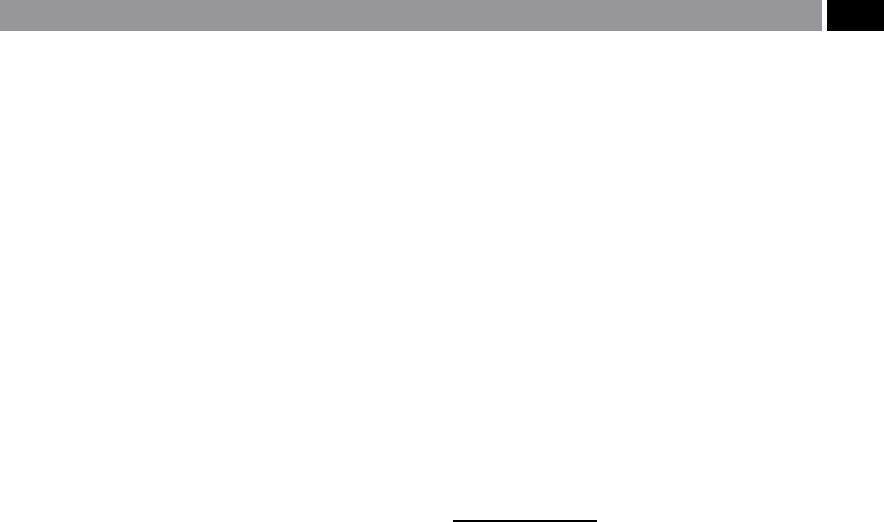
Today, anti-foaming agents tend to be ‘branch-
chained’ higher alcohols – being insoluble in wa-
t
er, or as mentioned above, silicones. Both alcohols
and silicones evidently disrupt the foam-producing
surface lm with that of an alternative gas-perme
-
a
ble surface lm, causing the surface-active liquid
surrounding each bubble to drain away, causing the
foam layer to collapse. If severe foaming occurs, anti-
foaming agents are not the answer, as eventually these
‘anti-foams’ get carried away, or ltered-out of the
coolant on the resultant machined: chips and swarf;
workpieces; or on coolant lters. e problem to
foaming may
not b
e due to the lack of ‘anti-foams’ ,
b
ut may be the result of air leaks that are sucking air
into the coolant stream. ese air leaks oen arise
around the pipe unions, or at pipe-connectors to
either the valves and pumps in the coolant delivery
system.
Microbiocides
Microbiocides are oen added to the aqueous-based
cutting uid as they help prevent the dramatic and un-
c
ontrolled growth of microbes in the coolant. Micro-
biocides uses are normally limited, owing to the po-
t
ential skin-care consideration – more will be said
concerning this very important topic later in the chap-
t
er, when ‘health-issues’ will be discussed.
8.4.3 Water Quality
e main constituent of any aqueous-based cutting
uid is obviously water and by nature, it is impure. e
impurity depends on the source: rain-; river-; spring-;
ground-water; etc. e water may also contain: dust
particles; oxygen; nitrogen; calcium and magnesium
salts; oen with smaller quantities of: ammonia; bo
-
r
on; ourine; iron; nitrate; strontium; aluminium;
arsenic; barium; phosphate; copper and zinc. Addi-
t
ionally, the water has in its presence micro-organ-
i
sms, such as: algae; bacteria; fungi and viruses (i.e.
see Fig. 203); although in dierent orders of magni-
tu
de. So, depending on its composition, water can
aect the aqueous-based cutting uid in many ways
and since the composition varies throughout the
year, these seasonal variations will have an eect on
its use. By far the greatest eect on the properties of
the cutting uid is caused by the hardness of the water.
Water’s hardness depends on the concentration of ele
-
ments
12
such as: calcium, magnesium and other heavy
metals like iron and manganese. Hard water may cause
a soapy deposit, which will eventually block lters, or
destabilise the emulsion and may have a detrimental
eect on the uid’s corrosion protection. Equally, so
water can be a problem, but for a dierent reason, in
this case it can promote foaming under ‘abusive’ ma
-
c
hining conditions.
e degree of alkalinity of the water can be ex-
p
ressed as a pH-value (
i.e. see the pH-scale shown in
Fig. 202b) and this is an important measurement, as
it aects its usage and can react to human skin
13
caus-
ing ‘serious complaints’ – more will be said concerning
these health issues later in the chapter. Alkalinity in
the main, aects the growth of microbes (i.e. see Fig.
203b) and the degree of corrosion protection aorded
12 ‘Water hardness levels’ , are calculated based upon the quantity
of ‘grains’ of hardness minerals the water contains. By way
of example, one grain of calcium carbonate, constitutes 17.1
parts million
–1
(ppm) per 3.785 litres (i.e. equivalent to a U.S.
gallon). ‘Salts’ such as sodium chloride and sodium sulphate
are found in hard water, where they contribute to corrosion, or
rust – if not ‘inhibited’. Moreover, the greater the cutting uid’s
solution salt content, the more coolant concentrate is required
to prevent subsequent corrosion. Further, coolant degradation
occurs with time and usage. For example, a new charge of
relatively so water admixed with coolant concentrate, will
initially have say, a 3-grain hardness, but aer one month’s use
its hardness will have increased to between 12–14 grains and,
aer two months this hardness will have increased still further,
to between 24–27 grains. is problem is exacerbated if the
water content evaporates, needing periodic cutting uid analy-
sis to maintain optimum coolant performance.One method of
signicantly reducing water of its hardness minerals, is to run
it through a water soener, which removes the calcium and
magnesium ions, replacing them with sodium ions, although
residue build-up will be signicantly reduced, corrosion may
now be a problem, so for this reason soened water is not
recommended when using water-miscible coolants. Other-
wise, boil the water – ensuring that no soener, or anti-cor-
rosion agents were present prior to using the condensed water
product (i.e from the boiling process). Deionized water is the
best source of pure water, as a deionizer removes all dissolved
minerals, creating distilled water.
13 ‘Human skin’ , varies from one body-region to another, but
generally, it has a pH-level slightly biased toward the acidic
region of the scale, at approximately 6.8 pH (e.g. a value of 7.0
pH is considered as ‘neutral’).
NB Skin also has a protective layer of natural oils, that act
to retard moisture evaporation, acting as a form of ‘defensive
shield’ against some forms of biological attack.
Cutting Fluids 397