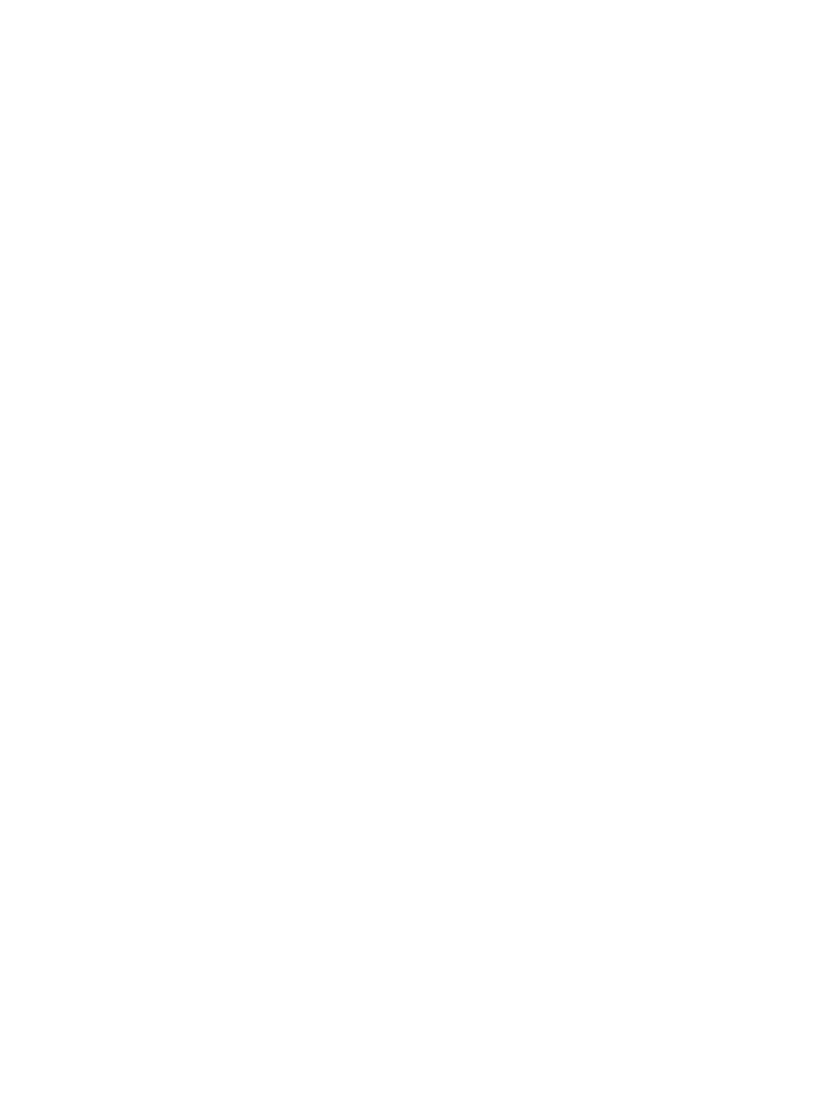
LEAD-ACID BATTERIES 23.19
Automotive lead-acid batteries (SLI) are produced mainly in high-volume plants with a
great deal of automation. Many modern factories are capable of producing quantities on the
order of 20,000 to 30,000 batteries per day. On average, an automated facility might require
less than 500 employees, including all staffing levels. The automation has been prompted
by environmental, reliability, and cost considerations.
23.3.1 Alloy Production
Pure lead is generally too soft to be used as a grid material. Exceptions that use pure lead
plates are some special, very thick plate Plante´ or pasted-plate batteries, some small spiral
wound batteries, some valve regulated cells and batteries (see Fig. 23.12c) and a cylindrical
cell. The latter were developed by Bell Laboratories (now part of Lucent Technologies) (see
Fig. 23.36).
12
The pure lead has been hardened, traditionally, by the addition of antimony metal. The
amount of antimony has varied between 5 and 12% by weight, generally dependent on the
availability and cost of antimony. Typical modern alloys, especially for deep-cycling appli-
cations, contain 4 to 6% antimony. The trend in grid alloys is to go to even lower antimony
contents, in the range of 1.5 to 2% antimony, in order to reduce the maintenance (water
addition) that the battery will require. As the antimony content goes below 4%, the addition
of small amounts of other elements is necessary to prevent grid fabrication defects and grid
brittleness. These elements, such as sulfur, copper, arsenic, selenium, tellurium and various
combinations of these elements act as grain refiners to decrease the lead grain size.
13–15
Some of the alloying elements, not previously described as grain refiners, fall into two
broad classes of elements that are beneficial or detrimental to grid production or battery
performance. Beneficial elements include tin, which operates synergistically with antimony
and arsenic to improve metal fluidity and castability. Silver and cobalt are also thought to
improve corrosion resistance. Detrimental elements include iron, which increases drossing;
1
nickel, which affects battery operation; and manganese, which attacks paper separators. Cad-
mium has been used in grid alloys to enhance processability in antimonial alloys to minimize
the detrimental effects of antimony. Cadmium, however, is not popular because of its toxicity
and difficulty of removal during lead recovery (recycling) operations. Bismuth exists in many
lead ore feedstocks and has been reported to both increase and decrease grid corrosion rates.
A second class of lead alloys has been developed which uses calcium or other alkaline
earth elements for stiffening. These alloys were developed originally for telephone service
applications.
2,16
Antimony from the grids is dissolved during battery operation and migrates
to the negative plates where it redeposits, which results in increased hydrogen evolution and
water loss. For telephone applications, more stable battery operation and less frequent wa-
tering were desired. The composition of the alloy depends somewhat on the grid manufac-
turing process. Calcium is used in the range of 0.03 to 0.20% but for corrosion resistance
the preferred range is 0.03 to 0.05%. A variation has been to substitute strontium for calcium.
Barium has been investigated but is generally felt to be detrimental to performance. Tin has
been used to enhance the mechanical and corrosion-resistant properties of the Pb-Ca alloys
and is usually used in the range of 0.25 to 2.0% by weight. The trend in nonantimonial
alloy development is toward ternary alloys (Pb-Ca-Sn) containing a minimal amount of tin
because of the expense of this element. Some batteries are produced with a quaternary
alloy—the fourth element being aluminum—to stabilize the drossing loss of the alkaline
earth element (calcium or strontium) from the molten alloy. Grain refining is done by the
alkaline earth metal, and no other elements (impurities) are desired. The properties of the
alloys are summarized in Table 23.8.
13