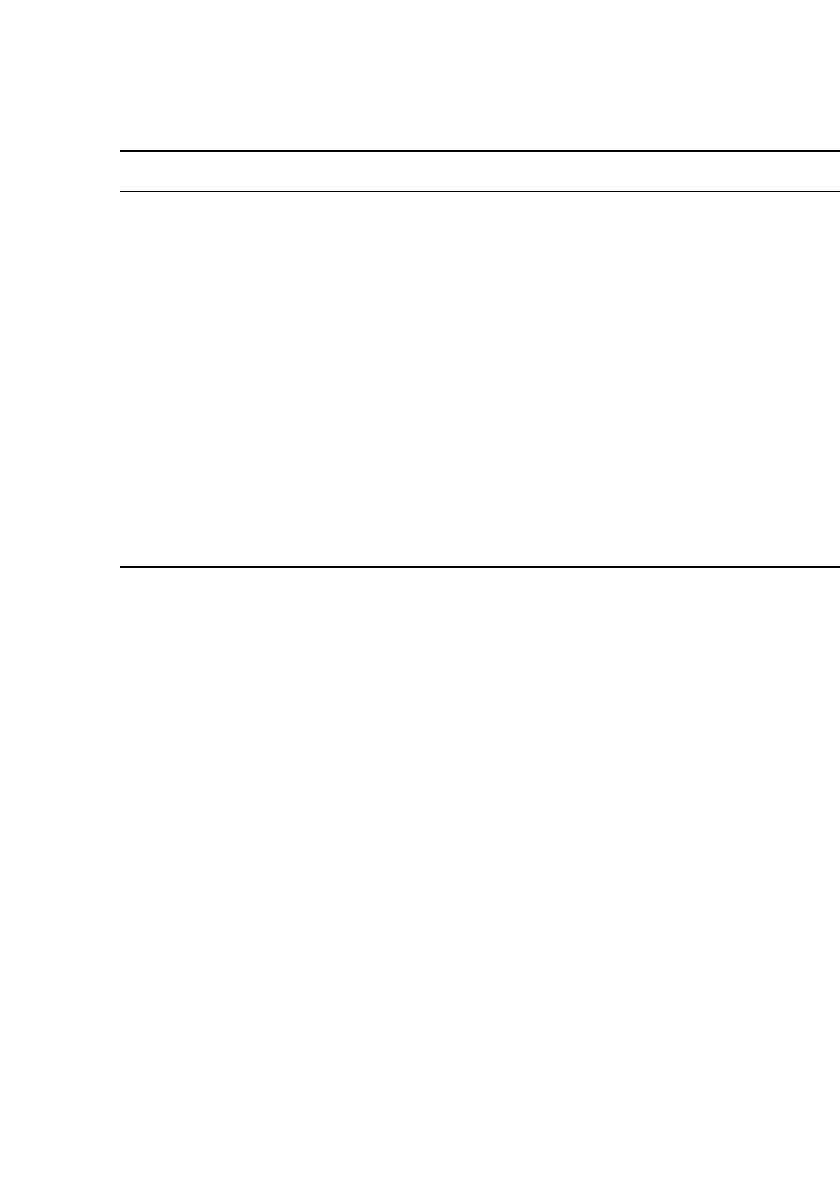
LEAD-ACID BATTERIES 23.3
The lead-acid battery is manufactured in a variety of sizes and designs, ranging from less
than 1 to over 10,000 Ah. Table 23.2 lists many of the various types of lead-acid batteries
that are available.
TABLE 23.2 Types and Characteristics of Lead-Acid Batteries
Type Construction Typical applications
SLI (starting, lighting, ignition) Flat-pasted plates (option:
maintenance-free construction)
Automotive, marine, aircraft,
diesel engines in vehicles and
for stationary power
Traction Flat-pasted plates; tubular and
gauntlet plates
Industrial trucks (material
handling)
Vehicular propulsion Flat-pasted plates; tubular and
gauntlet plates; also composite
construction
Electric vehicles, golf carts,
hybrid vehicles, mine cars,
personnel carriers
Submarine Tubular plates; flat-pasted plates Submarines
Stationary (including energy-
storage types such as charge
retention, solar photovoltaic,
load leveling)
Plante´;* Manchester;* tubular
and gauntlet plates; flat-pasted
plates; circular conical plates
Standby emergency power:
telephone exchange,
uninterruptible power
systems (UPS), load leveling,
signaling
Portable (see chap. 24) Flat-pasted plates (gelled
electrolyte, electrolyte
absorbed in separator);
spirally wound electrodes;
tubular plates
Consumer and instrument
applications: portable tools,
appliances, lighting,
emergency lighting, radio,
TV, alarm systems
*Now rarely used.
23.1.1 History
Practical lead-acid batteries began with the research and inventions of Raymond Gaston
Plante´ in 1860, although batteries containing sulfuric acid or lead components were discussed
earlier.
1
Table 23.3 lists the events in the technical development of the lead-acid battery. In
Plante´’s fabrication method, two long strips of lead foil and intermediate layers of coarse
cloth were spirally wound and immersed in a solution of about 10% sulfuric acid. The early
Plante´ cells had little capacity, since the amount of stored energy depended on the corrosion
of a lead foil to lead dioxide to form the positive active material, and similarly the negative
electrode was formed by roughening of another foil (on cycling) to form an extended surface.
Primary cells were used as the power sources for this formation. The capacity of Plante´ cells
was increased on repeated cycling as corrosion of the substrate foils created more active
material and increased the surface area. In the 1870s magnetoelectric generators became
available to Plante´, and about this time the Siemens dynamo began to be installed in central
electric plants. Lead-acid batteries found an early market to provide load leveling and to
average out the demand peaks. They were charged at night, similar to the procedure now
planned for modern load-leveling energy-storage systems.
Subsequent to Plante´’s first developments, numerous experiments were done on acceler-
ating the formation process and coating lead foil with lead oxides on a lead plate pretreated
by the Plante´ method. Attention then turned to other methods for retaining active material,
and two main technological paths evolved.
1. Coating a lead oxide paste on cast or expanded grids, rather than foil, in which the active
material developed structural strength and retention properties by a ‘‘cementation’’ process
(interlocked crystalline lattice) through the grid and active mass. This is generally referred
to as flat-plate design.
2. The tubular electrode design, in which a central conducting wire or rod is surrounded by
active material and the assembly encased in an electrolyte porous insulated tube, which
can be either square, round, or oval.