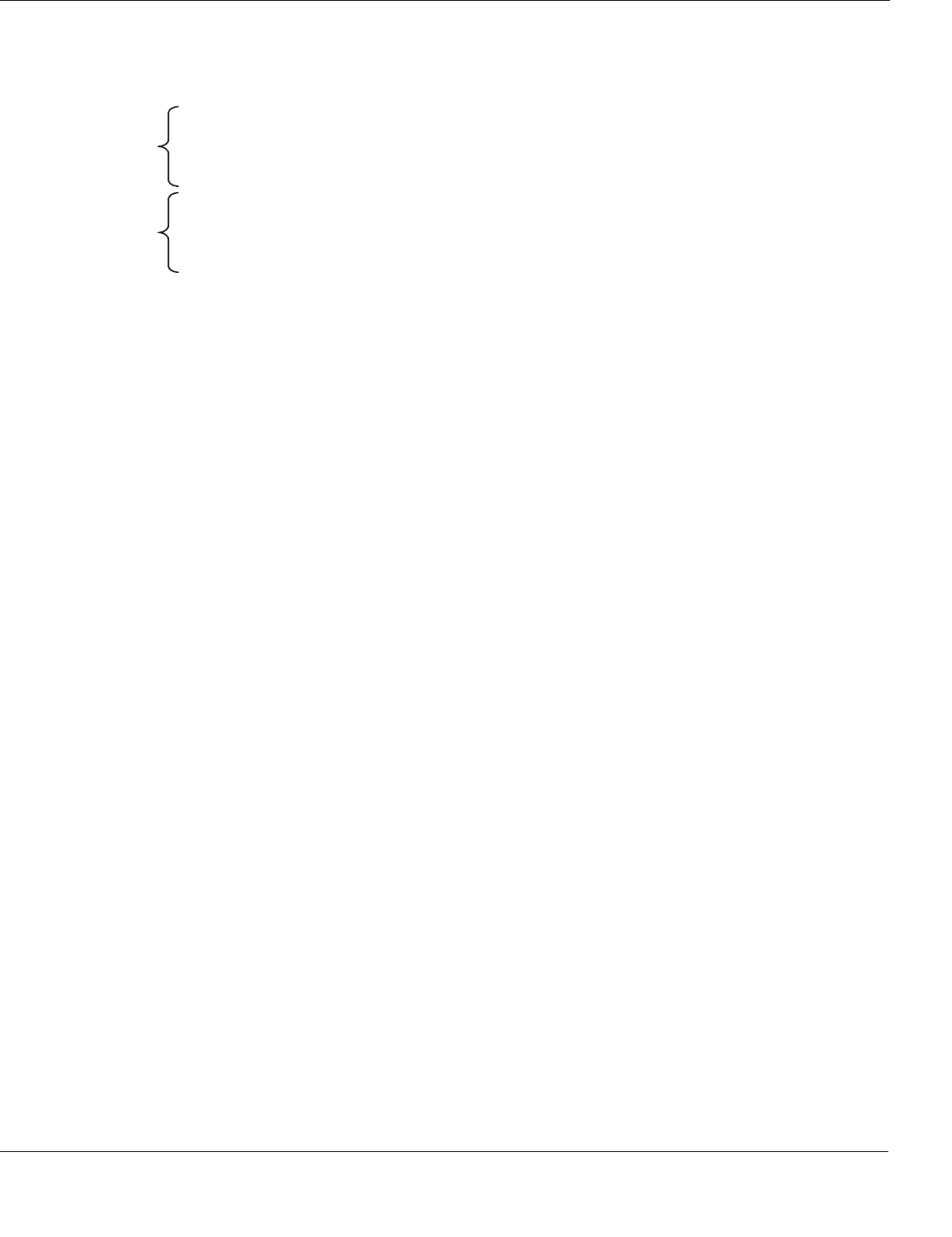
ptg6843605
opportunity cost – optimization
The Encyclopedia of Operations Management Page 246
strategic requirements of the business. In other words, the operations organization should always strive to make
decisions that are consistent with the competitive strategy being pursued by the strategic business unit. Hayes
and Wheelwright (1984, p. 31) developed the following list of “manufacturing strategy decision categories” and
divided the list into two sets – structure and infrastructure:
Structure
Capacity – Amount, timing, type
Facilities – Size, location, specialization
Technology – Equipment, automation, linkages
Vertical integration – Direction, extent, balance
Infrastructure
Workforce – Skill level, wage policies, employment security
Quality – Defect prevention, monitoring, intervention
Production planning/materials control – Sourcing policies, centralization, decision rules
Organization – Structure, control/reward systems, role of staff groups
Whereas structural decisions are physical, longer term, and more difficult to change, infrastructural decisions
are more tactical and require less visible capital investments (but can still be difficult to change). Hayes and
Wheelwright argue that these eight decision areas are closely interrelated and that “it is this pattern of structural
and infrastructural decisions that constitutes the manufacturing strategy of a business unit” (Hayes &
Wheelwright 1984, p. 32). This framework is closely related to the McKinsey 7S Model.
Other entries in the EOM – The balanced scorecard, strategy map, and causal map entries discuss strategy
process issues in more detail. The strategy map entry presents the time-based competition strategy. The mass
customization entry presents customization as a potential component of an operations strategy. Outsourcing to
achieve lower cost is also a component of an operations strategy. A focused factory is an important
manufacturing strategy, and the Service Profit Chain is an important service operations strategy. The push-pull
boundary and postponement entries deal with the customer interface, leadtime, and customization issues.
See 7S Model, agile manufacturing, balanced scorecard, blue ocean strategy, cash cow, catchball,
competitive analysis, core competence, first mover advantage, five forces analysis, focused factory, industry
analysis, mass customization, offshoring, operations management (OM), order qualifier, outsourcing, plant-
within-a-plant, postponement, push-pull boundary, resource based view, respond to order (RTO), robust, sand
cone model, Service Profit Chain, strategy map, supply chain management, sustainability, SWOT analysis,
technology push, time-based competition, vertical integration, virtual organization.
opportunity cost – The value of an alternative (opportunity) that was not taken.
When people have a choice between two or more alternatives, they will generally choose the best one.
However, choosing the best alternative means that they cannot choose the next best alternative. The opportunity
cost is the value of the next best alternative that must be sacrificed, i.e., “the value of the road not taken.”
For example, a firm can only make one product in a factory and decides to build product A instead of B.
Although it makes a profit on product A, it gave up the profit on product B. The forgone profit on product B is
called the opportunity cost.
For a more specific example, consider a factory that has one large machine (the bottleneck) that constrains
the plant’s production rate. The firm makes $1,000 per hour in gross revenue every hour the machine is running.
The firm currently has a setup time on this machine of one hour per day, which means that the firm could make
$1,000 more per day if the setup could be eliminated. The standard costing system assigns direct labor and
overhead to this machine at a rate of $200 per machine hour. However, the true cost of the setup is much more
than $200 per hour because of the opportunity cost (i.e., the lost gross margin).
See carrying cost, economics, overhead, setup cost, stockout, Theory of Constraints (TOC).
Optical Character Recognition (OCR) – A technology that enables a machine to translate images into text.
See Automated Data Collection (ADC), Electronic Product Code (EPC), lockbox.
optimization – An operations research term for mathematical techniques that find the best solution to a problem.
Optimization techniques can be classified as either unconstrained or constrained optimization.
Unconstrained optimization methods include calculus and numerical methods (search methods). Constrained
optimization methods include linear programming, integer programming, and many other mathematical
programming methods. Optimization techniques can also be classified as deterministic (has no uncertainty) or
stochastic (allows for uncertainty). For example, finding the optimal safety stock is usually modeled as an