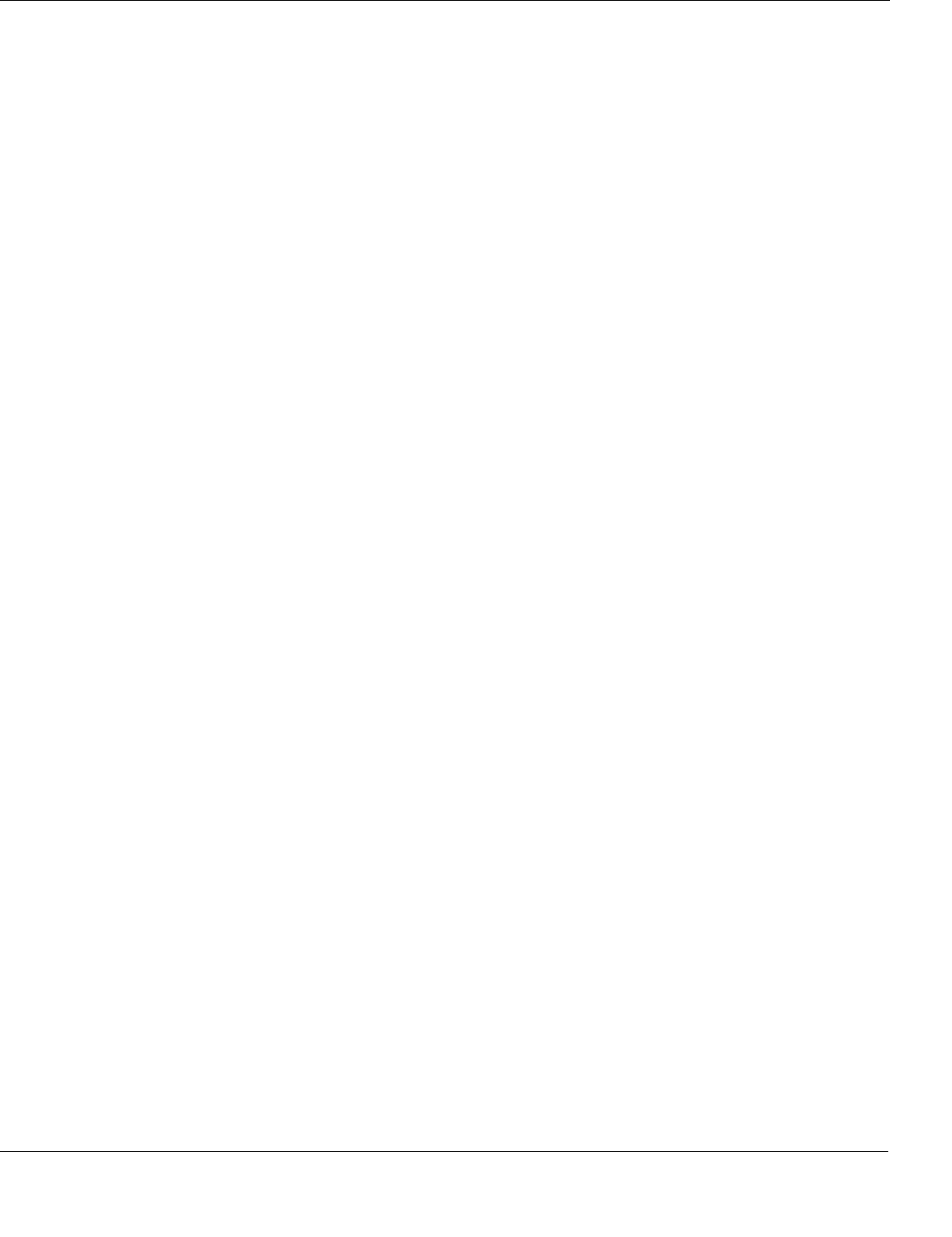
ptg6843605
in-transit inventory − inventory management
Page 173 The Encyclopedia of Operations Management
in-transit inventory – The quantity of goods shipped but not yet received.
In-transit inventory may belong to either the shipper or the customer, depending on the terms of the contract.
See inventory management, logistics.
intrinsic forecasting model – See forecasting.
Inventory Dollar Days (IDD) – A Theory of Constraints (TOC) measure of investment in inventory.
The Theory of Constraints (TOC) promotes Inventory Dollar Days (IDD) as a measure of things done
ahead of schedule and Throughput Dollar Days (TDD) as a measure of things done behind schedule. A dollar
day is one dollar held in inventory for one day. When an individual borrows money from a bank, the interest
payment is based on how many dollars are borrowed and for how long, which means that interest is based on
dollar days. When a firm is holds inventory, the cost to the firm is based on the dollar days of inventory. The
IDD can be calculated as IDD = (unit cost) x (quantity on hand) x (days in the system). For example, if a
manufacturing order for 100 units has been waiting at a workcenter for five days and the unit cost is $2, the
workcenter has 100 x 5 x 2 = $1000 dollar days for that order.
Similarly, when a firm is late, the time value of money is lost during the delay. The cost to the firm,
therefore, is based on the dollar days late. TDD measures the value of each late shipment multiplied by the
number of days it was late (i.e., a $1-million order five days late becomes five-million TDD).
Phillip Brooks, president and owner of H. Brooks and Company, a St. Paul, Minnesota distributor of fresh
fruits and vegetables, shared the following quote with the author: “We began measuring dollar days of inventory
last winter, with an item ranking and overall totals by buyer and vendor. You will find that this number will be
surprisingly large and will create an insight followed by instant action – and focus on inventory items that are
unneeded. In the last eight months, we have cut this measure by about 50%.”
The IDD for a set of items during a planning period is the sum of the unit cost for each item times the
number of days in inventory for each item. Therefore, IDD is a time-integrated sum. Any time-integrated sum
can be turned into a time-integrated average by dividing by the number of periods. Therefore, IDD divided by
the number of days in the planning period is the average inventory investment. For example, if a set of items has
an IDD of 30,000 dollar days during a 30-day month, the average inventory investment for the month is
$1000. With a monthly carrying charge of 1%, the carrying cost for these items is $10.
See
carrying cost, inventory turnover, operations performance metrics, periods supply, Theory of
Constraints (TOC), throughput accounting, Throughput Dollar Days (TDD).
inventory management – Inventory management involves planning and control of all types of inventories.
Inventory management involves forecasting demand, placing purchase and manufacturing orders, and filling
sales orders. Inventory management requires two decisions that must be made frequently: when to order, and
how much to order. A less frequent inventory management decision is deciding if an item should be stocked. If
an item is not stocked, the firm must make, assemble, or buy the item in response to customer demand.
Inventory managers may be responsible for all types of inventory:
• Raw materials/purchased components inventory – Purchased materials from outside suppliers.
• In-transit inventory – Inventory shipped, but not yet received.
• Work-in-process inventory (WIP) – Products started in manufacturing, but not yet complete.
• Manufactured components/subassemblies – Parts and subassemblies built and then stored in inventory
until needed for higher-level products or assemblies.
• Finished goods inventory – Products that are complete, but not yet shipped to a customer.
• Supplies/consumables inventory – Supplies needed for the manufacturing process, but do not become a
part of any product (e.g., cleaning supplies for a machine). These are often called Maintenance, Repair, &
Operating Supplies (MRO) items. (Note: MRO has many similar names, including “Maintenance, Repair,
and Operations” and “Maintenance, Repair, and Overhaul.”)
• Scrap inventory – Defective products that will be reworked, recycled, or scrapped.
• Consignment inventory – Products owned by one party, but held by another party until sale.
Inventory control systems must determine when to order (order timing) and how much to order (order
quantity). Order timing can be based on a reorder point (R) or a fixed schedule (every P time periods). Order
quantity can be a fixed quantity Q (possibly the EOQ) or a variable quantity based on an order-up-to level (T).
With an order-up-to (base stock) policy, the order quantity is set to T – I, where I is the inventory position.