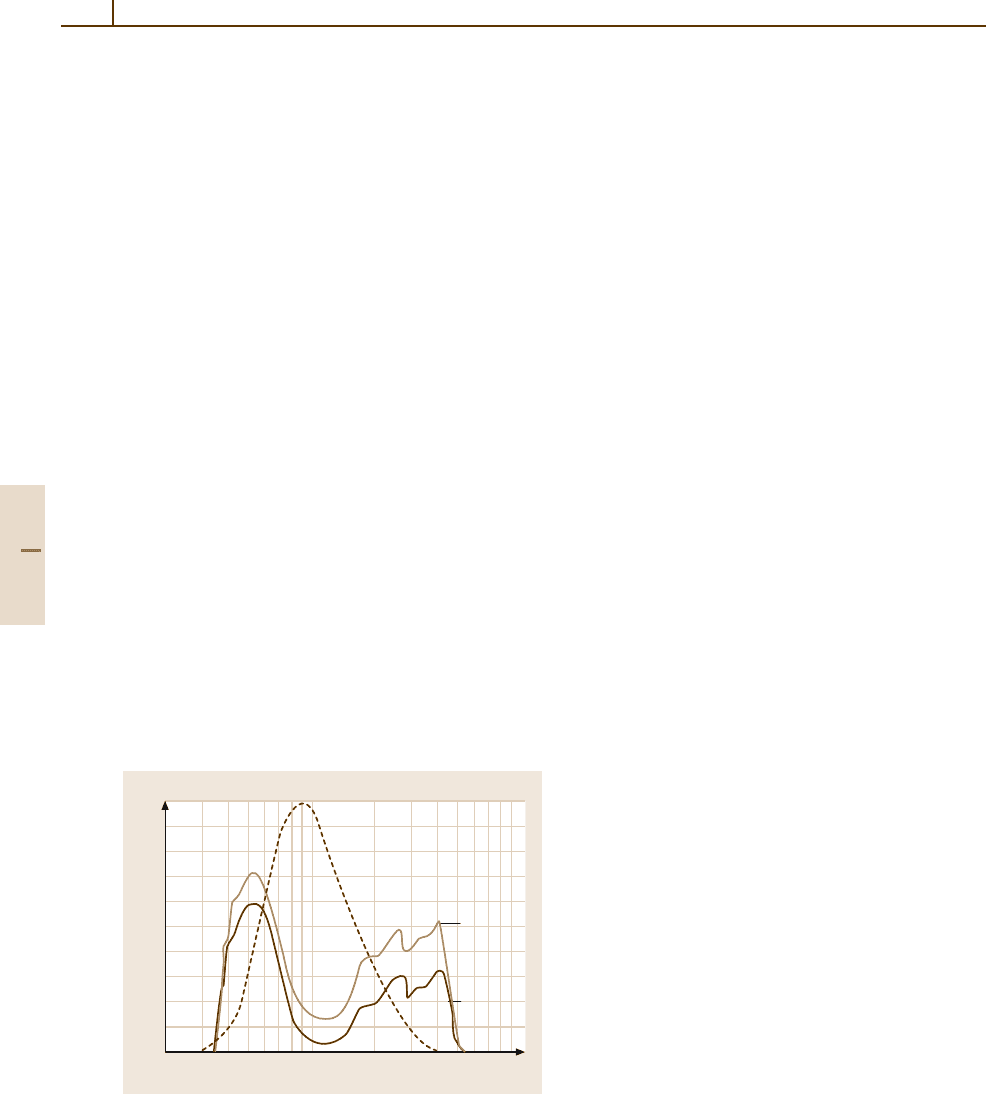
562 Part 3 Classes of Materials
certain special requirements, such ashigh electrical insu-
lation (e.g. alkali–lead silicate, 8095) or an exceptionally
low working temperature (e.g. the dense-lead glasses
8531 and 8532).
FeO-containing glasses (8512 and 8516) are fre-
quently used for hermetic encapsulation of electrical
switches and electronic components in an inert gas.
Hot forming and sealing are easily achieved by the ab-
sorption of IR radiation with an intensity maximum at
1.1 µm wavelength (Fig. 3.4-33). The presence of a pro-
portion of Fe
2
O
3
makes these glasses appear green. At
appropriately high IR intensities, they require consider-
ably shorter processing times than do flame-heated clear
glasses.
Compression Seals
A common feature of all compression seals is that the
coefficient of thermal expansion of the external metal
part is considerably higher than the thermal expansion
coefficients of the sealing glass and the metallic in-
ner partner (conductor). As a result, the glass body is
under overall radial pressure after sealing. This pre-
stressing protects the glass body against dangerous
mechanical loads. Because the compressive stress of the
glass is compensated by a tensile stress in the jacket, the
jacket wall must be sufficiently thick (at least 0.5mm,
even for small seals) to be able to permanently with-
stand such tension. If the thermal expansion of the
metallic inner partner is lower than that of the seal-
ing glass, an additional prestressing of the glass body
results.
Emission spectrum of a
tungsten–halogen lamp
Wavelength (nm)
Transmission (%)
100
90
80
70
60
50
40
30
20
10
0
200 500 1000 2000 5000 10000
Thickness
0.5 mm
Thickness
1 mm
Fig. 3.4-33 IR absorption of Fe-doped glasses compared
with the emission of a tungsten–halogen lamp at 3000 K
(in relative units). The transmission of reed glass 8516 with
thicknesses 0.5mmand1mmisshown
Glasses for Sealing to Ceramics
Dielectrically superior, highly insulating ceramics such
as hardporcelain, steatite, Al
2
O
3
ceramics, and forsterite
exhaust almost the complete expansion range offered
by technical glasses. Hard porcelain can generally be
sealed with alkaline-earth borosilicate glasses (for ex-
ample 8486), which are also compatible with tungsten.
Glass seals to Al
2
O
3
ceramics and steatite are possi-
ble with special glasses such as 8454 and 8436, which
will also seal to a 28Ni/18Co/Fe alloy. Soft glasses with
thermal expansions around 9 ×10
−6
/K are suitable for
sealing to forsterite.
Intermediate Sealing Glasses
Glasses whose thermal expansion differs so widely from
that of the partner component that direct sealing is
impossible for reasons of stress must be sealed with
intermediate sealing glasses. These glasses are designed
in such a way that for the recommended combinations
of glasses, the sealing stress does not exceed 20 N/mm
2
at room temperature (Table 3.4-21).
3.4.8.2 Solder and Passivation Glasses
Solder glasses are special glasses with a particularly
low softening point. They are used to join glasses to
other glasses, ceramics, or metals without thermally
damaging the materials to be joined. Soldering is car-
ried out in the viscosity range 10
4
–10
6
dPa s of the
solder glass; this corresponds to a temperature range
T
solder
= 350–700
◦
C.
One must distinguish between vitreous solder
glasses and devitrifying solder glasses, according to their
behavior during the soldering process.
Vitreous solder glasses behave like traditional
glasses. Their properties do not change during soldering;
upon reheating of the solder joint, the temperature de-
pendence of the softening is the same as in the preceding
soldering process.
Unlike vitreous solder glasses, devitrifying sol-
der glasses have an increased tendency to crystallize.
They change into a ceramic-like polycrystalline state
during soldering. Their viscosity increases by sev-
eral orders of magnitude during crystallization so that
further flow is suppressed. An example of this time-
dependent viscosity behavior is shown in Fig. 3.4-34
for a devitrifying solder glass processed by a spe-
cific temperature–time program. Crystallization allows
a stronger thermal reloading of the solder joint, up to
the temperature range of the soldering process itself
(e.g. glass 8596 has a soldering temperature of approx-
Part 3 4.8