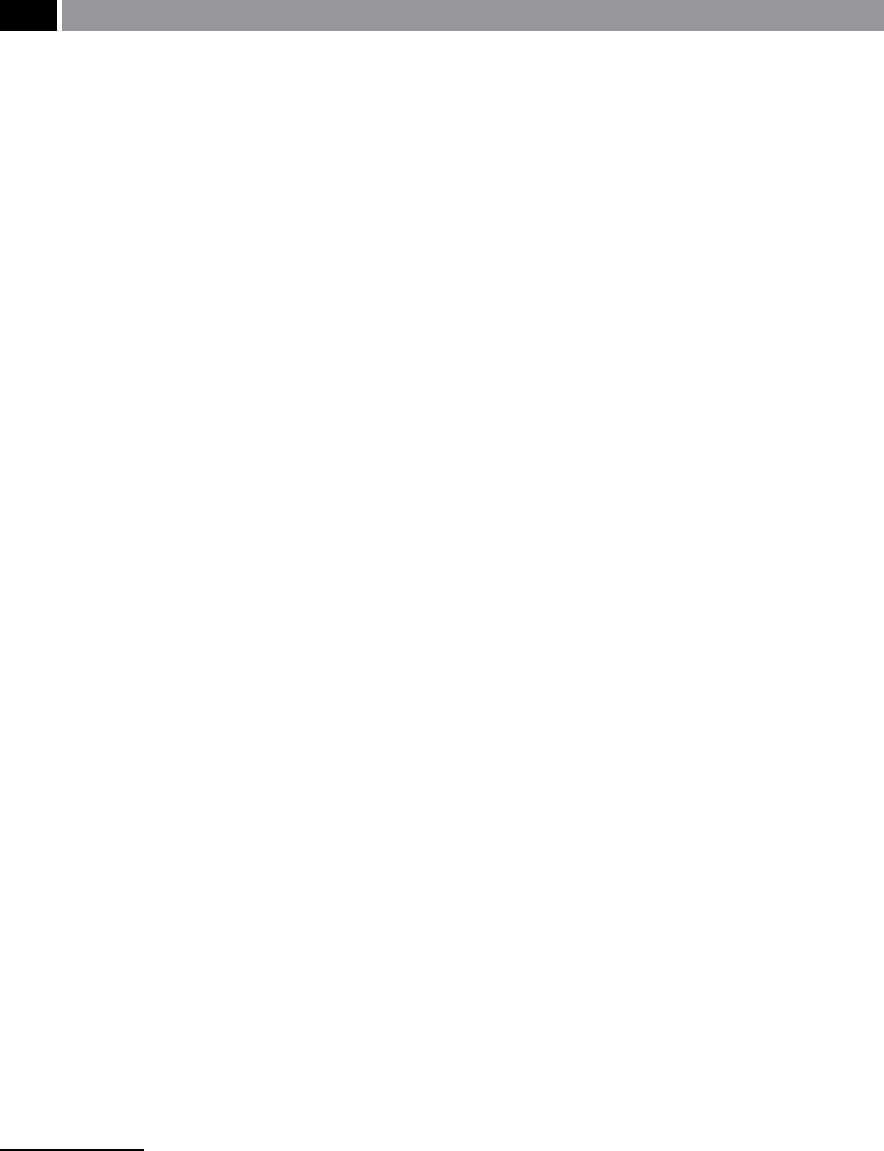
In Fig. 189c, a ‘white-layer’ (i.e. for this ferrous
drilled part, being a localised untempered martensitic
phase of 63 H
Rc
91
) exists beneath the recast and rede-
posited layer, in this case produced by a ‘dull’ drill’s
cutting lips and margins. Due to the fact that the recast
layer (i.e. heat-aected zone – HAZ) has a similar met-
a
llurgy to that of the ‘white-layer’ , with the delineation
of these ‘white-layers’ regions and their accompany-
ing HAZ’s are not clearly dened. is latter HAZ is a
complex metallurgical condition, comprising of some:
untempered martensite (UTM); over-tempered mar-
tensite (OTM), while beneath these layers, the bulk
substrate material remains unaected. e thickness
of these ‘white-layer’ zones is strongly inuenced by
both the actual plastic deformation created here and,
to a lesser degree, by the thermal inuence of the pas-
sage of the tool’s edge over the machined surface as
heat penetrates into the locality of the component’s
surface. Probably the worst ‘abusive machining’ condi-
tions that can exist, are when drilling holes in work-
hardening materials having long length-to-diameter
ratios (i.e. L/D ratios of >12:1) with inadequate cool-
ant supply, creating high levels of friction, this condi-
tion being exacerbated by an ineciency produced by
a ‘dulled’ drill’s cutting lips.
Virtually all tooling even the most sharp – the no-
table exception here being monolithic faceted natu-
ral diamond cutting edges, have a nite tip radius of
≈
8 µm (i.e. see Fig. 184 – high-lighting the tool tip
‘rounding eect‘), this results in increased forces and
tool wear, which can transform the surface metallurgy
by thermo-mechanical generation. e case has al-
ready been made concerning the fact that machining
processes impart residual stresses into the surface lay-
ers, as indicated in the schematically-represented mill-
ing conditions shown in Fig. 190 and graphically, in
Fig. 191 for a series of milling operations where preset
‘wear lands’ were generated on the cutter’s teeth prior
to workpiece machining. is latter case (Fig. 191) of
articially-inducing a controlled ‘wear land’ onto the
face-milling cutter’s individual tooth (i.e. with the other
teeth removed, hence, acting as ‘Fly-cutter‘), then aer
91 By way of comparison of this untempered martensitic ‘white-
layer’ phase, a conventional high-speed steel (HSS) milling
cutter’s teeth would have had a maximum hardness aer heat-
treatment of 62 H
Rc
, which clearly signies the true local hard-
ness of these ‘white-layers’.
several milling passes plotting the residual stress levels
from the surface and into the 4340 steel workpiece’s
substrate under standardised cutting data (i.e the steel
specimens having previously been quenched and tem-
pered to a bulk hardness of 52 H
Rc
). Hence, the eect
of these dierent induced tool wear rates and their
inuence in terms of their respective magnitudes and
depths, can clearly be seen. Even when the cutting edge
h
as ‘sharp tooth’ , a certain degree of tensile residual
stress was apparent in the immediate surface region.
Here, directly under this tensile stress zone, the stress
concentration changed to one of compression (i.e. to
a
depth of ≈50 µm). As each milling cutter tooth ank
became steadily more worn, the substrate compression
layer also increased in magnitude, which could lead to
considerable workpiece distortion, once the clamping
forces had been released – particularly if only one-side
of the part was milled (i.e. see Fig. 186b).
If the forces involved in the machining process ex-
ceed the ow stress, plastic deformation occurs and
the structure is deformed. In the case o ductile materi-
als, the plastic ow can create a range of degenerative
surface topography characteristics, such as: burrs; laps;
BUE residue; plus other unwanted debris deposits. If
this deformation becomes severe as a result of exces-
sive plastic ow, any grains adjacent to the surface
may become fragmented to such an extent that little,
or no metallic structure can be metallographically re-
solved, therefore ‘white-layering’ will result. Normally,
a ‘white-layer’ region extends to quite a small depth
b
eneath the surface, in the region of 10 to 100 µm, de-
pending upon the severity of the ‘abusive regime’ of
surface generation. Considering Fig. 191 once again,
as can be seen, the residual stress is indicated along the
vertical axis, here instead, it is alternatively possible
to superimpose a micro-hardness axis – see Fig. 191
circular inset graph. A note of care is required when
changing the vertical axis from residual stress to that
of micro-hardness, as they are two distinct quantita-
tive values. As mentioned the hardness prole closely
approximates that of the residual stress curve, however
in the latter case, instead of tensile stress at the in the
surface region, the sub-surface layer could equally be
compressive in nature.
‘White-layers’ must be avoided under all occasions,
because of the unstable metallurgical condition, com-
pounded by the fact that the these regions act as po-
tential stress-raisers for any critically-engineered com-
ponent and can lead to premature failure, or at worse,
catastrophic failure in-service.