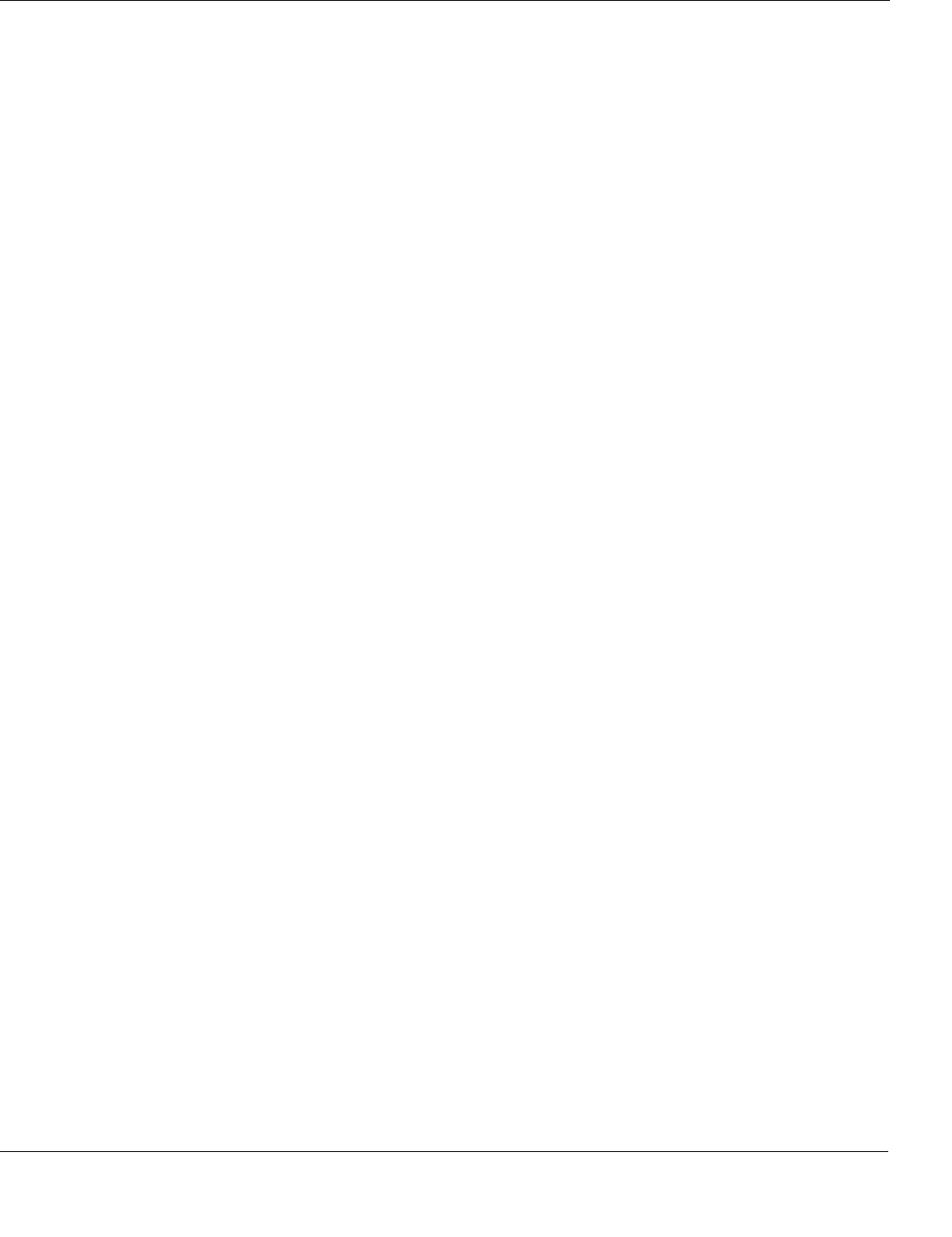
ptg6843605
learning curve − learning curve
Page 197 The Encyclopedia of Operations Management
by making the process simpler, more visible, and more error-proof. Flow is then achieved by leveling the
schedule, reducing cycle time, using a pull system, and reducing setup costs, setup times, and lotsizes (one-piece
flow is the ideal). Finally, implement changes with respect for people (the gemba), focusing on lean metrics,
such as the value added ratio, using well-executed kaizen events, and creating standardized work, all guided by a
strong program management office. The virtuous cycle is self-reinforcing because the new improvement process
will be even more visible, which makes it easier to see and eliminate waste. This figure was developed by this
author and has been validated from first-hand experience with many factory and hospital lean implementations.
Spear and Bowen’s five rules – Spear and Bowen (1999) defined five rules that capture much of the lean
philosophy at Toyota. They emphasized that lean is more of a philosophy than a set of tools. These four rules
are briefly described as follows:
Rule 1. Specifications document all work processes and include content, sequence, timing, and
outcome – Each process should be clearly specified with detailed work instructions. For example, when
workers install seats with four bolts, the bolts are inserted and tightened in a set sequence. Every worker
installs them the same way every time. While lean thinking shows respect for people and values
experimentation (using PDCA), individual workers do not change processes. Teams work together to
experiment, analyze, and change processes. Workers need problem-solving skills to their support teams in
improving standard processes over time.
Rule 2. Connections with clear yes/no signals directly link every customer and supplier – Lean uses
kanban containers (or squares) that customers use to signal the need for materials movements or production.
Rule 3. Every product and service travels through a single, simple, and direct flow path – Toyota’s U-
shaped workcells are the ultimate manifestation of this rule. This improves consistency, makes trouble
shooting easier, and simplifies material handling and scheduling.
Rule 4. Workers at the lowest feasible level, guided by a teacher (Sensei), improve their own work
processes using scientific methods – Rule 4 is closely tied with Rule 1 and engages the entire workforce in
the improvement efforts.
Rule 5. Integrated failure tests automatically signal deviations for every activity, connection, and flow
path – This is the concept of jidoka or autonomation. It prevents products with unacceptable quality from
continuing in the process. Examples include detectors for missing components, automatic gauges that check
each part, and visual alarms for low inventory. The andon light is a good example of this rule.
See 3Gs, 5S, 8 wastes, A3 Report, absorption costing, agile manufacturing, agile software development,
andon light, batch-and-queue, blocking, Capability Maturity Model (CMM), catchball, cellular manufacturing,
champion, continuous flow, cross-training, defect, demand flow, Drum-Buffer-Rope (DBR), facility layout, flow,
functional silo, gemba, heijunka, hidden factory, hoshin planning, ISO 9001:2008, jidoka, JIT II, job design,
Just-in-Time (JIT), kaizen, kaizen workshop, kanban, Keiretsu, KISS Principle, Lean Advancement Initiative
(LAI), lean design, Lean Enterprise Institute (LEI), lean promotion office, lean sigma, milk run, muda,
multiplication principle, one-piece flow, Overall Equipment Effectiveness (OEE), overhead, pacemaker, pitch,
process, process improvement program, program management office, project charter, pull system, Quick
Response Manufacturing, red tag, rework, scrum, sensei, Shingo Prize, Single Minute Exchange of Dies (SMED),
stakeholder analysis, standardized work, subtraction principle, supermarket, takt time, Theory of Constraints
(TOC), Toyota Production System (TPS), transactional process improvement, true north, two-bin system, value
added ratio, value stream, value stream manager, value stream map, visual control, waste walk, water spider,
zero inventory.
learning curve – A mathematical model that relates a performance variable (such as cost per unit) to the number of
units produced, where the performance variable decreases as the cumulative production increases, but decreases
at a slower rate; also called experience curve.
All systems can improve over time, and the rate of improvement can and should be measured. This learning
can take place at any level: the machine, individual, department, plant, business unit, and firm. Some authors
use the term “experience curve” for more complex systems, such as factories or firms; however, there is no
practical difference between the learning curve and experience curve concepts.
The performance variable is usually the cost per unit or time per unit, but could be any variable that has an
ideal point of zero. For example, other possible variables could be the defect rate (defects per million