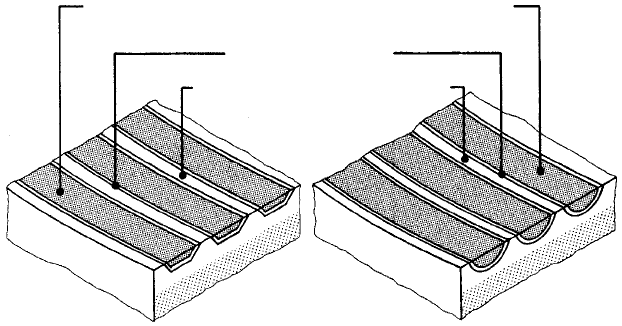
658 Sulzer (Wärtsilä)
in a reduction of the dynamic stresses of around 20 per cent. The bolts are
hydraulically tightened for easier and faster maintenance procedures.
Helix-controlled fuel injection pumps (Figure 26.12) are provided for each
cylinder, with fuel leakage into the lubricating oil prevented by an oil barrier at
the lower end of the plunger sleeve. Depending on the engine application, helix
control edges can be chosen for constant or variable injection timing (CIT or
VIT). The simple arrangement of short high-pressure fuel pipes to the injection
valves, together with the circulation of preheated fuel oil up to the level of the
pumps, underwrites routine pier-to-pier operation on heavy fuel (with appro-
priate circulation and preheating).
The injection valves (Figure 26.13) are equipped with sleeve-type noz-
zles cooled by freshwater and provided with rounded-off inner edges of the
spray holes (Figure 26.14). Rounded-off spray holes are traditional for Sulzer
nozzles and reportedly result in a more stable spray pattern over longer service
periods with a narrower scatter of injection rates between individual cylinders.
A more corrosion-resistant sleeve material was introduced to replace the origi-
nal material whose punishment threshold was not large enough to cope with
corrosion attacks by insufficiently treated cooling water (as a result, some tip
breakages occurred).
Plunger seizures initially occurred on Z40 engines due to insufficient clear-
ance (either through manufacturing with too small a clearance or reduction of
clearance in heavy fuel service as a result of the tendency of the material used
earlier to grow at higher temperature levels). An increased plunger clearance
and a changeover to a new material specification for the plungers, supported
by stricter quality control, proved to be design remedies. Operationally, ship-
yards and operators must take care that no undue impurities are present in the
Barrier layer : Ni
Shell back: Steel
Running layer 2: Al with 6% Sn
Running layer 1: Pb Cu Sn-(or Sn Sb-) overlay as groove
fillings
FIgure 26.11 Features of ‘rillenlager’-type bearings: thickness of the Al/Sn running
layer no. 2 is a few tenths of a millimetre; depth of grooves is a few hundredths of a
millimetre; grooves are laid as a helical thread; shape and dimension of grooves may
vary, depending on the manufacturer