2008. Under his leadership, Hyundai
increased its marketshare by 50% (source: http://www.hyundainews.com/Executive_Bios.asp, April 23, 2011).