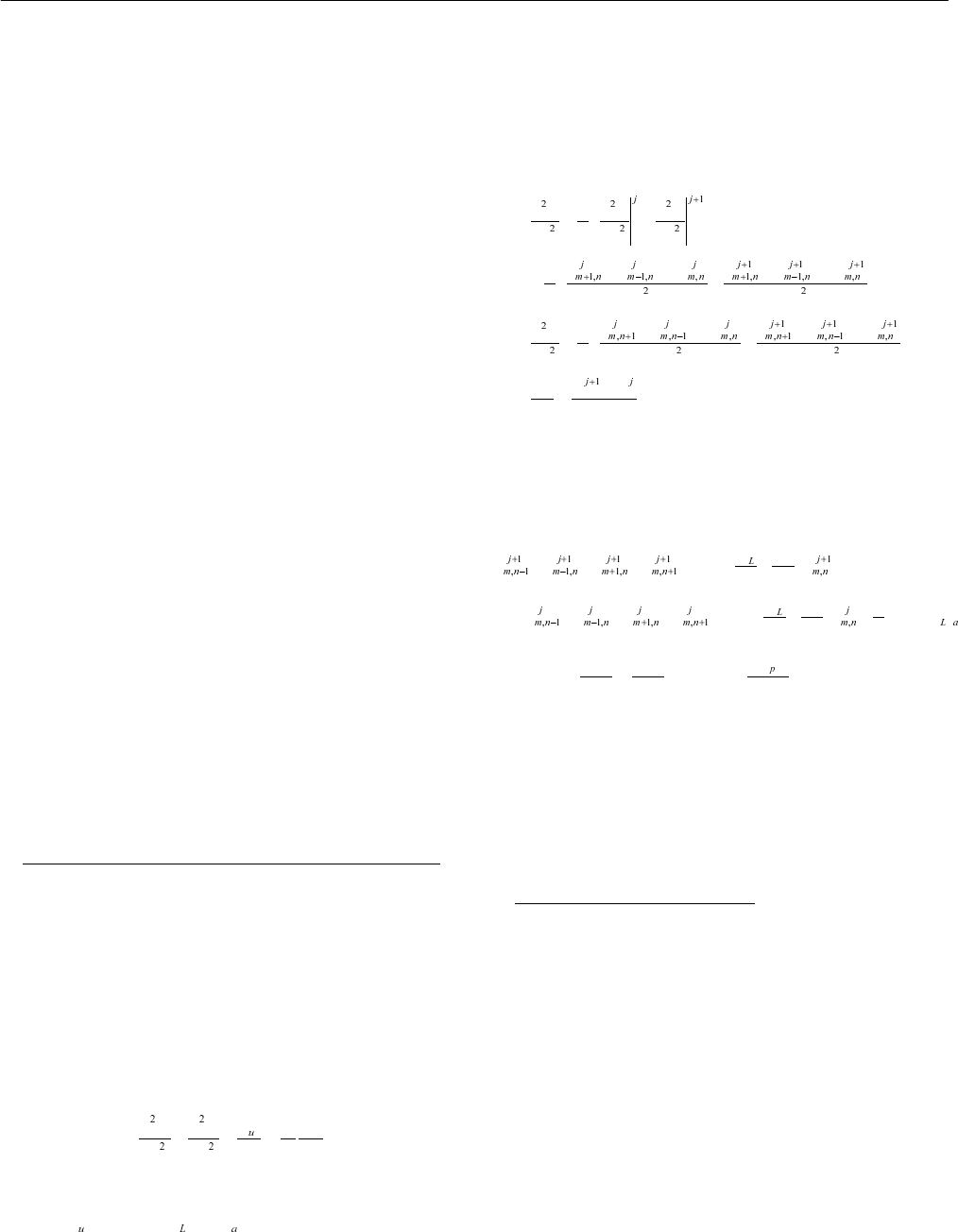
3 SOLAR COLLECTOR TECHNOLOGIES AND SYSTEMS
685
tube of 9.52 mm diameter was soldered at the back of each
absorber plate in serpentine form. Adequate insulations
were provided at the back of the collector but no glass
cover was used on the top surface i.e. unglazed collector.
There is a bypass line from the exit of the first
evaporator-collector to the exit of second
evaporator-collector, which remains closed or open
depending on the solar irradiation. Refrigerant R-134a is
used as the working fluid due to the better thermodynamic
and environmental performance.
A thermostatic expansion valve is used for the system, which
maintains constant superheat at the inlet of the compressor
by regulating the mass flow rate of refrigerant with the help
of a feeler bulb. Actually, the feeler bulb is a remote bulb of
the thermostatic expansion device that controls the degree of
superheat by controlling the pressure. An open
type-reciprocating compressor is used for the system, which
is directly coupled to a three-phase induction motor.
The three applications (air-conditioning, water heating and
drying) of this system can be served simultaneously or
independently. A frequency inverter is utilized to vary the
compressor speed, to have proper matching between the
evaporator load (cooling requirement) and condenser load
(heating requirement) and thus improves the efficiency.
Different motor speeds in different operating conditions
lead to different refrigerant mass flow rate in the
evaporator-collector
The details of the evaporator-collectors are shown in Figure 2.
2.
MATHEMATICAL MODELING AND SIMULATION
A transient mathematical model of the system has been
developed. Two-dimensional simulation is applied in the
part of evaporator-collector to obtain more accurate
collector performance prediction. By considering an
element of the collector, a two-dimensional partial
differential equation is developed to describe the collector
performance, as shown in equation 1
1
q
TT T
ktxyδα
∂∂ ∂
++=
∂∂∂
(1)
where
() ( )qI UTTτα=−− and 1τ =
Equation 1 is solved by making use of Crank-Nicholson
method and appropriate boundary conditions.
Using Crank-Nicholson method, the governing equations
for the evaporator-collector are expressed as:
1
2
22
1
2
22
1
2
TTT
xxx
TT TTT T
xx
TT TTT T
T
yy y
TTT
tt
⎛⎞
∂∂∂
⎜⎟
=+
⎜⎟
∂∂∂
⎝⎠
⎛⎞
+− +−
=+
⎜⎟
⎜⎟
ΔΔ
⎝⎠
⎛⎞
+− +−
∂
=+
⎜⎟
⎜⎟
∂Δ Δ
⎝⎠
−∂
=
∂Δ
The Finite difference approximation for the partial
differential equation is derived as:
()
()
2
4
22
4
U
p
TTTT T
rr
U
p
TTTT T IUT
rr r
α
⎛⎞
++++−−−
⎜⎟
⎝⎠
⎛⎞
=− + + + + + − − +
⎜⎟
⎝⎠
where
22
kk
r
xy
δδ
==
ΔΔ
and
c
p
t
ρδ
=
Δ
After setting the initial condition, variation of temperature
distribution on the evaporator-collector can be calculated
by Gauss-Seidel iteration method using the finite difference
approximation.
3.
RESULTS AND DISCUSSION
Results were obtained for both simulation and experimental
data. Meteorological data for a typical day in Singapore is
shown in Figures 3.1 and 3.2.
In Fig. 4, predicted useful energy gain (Q
u
) by collector
was plotted against time. Useful energy gain(Q
u
) is the
combination of energy gain from irradiation and the energy
gain from ambient. While the energy gain from ambient,
Q
surrond
is mainly effected by ambient temperature. It shows
that predicted Q
u
has a reasonably good agreement with
experimental values. As seen from Figure 4, Q
u
shows a
slightly declining trend with the reduction of irradiation.