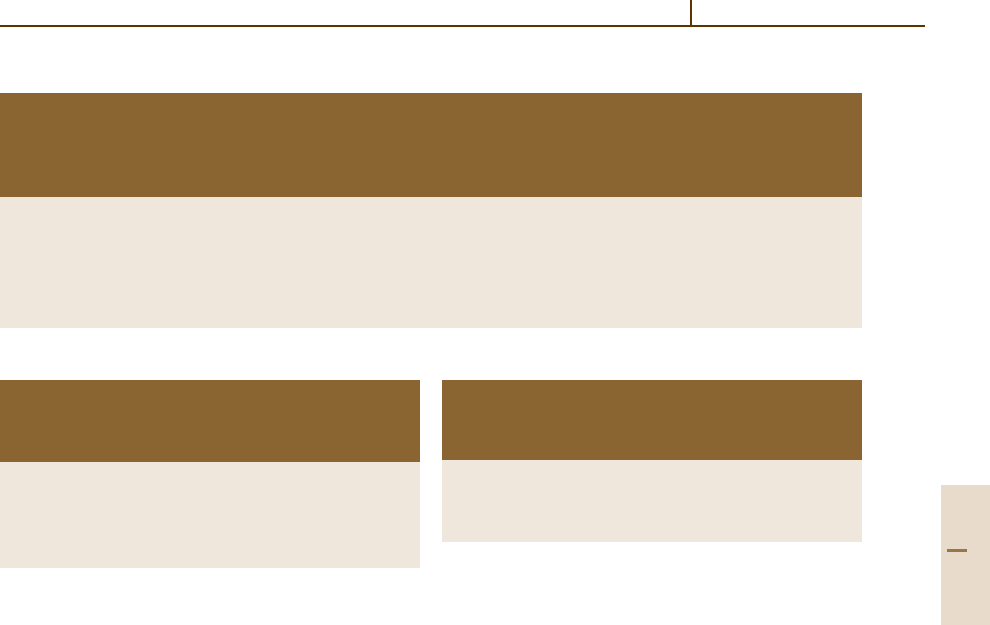
Glasses 4.4 Technical Specialty Glasses 533
Table 3.4-4 Hydrolytic classes according to DIN 12111 (ISO 719)
Hydrolytic Acid consumption of Base equivalent Possible designation
class 0.01 mol/l hydrolytic acid as Na
2
O
per g glass grains per g glass grains
(ml/g)(µg/g)
1 Up to 0.10 Up to 31 Very high resistance
2 Above 0.10, up to 0.20 Above 31, up to 62 High resistance
3 Above 0.20, up to 0.85 Above 62, up to 264 Medium resistance
4 Above 0.85, up to 2.0 Above 264, up to 620 Low resistance
5 Above 2.0, up to 3.5 Above 620, up to 1085 Very low resistance
Table 3.4-5 Acid classes according to DIN 12116
Acid Designation Half loss in weight
class after 6 h
(mg/100 cm
2
)
1 High acid resistance Up to 0.7
2 Good acid resistance Above 0.7, up to 1.5
3 Medium acid attack Above 1.5, up to 15
4 High acid attack Above 15
contaminants or some of their components may burn
in. Normal cleaning processes will then be ineffective
and the whole surface layer has to be removed (e.g. by
etching).
Desirable Chemical Reactions with the Glass Surface
(Cleaning and Etching).
Very strong reactions between
aqueous agents and glass can be used for the thorough
cleaning of glass. The complete ablation of a glass layer
leads to the formation of a new surface.
Hydrofluoric acid reacts most strongly with glass.
Because it forms poorly soluble fluorides with a great
number of glass constituents, it is mostly used only in
diluted form. The best etching effect is usually achieved
when another acid (e.g. hydrochloric or nitric acid) is
added. A mixture of seven parts by volume of water, two
parts of concentrated hydrochloric acid (c =38%) and
one part of hydrofluoric acid (c =40%) is recommended
for a moderate surface ablation of highly resistant
borosilicate glasses. When chemically less resistant
glasses (e.g. Schott 8245 and 8250) are exposed for
5 min to a stirred solution at room temperature, a surface
layer with a thickness of 1–10 µm is ablated, and a trans-
parent, smooth, completely new surface is produced.
Glasses can also be ablated with alkaline solu-
tions, but the alkaline etching process is much less
effective.
Table 3.4-6 Alkali classes according to DIN ISO 695
Alkali Designation Loss in weight
class after 3 h
(mg/100 cm
2
)
1 Low alkali attack Up to 75
2 Medium alkali attack Above 75, up to 175
3 High alkali attack Above 175
3.4.4.2 Mechanical and Thermal Properties
Viscosity
As described earlier, the viscosity of glasses increases
by 15–20 orders of magnitude during cooling. Within
this viscosity range, glasses are subject to three different
thermodynamic states:
•
the melting range, above the liquidus tempera-
ture T
s
;
•
the range of the supercooled melt, between the
liquidus temperature T
s
and the transformation tem-
perature T
g
, which is defined by ISO 7884-8;
•
the frozen-in, quasi-solid melt range (“glass range”),
below the transformation temperature T
g
.
The absence of any significant crystallization in
the range of the supercooled melt (see Fig. 3.4-1, line
segment 2) is of the utmost importance for glass for-
mation. Hence a basically steady, smooth variation in
the viscosity in all temperature regions is a fundamen-
tal characteristic of glasses (Fig. 3.4-4) and a crucial
property for glass production. Figure 3.4-13 shows
the strongly differing temperature dependences of the
viscosity for some glasses. The best mathematical ex-
pression for practical purposes is the VFT (Vogel,
Fulcher, and Tammann) equation,
log η(T ) = A +B/(T −T
0
), (4.5)
Part 3 4.4