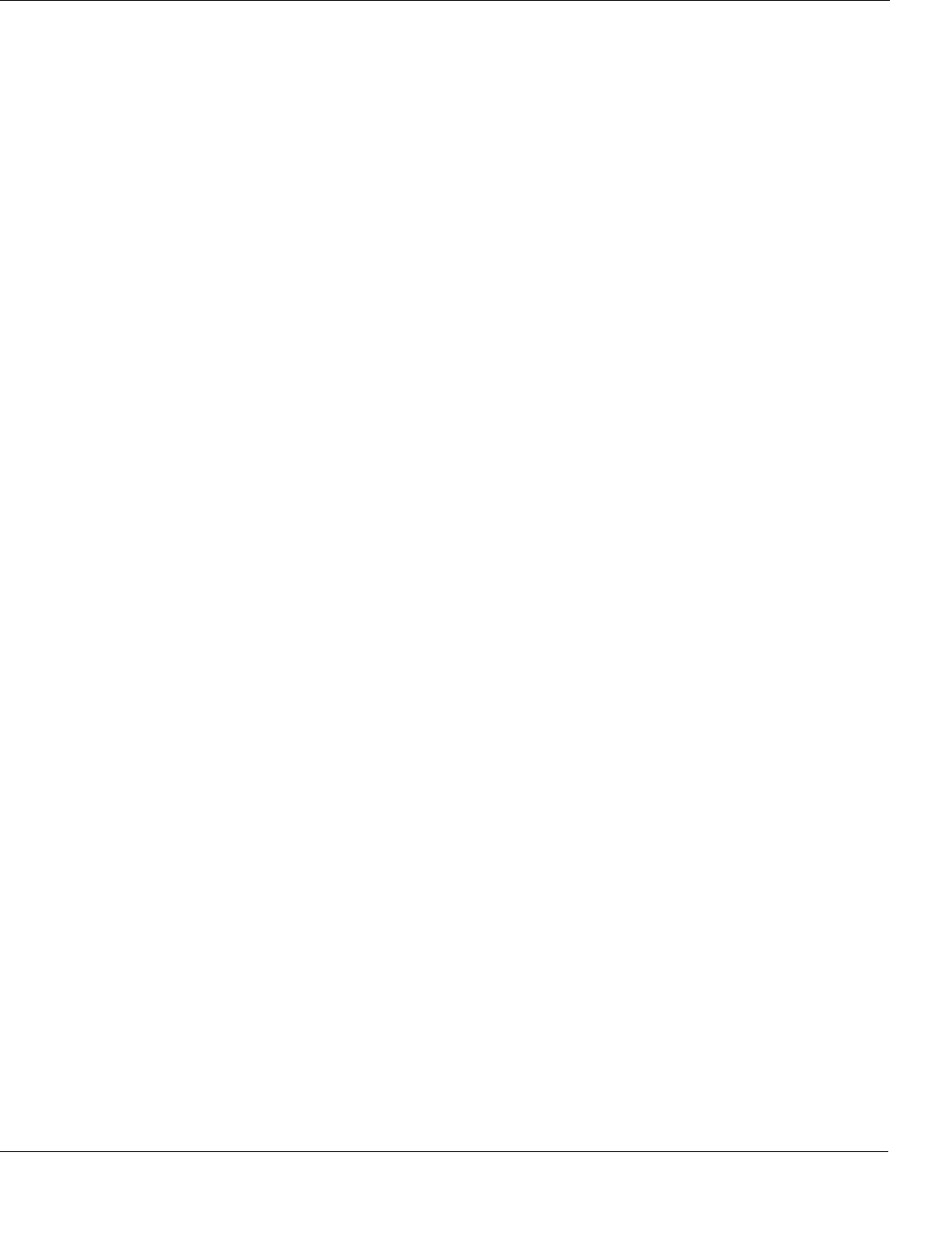
ptg6843605
physical inventory – pilot test
The Encyclopedia of Operations Management Page 262
physical inventory – The process of auditing inventory balances by counting all physical inventory on-hand.
A physical inventory is usually done annually or quarterly and usually requires that all manufacturing
operations be stopped. Cycle counting is better than the physical inventory count, because it (1) counts
important items more often, (2) fixes the record-keeping process rather than just fixing the counts, and (3)
maintains record accuracy during the year.
See cycle counting.
pick face – The storage area immediately accessible to the order picker.
See picking, warehouse.
pick list – A warehouse term for an instruction to retrieve items from storage; also called a picking list.
A pick list gives stock pickers the information they need to pick the right items, in the right quantities, from
the right locations, in the right sequence (route). These items may be for a specific production order, sales order,
or interplant order, or, alternatively, they may be for a group of orders. If the pick list is for a group of orders,
the orders need to be consolidated (assembled) from the items that are picked.
See backflushing, picking, warehouse.
picking – The process of collecting items from storage locations to meet the requirements of an order.
Warehouses usually have more outgoing shipments (customer orders) than incoming shipments (purchase
orders). This is particularly true for warehouses that serve retailers, because these warehouses are often used to
break out large orders from a few manufacturers into small orders sent to many retailers. The picking process,
therefore, has a significant impact on overall supply chain efficiency. Mispicks (errors in picking) directly
impact customers and customer satisfaction.
The ideal picking system will have low purchase and implementation cost, low operating cost, low cycle
time per pick, and high accuracy. The efficiency of the picking system is highly dependent upon the warehouse
system and policies for locating SKUs in the warehouse.
The type of picking process depends on many factors, such as product characteristics (weight, volume,
dimensions, fragility, perishability), number of transactions, number of orders, picks per order, quantity per pick,
picks per SKU, total number of SKUs, shipping requirements (piece pick, case pick, or full-pallet loads), and
value-added services, such as private labeling, cutting, or packaging. A pick to clear rule selects item locations
with the smallest quantities first to empty the bins more quickly. A pick to light system uses LED lights for
each bin and uses these lights to guide the picker to the next bin to be picked.
Picking is closely connected to the slotting policies, which are the rules used to guide employees to a bin (or
bins) when putting materials away. All Warehouse Management Systems (WMS) provide functionality for
both slotting and picking rules.
Voice picking (voice recognition) uses speech recognition and speech synthesis technologies to allow
workers to communicate with the WMS. Warehouse workers use wireless, wearable computers with headsets
and microphones to receive instructions by voice and verbally confirm their actions back to the system. The
wearable computer, or voice terminal, communicates with the WMS via a radio frequency local area network
(LAN). Directed RF picking uses radio frequency technologies to transmit picking, put away, replenishment,
and cycle count instructions to warehouse personnel using either handheld or truck-mounted devices.
See batch picking, carousel, discrete order picking, first pick ratio, flow rack, forward pick area, pick face,
pick list, private label, random storage location, reserve storage area, slotting, task interleaving, voice picking,
warehouse, Warehouse Management System (WMS), wave picking, zone picking.
picking list – See pick list.
piece work – Pay for performance based on the number of units produced rather than on the number of hours
worked or a salary; also called piece rate.
See gainsharing, pay for skill.
pilot test – A method used to test new software or a production process before it is fully implemented; for
information systems, a pilot test is also called a conference room pilot.
In the software context, the purpose of the pilot test may be to (1) evaluate for purchase, (2) evaluate for
implementation, (3) evaluate if the database and settings in the software are ready for implementation, and (4)
train users how to use the software. Ideally, the pilot test is conducted with actual data by actual decision makers