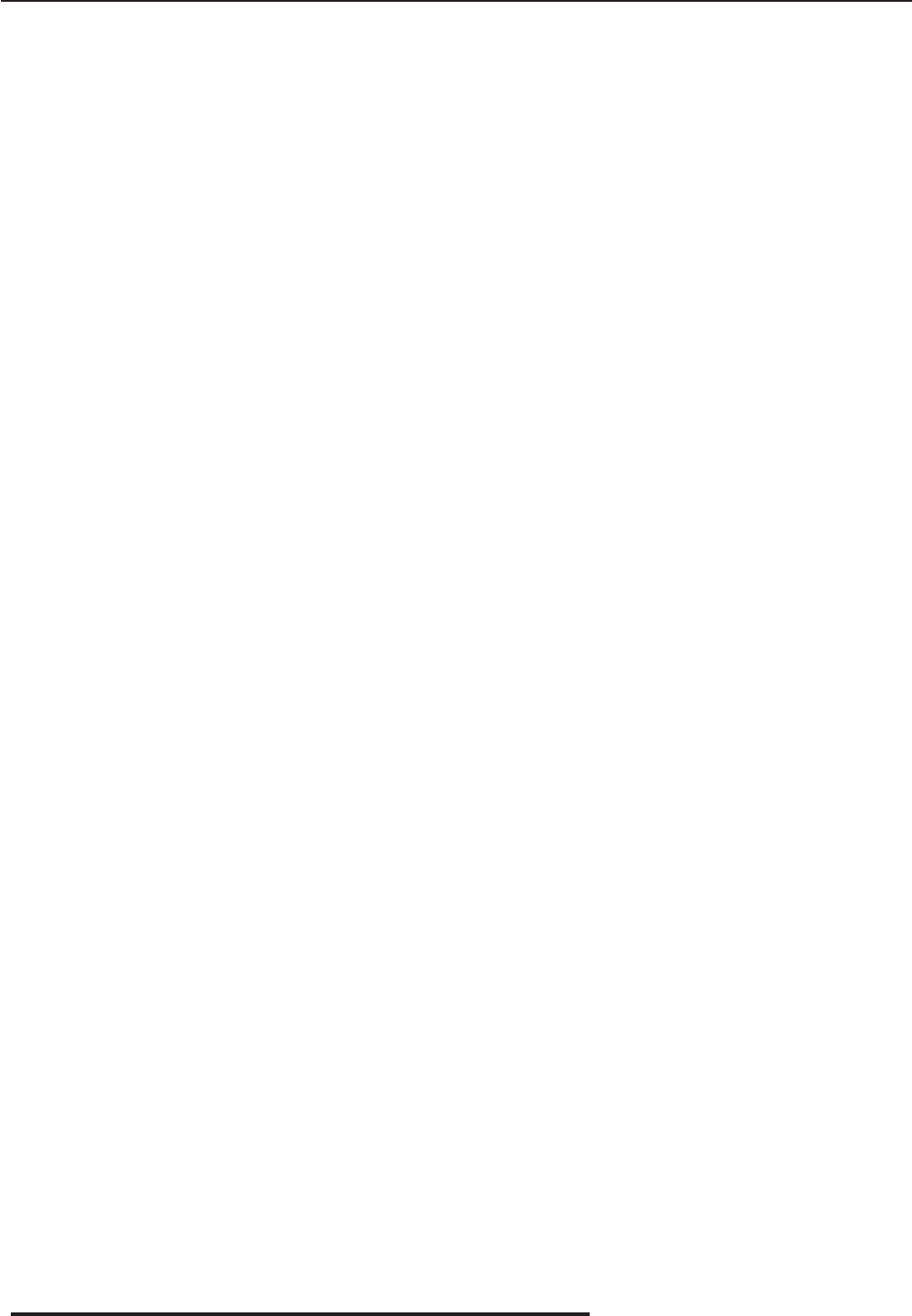
I l%2 ++30#(7%1* ? ( #.0-.03$- ? /0.,;8+%--.12</2010
2
83
ЭЛЕКТРОМЕТАЛЛУРГИЯ
превышал 70-75 % [2].
Наряду с повышением требований к размерным
факторам элементов подшипников, ужесточаются
требования к качеству заготовок сортового проката
по неметаллическим включениям по ГОСТ 801-78 (с
рядом изменений) и ASTM E-45 (метод А).
Вместе с тем, возросли поставки трубной заго-
товки для изготовления колец подшипников для под-
вижного магистрального железнодорожного транс-
порта. Потребность подшипниковых заводов в с
орто-
вом прокате в последнее время существенно повыси-
лась в связи с увеличением поставок крупных партий
подшипников в страны ближнего и дальнего зарубе-
жья.
Харьковский подшипниковый завод (ХПЗ) – один
из основных поставщиков подшипников в страны
СНГ, Балтии, Западной Европы и Южной Америки. В
России сооружается ряд заводов по сборке автомоби-
лей в
едущих фирм мира. В этой связи на ХПЗ прове-
дена реконструкция оборудования для изготовления
подшипников повышенного класса точности, удо-
влетворяющих жестким требованиям машиностро-
ителей. ОАО ХРЗ реализует также инвестиционный
проект, предусматривающий создание производства
подшипников для тяговых двигателей, что позволит
заводу занять лидирующие позиции в сегменте рын-
ка подшипников для железнодорожного т
ранспорта.
Цех № 3 завода «Днепроспецсталь», специали-
зированный по выплавке подшипниковой стали, обо-
рудован дуговыми печами ДСП-60, а также УКП и
ковшевым вакууматоров. Сталь разливают сифон-
ным способом на слитки массой 3,6 т [3]. Проектное
оборудование завода обеспечивает получение загото-
вок и сортового проката пяти размерных групп кру-
глого и квадратного профилей. Действовавшая техно-
логия не в
сегда позволяла выполнять заказы потре-
бителей металлопродукции по ГОСТ 801-75 и ASTM
E-45 (метод А).
Проведенный физико-химический аудит сквоз-
ной технологии позволил установить [4], что одной
из основных причин повышенного количества выпа-
дов образцов с высоким баллом загрязненности со-
ртового проката неметаллическими включениями,
прежде всего глобулярными труднодеформируемыми
алюминатами кальция, является использование фер-
ро
силиция ФС65 с не регламентируемым стандартом
высоким содержанием кальция (до 0,6 %) [5]. Осо-
бенности образования продуктов реакции раскисле-
ния стали при раздельном вводе Mn (ферромарганца)
и Si (ферросилиция) также влияют на выход сортово-
го проката с первого контроля.
Разработана и освоена технология выплавки ста-
ли ШХ15СГ-В путем научно обоснованной диверси-
фикации применяемых ферро
сплавов и режимов рас-
кисления и легирования металла. Установлено, что
при вводе ферросиликомарганца МнС17 вместо фер-
росилиция ФС65 (0,4-0,6 % Са) [4] образуются продук-
ты реакции раскисления металла в виде легкоплавких
силикатов марганца, которые наиболее полно ассими-
лируются шлаком при обработке стали на АКП шлако-
образующими смесями [5]. В совокупности с режимом
раскисления Al достигнуто повышение вых
ода годно-
го сортового проката с первого контроля по неметал-
лическим включениям до 90-92 % [4].
В период промышленного освоения техноло-
гии выплавку стали ШХ15СГ-В проводили в дуго-
вых электропечах ДСП-60 по двум вариантам, раз-
личающихся в основном присадками ферросилико-
марганца МнС17 в ковш (вариант 1) и сталелпавиль-
ную ванну (вариант 2). Ост
альные технологические
операции проводили в полном соответствии с разра-
ботанной технологической инструкцией. По техноло-
гии выплавки стали ШХ15СГ-В проведено 12 плавок
по варианту 1 (с присадкой МнС17 в ковш) и 24 плав-
ки по варианту 2 (с присадкой МнС17 в печь). При-
садка ферросиликомарганца МнС17 в стальную ван-
ну по варианту 1 составила в сре
днем 803 кг на плав-
ку при расходе ферросилиция ФС65 453 кг; по вари-
анту 2 – МнС17 847 кг и ферросилиция ФС65 450 кг.
Удельный расход ферросиликомарганца МнС17
в случае присадки его в печь (вариант 2) составил
13,82 кг/т жидкой стали, что на 0,54 кг/т больше, чем
в случае присадки в ковш (вариант 1). При этом плав-
ки по в
арианту 1 сопровождались небольшим повы-
шенным расходом ферросилиция ФС65 (7,49 кг/т
по варианту 1 вместо 7,34 кг/т по варианту 2). Та-
ким образом, выплавка стали по варианту 1 (присад-
ка всех ферросплавов в ковш) характеризуется не-
сколько меньшим общим расходом ферросплавов
относительно плавок по варианту 2, хотя это разли-
чие и не столь с
ущественно (с учетом оценки стои-
мости ферросплавов) в сравнении с технологиче-
ским преимуществом присадок ферросиликомар-
ганца МнС17 в ванну печи. Эффективность приме-
нения ферросиликомарганца МнС17 подтверждает-
ся результатами контроля качества сортового прока-
та стали ШХ15СГ-В по неметаллическим включени-
ям. Всего проконтролировано 165 образцов сортово-
го проката стали 20 партий из 12 плавок по в
арианту
1 и 374 образца от 52 партий 24 плавок стали по ва-
рианту 2. По варианту 2 достигнут более высокий вы-
ход годных партий с первого контроля сортового про-
ката плавок (98 против 90 % для плавок стали по ва-
рианту 1).
Меньший выход годного по варианту 1 обуслов-
лен в основном повышенным выпадом образцов III
группы по оксидам (13,8 %) при 100%-но
м выходе
годного по I, II, IУ и У группам. Для определения
качественных характеристик металла методами ма-
тематической статистики выполнена выборка пока-
зателей металла I и У групп, как наиболее различа-
ющихся по балльной оценке. Результаты статистиче-
ской обработки приведены в табл. [5].
Статистическая выборка показателей качества с
использованием критерия Фишера позволяет сделать
заключение об о
тсутствии статистических различий
двух технологических вариантов. Оба варианта пол-
ностью обеспечивают выход годного с первого кон-
троля как по 1, так и по У группе ГОСТ 801-78. Ме-
талл варианта 2 характеризуется стабильно низким