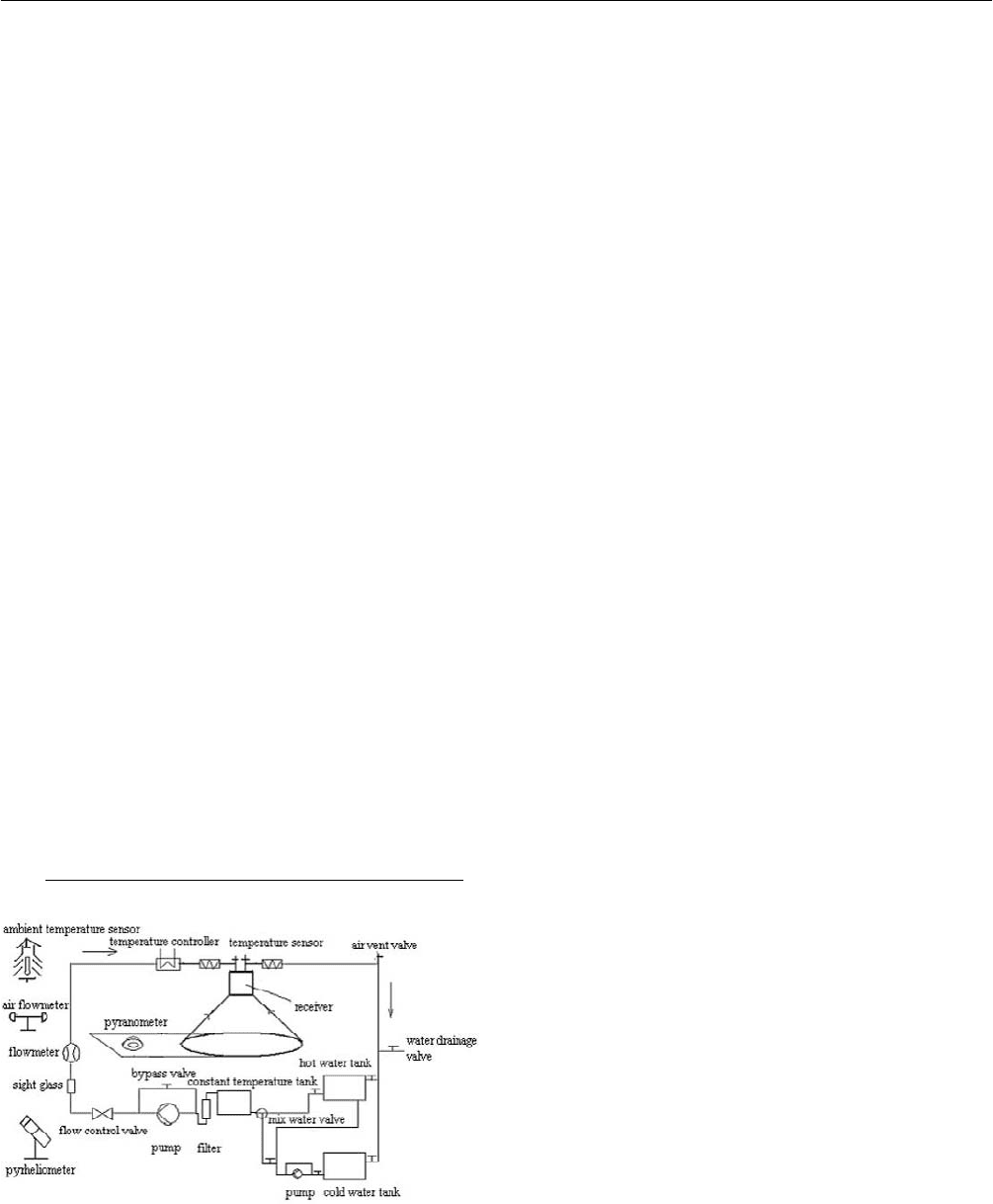
Proceedings of ISES Solar World Congress 2007: Solar Energy and Human Settlement
646
The working fluid entering through the inlet then flowed to
the front part of the receiver and then around the receiver
cavity towards the outlet along the pipe. The flux density
was maximized on the aperture because it is also the focal
plane. Therefore, the flow direction from the front to the
back along the absorber surface improves the solar
absorption. The absorber was surrounded by firebricks as
the heat insulation material.
The receiver aperture did not have a glass cover which
would reduce the absorption and reflection by the glass, on
the other hand increase the reflection, convection and
radiation heat loss from the absorber. The net effect of a
glass cover on the receiver aperture would be to improve
the receiver thermal efficiency.
The receiver was meant to be a simple test bed with few
attempts made to enhance the absorption and reduce the
heat losses. The main objective was to demonstrate the
multifaceted solar dish concentrator and to make thermal
performance tests.
Therefore, the absorber surface was not coated with a
selective coating. So that the ratio of the absorption to the
emission is relatively small and reflection losses are large.
A selective coating would also enhance the receiver thermal
efficiency.
High temperature and high pressure metal hoses were used
for the inlet and outlet union pipe.
2.3 Experimental System for Thermal Performance Tests
Fig. 3: Solar dish concentrator thermal performance test
schematics.
The solar dish concentrator thermal performance test bed is
diagrammed in Fig. 3. Water from the cold water tank was
pumped to the gas combustion heater where it was heated
to a high temperature and stored in the hot water tank. Hot
water was mixed with cold water in the mixing valve to the
desired temperature and then stored in the constant
temperature storage tank until being pumped to the receiver.
Thermal insulation was wrapped around the pipeline to
prevent heat loss with the heat tapes wrapped around the
pipeline to prevent the heat loss. The constant temperature
tank not only mixed the hot and cold water to keep the
temperature uniform, but also buffered flow fluctuations.
The flow fluctuations were less than 0.9%, so the flow was
easily controlled to steady or quasi steady conditions.
Temperatures were measured by Pt100 resistance
thermometers on the cold tank, the hot tank, the constant
temperature tank and the receiver inlet and outlet. The
accuracy of the temperature measurements was within the
±0.1 K. The temperature sensors were installed within 200
mm of the receiver inlet and outlet with the pipeline in
front of and behind the sensor insulated by rock wool. The
Pt100 RTD which measured the ambient temperature was
placed in a well ventilated shelter less than 15 m from the
solar dish concentrator.
The flow rate was measured by an electromagnetic
flowmeter type DE43F produced by ABB corporation with
a measurement error less than ±0.5%.
The beam normal radiation was measured by a
pyrheliometer which tracked the sun. The pyrheliometer
was placed on the north of the solar dish concentrator
where no structures would affect the readings. The
pyranometer was mounted on the back of receiver so that it
tracked the sun with the moving solar dish concentrator to
measure the total solar radiation. The pyranometer was
mounted so that the solar dish concentrator structure did
not shade it.
The test data was acquired in a HP34970A data logger
every 10 seconds.
Water was used as the heat transfer fluid at inlet
temperatures of 31ć, 45ć, 53ć and 71ć with four
testing points per temperature.