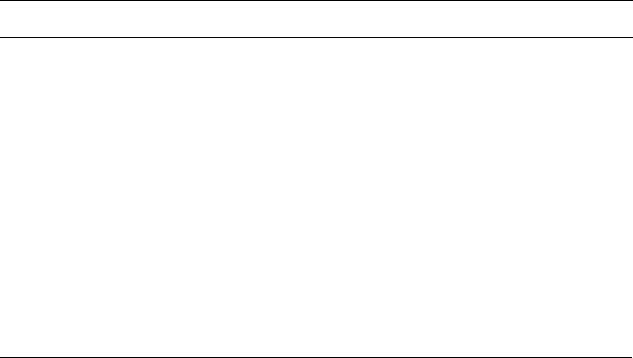
644 SEMT Pielstick (MAN Diesel Group)
Cylinder head: a vermicular cast iron component attached to the water
jacket and to the liner by eight tie-bolts anchored in the crankcase bosses.
Valves: both inlet and exhaust valves have a tight guide bush and the
exhaust valves feature a turning device. The entire water flow across the cyl-
inder head passes through the exhaust valve cages, substantially decreasing the
valve seat temperature.
Fuel injection: the injectors are cooled by a separate freshwater system.
The fuel pumps provide a pressure exceeding 1000 bar.
Camshaft: the bearings are secured with four bolts directly below the injec-
tion pump supports, an arrangement which avoids the transmission of injection
stresses to the crankcase. Each camshaft and its bearings can be removed later-
ally from the side of the engine. The fuel pump driving gear design secures a
low contact pressure between cam and roller.
Turbocharging: a patented MPC system represents a compromise between
impulse and constant pressure systems, and also fosters easier maintenance of
piping and expansion bellows.
Comparison of PC2.6-2 and PC2-6B parameters
PC2.6-2 PC2-6B
Bore, mm 400 400
Stroke, mm 460 500
Swept volume, dm
3
57.8 62.8
Max. combustion pressure, bar 137 (V-cyl)
142 (L-cyl)
150 (V-cyl)
150 (L-cyl)
Nominal power, kW/cyl 550 615
Speed, rev/min 500/514/520 500/514/520
Mean piston speed, m/s 7.7–8.0 8.3–8.6
Mean eective pressure, bar 22.9 23.5
Specic fuel consumption, g/kW h 183 182
PC2-6B LoW-PoLLuTANT VErSioN
In creating a low-pollutant version of the PC2-6B engine, SEMT Pielstick
aimed to find a compromise between low emission levels, first cost and run-
ning cost using proven solutions. The following nitrogen oxides (NOx) reduc-
tion techniques, investigated earlier on other prototype engines, were applied:
l Increased compression ratio: raised to 14.8 instead of 12.7:1 on the
standard engine.
l Retarded fuel injection: 4° before TDC instead of 11°.
l Water/fuel emulsion injection: 30 per cent/70 per cent ratio.