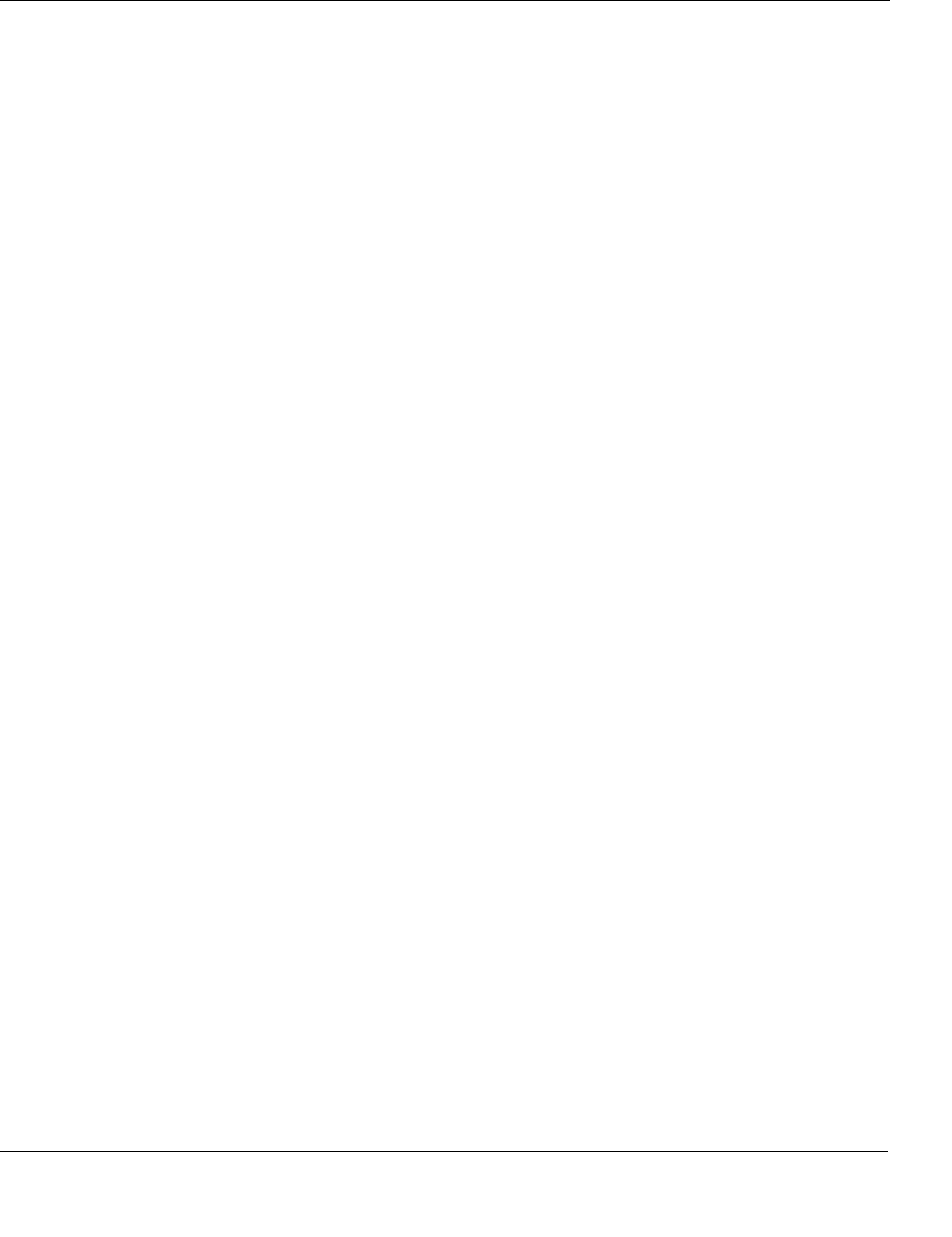
ptg6843605
procurement – product life cycle management
The Encyclopedia of Operations Management Page 274
Worst case – A set of conditions encompassing upper and lower processing limits and circumstances,
including those within standard operating procedures, which pose the greatest chance of process or product
failure when compared to ideal conditions. Such conditions do not necessarily induce product or process failure.
See Good Manufacturing Practices (GMP), process capability and performance, quality assurance,
Statistical Process Control (SPC), Statistical Quality Control (SQC).
procurement – See purchasing.
producer’s risk – The probability of rejecting a lot that should have been accepted.
The producer suffers when a lot with an acceptable quality level (AQL) is rejected. This is called a Type I
error. The Greek letter α (alpha) is used for Type I risk with typical α values in range (0.2, 0.01).
See Acceptable Quality Level (AQL), acceptance sampling, consumer’s risk, operating characteristic curve,
quality management, sampling, Type I and II errors.
Product Data Management (PDM) – The business function and associated software that creates, publishes, and
manages detailed product information.
PDM manages all information related to a product and the components that go into a product. The data
include current and historical specifications, the engineering change history (version control), the item master,
bill of material (BOM), and routing databases.
The best PDM systems are Web-based collaborative applications for product development that allow
enterprises to share business processes and product data with dispersed divisions, partners, and customers. PDM
systems hold master data in a single secure vault where data integrity can be assured and all changes are
monitored, controlled, and recorded (i.e., version control). Duplicate reference copies of the master data, on the
other hand, can be distributed freely to users in various departments for design, analysis, and approval. The new
data are then released back into the vault. When the database is changed, a modified copy of the data, signed and
dated, is stored in the vault alongside the old data.
See knowledge management, New Product Development (NPD), product life cycle management, version
control.
product design quality – The degree to which the product design meets customer requirements; also called design
quality and performance quality.
Product design quality is the output of a team of knowledge workers in marketing, product design, quality
assurance, operations, and sourcing, possibly with the help of suppliers. This design is stored and communicated
in drawings (CAD files) and specifications.
For example, the marketing and R&D people in a firm decide that a watch should be designed to survive 100
meters under water based on focus groups with customers and salesforce feedback. This design is better than a
watch designed to only survive 10 meters under water.
Although the product design standards might be high (e.g., survive 100m under water), it is possible that the
manufacturing process is flawed and that products regularly fail to meet the standard (e.g., only survive 10m
under water). In summary, product design (performance) quality is how well the design specifications meet
customer requirements, and conformance quality is how well the actual product meets the design specifications.
See conformance quality, quality management, warranty.
product family – A group of items with similar characteristics; also called family or part family.
Product families can be created from many different points of view, including selling, sales planning,
production planning, engineering, forecasting, capacity planning, financial planning, and factory layout. Product
families may meet a common set of customer requirements (e.g., a product family sold to one market segment),
may have similar manufacturing requirements (e.g., all items within a family require the same sequence of
manufacturing steps), or may have similar product technologies or components (e.g., all use digital electronics).
See bill of material (BOM), cellular manufacturing, part number, Resource Requirements Planning (RRP),
Sales & Operations Planning (S&OP), sequence-dependent setup time, setup cost, value stream.
product layout – See facility layout.
product life cycle management – Managing a product through its entire life, from concept to design,
development, commercialization, manufacturing, and finally, phase out.